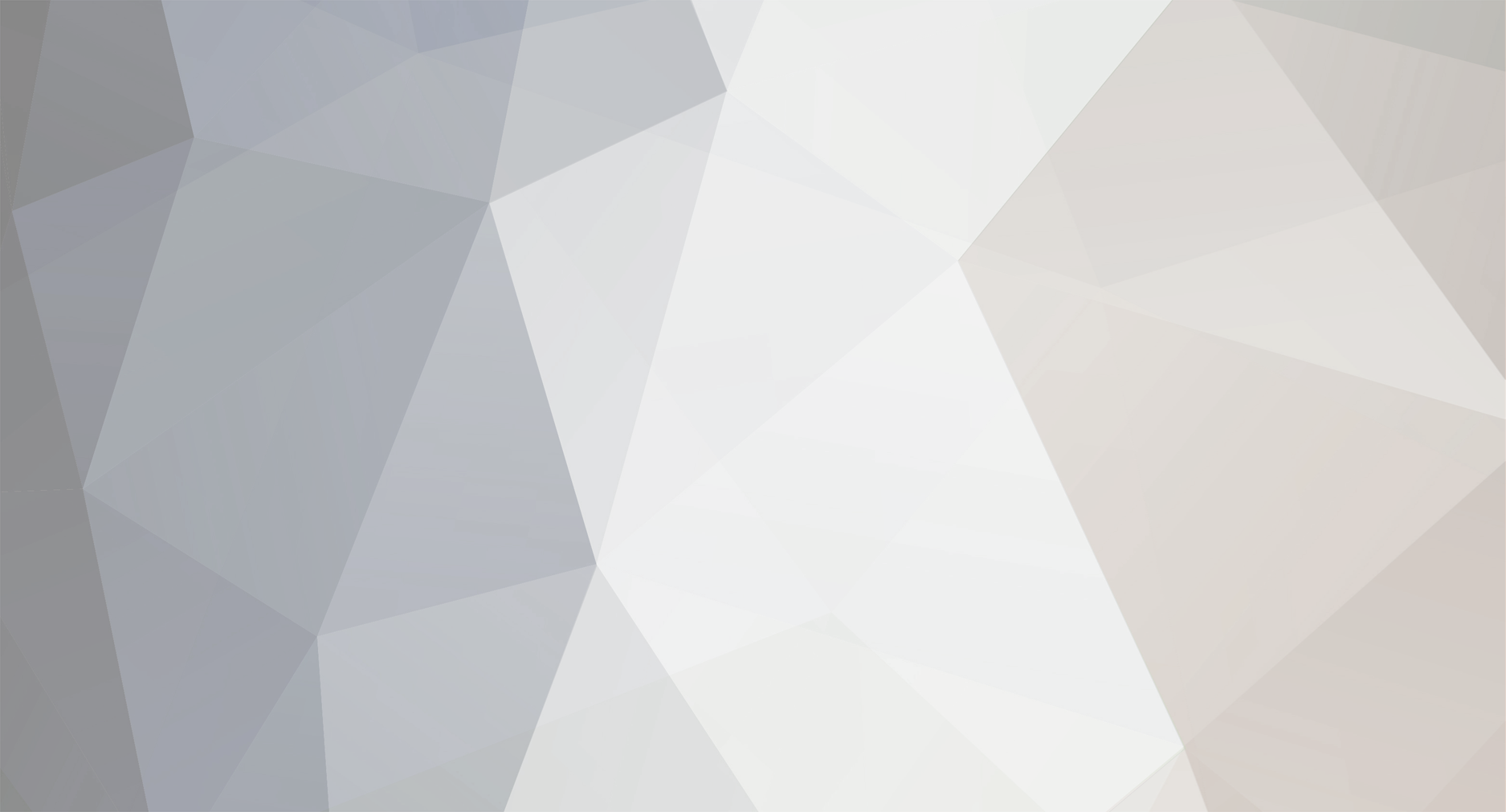
JayW
-
Posts
2,316 -
Joined
-
Last visited
-
Days Won
26
Content Type
Profiles
Forums
Events
Posts posted by JayW
-
-
-
On 2/14/2025 at 6:48 PM, Oldbaldguy said:
Not sure I understand your vexation, Jay. Is it not true that this is your FIRST attempt at a wholly 3D model? Of course there have been some glitches - it would be scary had there not. I doubt there is anyone else on this site right now who could have done what you have so far. This is not to say that the next guy to take on such a project will not blow the rest of our socks off, but dude, honestly. I’m just happy to be able to tag along in abject wonder as this thing grows out of nothing and frankly could not give two shites if something is .030 whatevers out of whack. You are building a masterpiece the first time out - own it and revel in it.
This is a really nice thing to say OBG. Appreciated! And yes I guess I am guilty of being a perfectionist and maybe even a pessimist in this effort. Which could annoy some of you. Understand though that the further I get into this journey, the more pressure I feel. I am so afraid of compromising what has so far been a long and pretty successful effort. I am very very vested in this.
And let's give credit where credit is due. Peter Castle (Airscale to us) started this whole thing off on LSP with an effort to 3D print a P-39 in 1/18 scale. This effort did not go to completion, but since then he has done a wonderful Hawker Sea Fury - not entirely 3D printed but a whole lot. His P-39 effort was my inspiration to do this 3DP P-51B. That and some spectacular 3DP parts made for me on my 1/18 F4U-1A.
As for that .03 inch error on the aileron - it was worse than you'd think. I have had to do some digital design magic to get it under control. That discovery came at a time where I have had one problem after another. Am hoping for calmer waters from here on out.
-
On 2/11/2025 at 1:13 PM, Thunnus said:
I would recommend trying Mr Hobby Aqueous H326 (acrylic) or Mr Color C326 (lacquer), which are both FS15044 Blue. I used the Aqueous version on my Razorback and Corsair builds...
Well John - in addition to trying to gin up my own formula for FS15044 blue with Tamiya colors, and not being very impressed, I looked for the Mr. Color C326. Without success. Where do you get these?
On 2/12/2025 at 9:59 AM, chuck540z3 said:If you live in the US, MRP is readily available from Sprue Bros.
Right Chuck - so I ordered some MRP 300 (FS15044) from Sprue. It's on its way. Thanks for that!
The fuselage paint disaster is for the most part in the rear view mirror, including the emotional damage, although it has put a serious delay in my build schedule. I wait for stencils from Thunnus, and the MRP blue. This time I will paint it up right.
While waiting, I actually finished the wing painting. Which was a pretty big deal. There were minor part breakage casualties, but not paint casualties. Even though the insignias were painted with the Model Master enamel (applied before the fuselage disaster), they held up to careful and gradual airbrush flat clear final coat. Whew!!
Some pictures (god this wing is just huge; difficult to take good pics):
The work area is not easy on the eyes, and for that I am sorry. The last picture shows well the characteristic droop of the B/C extended inboard leading edge.
Details:
Above are lower fuel tank access panels, which are not painted silver. Supposed to be that way. And of course the few hundred protruding head fasteners discussed a while back. These are pretty lumpy panels due to the aluminum skin disbonding issues I had with them. But the contrasts of the invasion stripes and the flat finish makes it not as noticeable.
Above you see the ID lights, now on the RH wing where they belong. Recall a couple of posts ago I was in a panic because I had them on the LH wing. This re-location came out more or less to my satisfaction. The rings are not flush with contour like they ought to be - the penalty I paid for the mistake, but everything else worked out OK. Note the insignia behaved OK after flat coat.
Above is the LH lower wing tip, where the ID lights were mistakenly placed on the 3D printed part. Can you see the three round cover plates?
Let's make believe that horrible ID light gaff just didn't actually happen shall we?
The guns shown above are finally permanently in place. Had to wait for painting to be finished. When I started the wing months ago, I thought the guns and their openings would be trouble. Nope, they were easy. Rhino design, 3D printing, and carefully selected tubes of multiple materials.
Above I show perhaps the worst looking feature of the wings - the landing light. The aluminum skinning is dreadful, but it's there for good. No way do I tear it out and do it again. No way.
Two of the aforementioned casualties are the wing tip aft ends. They are so delicate - this from a couple months ago:
You can practically see through the aft end they ar so thin.
Well I failed. I tried to protect them and I failed. Both have about .1 inch or so broken away. I won't show it, it doesn't look that bad. Until I install the ailerons and then it will look bad. So I will have to fix them. I can 3D print the aft portions at a point I will choose later, cut away a matching portion, and CA/epoxy new aft ends on. MUCH easier said than done. I think I will do this once the ailerons are installed.
Ailerons? So I have begun the Rhino work on the ailerons, finally:
They will be designed and constructed similar to the flaps, which worked out well. But as I began working the complex inboard end, easily seen with flaps down, I discovered to my dismay that I mislocated the aileron inboard hinge fitting on the wing rear spar! When will it end???
The hinge fitting is about 0.03 inch too far inboard (full scale that would be about a half inch), which really spoiled the integration of all that stuff on the aileron inboard end. Sooooo, I got out my magic wand and tweaked some details on the aileron here and there in Rhino and got it to look kinda like the real thing - to a point where few if any will notice. Maybe I should not have admitted it.
So as I wait for masks and paint for the fuselage repaint effort, I will be concentrating on the aileron now. I think you will like them once done; lots of work to do to get to that point. I hope to report good progress on them next post. Thanks for looking in.
-
-
This is really fun to watch Tolga. May I ask - what are you using to bond the parts?
- airscale and Tolga ULGUR
-
2
-
-
So many kind and encouraging comments. Thank you all. Still "girding my loins" for try number two. One of the things I am going to do is to divorce myself from my beloved Model Masters Dark Sea Blue FS15042. For years now I have used this blue spray paint for my US insignias, and to my eye the hue is perfect. Not too blue and quite dark. Up until this point I had not experienced the crinkling failure I just experienced on Cripes. It is enamel, and I sprayed a Tamiya lacquer clear over it, which is a no-no. Why now and not before? Don't know.
At any rate, I will be using a different paint for the insignia, probably lacquer-based. Bringing me to this question - what is a good proper-colored paint to use? To date, I have used almost exclusively Tamiya paints, decanting spray cans or using bottles. I don't get many lift-off issues when painting on the aluminum as long as I use the gloss clear as a primer. My one foray into Vallejo acrylics was the blue-noser blue and although I like the color I came up with, I will never do that again. With my clear-coat covered aluminum, it lifts off with the bat of an eye and I have had very many issues with it. I did a web search and found some folks who like Tamiya sea blue XF-17 in a bottle, and add drops of white until satisfied. So I bought a couple of bottles. I don't like it. It's hardly blue at all - more like dark gray. I also got some Tamiya US Navy blue AS-8 in a rattle can. This appears much better - it is "bluer" but not too much. But it is a lighter shade and I am in the process of adding drops of black to see if I can get something closer to the model Master dark sea blue.
All you master painters out there who have painted great WW2 US insignias - what do you use?
- scvrobeson and Greg W
-
2
-
On 2/10/2025 at 2:40 PM, LSP_Kevin said:
A light coat airbrushed on may have been OK, but the volume of paint out of the rattle can would have been too much for the Model Master enamel to cope with.
Yes Kevin I think you are right. The cold weather right now is preventing me from air brushing (I do it in the garage), so I got impatient and used the rattle can indoors. My wing has the enamel on the stars and bars too, so I am a little worried. But it has held up OK in the past (like the Corsair), although I think I air brushed the Corsair clear coat. Hopefully careful air brushing on the wing will work. I do not want to strip that wing.
The fuselage invasion stripes and insignia looked pretty ratty anyway. This is a chance to do better.
- geedubelyer and LSP_Kevin
-
2
-
In parallel with the wing paint work, I am finishing up forward fuselage skinning work - I had the two side panels left; something I have been delaying for a long time. Here are the side panels - the LH side panel is always more interesting than the RH side:
In order to do the side panel skinning, I had to permanently install the windshield, instead of the spare one I have been using. So I could match the panel edges. Although I have not shown it, fit to the engine cowl is excellent. I guess you could call that a milestone. A shoutout to Thunnus who provided the stencils for the crosses, and also the decal.
So once that was done, and some dirtiness applied, I decided that it was time for some semi-gloss clear to preserve it all. And look what I got:
Disastrous. Fellow modelers - I don't know how many more heart stoppages I can endure with this project. And BTW - I broke off the throttle lever again, just for good measure.
All right. I don't think anybody was very happy with the fuselage painting to date, even before this latest catastrophe. Mistakes have been made. And as you may recall I have had some issues with aluminum skins disbonding, including the LH side fuselage, and my CA fix really mucked up the paint. And prior to that I was a bit careless shooting on the white, and got alot of dripping, which was sorta fixed, sorta not. This crinkling of the dark blue on the insignia is the last straw. Now this paint job is just awful. No better way to describe it. That paint is Model Master dark sea blue enamel - a paint I have been using a long time for the US insignia. I don't know why, but the Tamiya semi-gloss out of the spray can really attacked it. So I am going to start over. Already I have stripped the offending area:
I will do some things differently. I have some ideas based on what I have done with the wing painting so far, which has turned out better. I will show wing progress next post I think. Meanwhile I have a heavy heart, and I'm a little nervous. And it is too cold to do airbrush painting right now.
-
8 hours ago, geedubelyer said:
How tough do you think it would be to remove the wingtip metal panels?
Guy - the cure would be worse than the disease! The metal panels have some edges bondo'd to try to eliminate the panel lines, as was done on the actual aircraft. You will find, I think, that my fix is going to be OK.
-
For those of you who, like me, regard this recognition light issue as a project wrecking mistake, and just didn't say it out loud - I have some good news for you.
First, months ago I did the wing tips, and was so proud of them. They really are awesome, especially with the tip fairings attached. They were tailor made for 3D printing. I took pictures and posted:
Those three holes on the tip on the left (the LH tip), with light bulbs at the bottoms of the holes? I worked hard on those details. But they should be on the other tip that you see on the right (the RH tip)! Just a stupid gaff by yours truly. Truly stupid. Hit the button to make opposite hand parts, and it's good. Wish I realized that then; I'd have re-printed them.
But no. The mistake went unnoticed right up until the wing was basically complete and ready for paint. And it was discovered and my hair caught on fire.
So guess what I did nearly all day today. Here is what that LH side tip panel looks like now:
Those pretty light holes are never to be seen again - covered by round litho plates and gaps filled with epoxy. I have sanded and buffed this area about as well as I can. I will restore the silver paint next, and accept it if I can still see the plates. It's part of the price for the mistake.
But what I really want to show you is the RH side where I created the new recognition lights, now in the correct location:
Those litho rings are the same ones I made months ago, meant to fit into .005 inch under-contour circular depressions such that the rings would be flush with the surrounding surface (now occupied by the litho cover plates in the previous picture). So now they are no longer flush with the surface, but they are really quite thin (less than .005 inch thick after some vigourous sanding). That is also part of the price for the mistake. And what you don't see yet, under the masking plates, are three holes with little light bulbs at the bottom sort of similar to what I did in the first place. Later after I finish the painting in this area, I will glue in the colored acetate "glass", and I think I will have an acceptable installation. I will post on it when it's done in a couple days or so.
I think this development is better than just accepting the mistake as it is. When I show the finished product I hope you all agree.
- Model_Monkey, Greg W, TAG and 14 others
-
17
-
14 hours ago, JayW said:
I have the three ID lights on the wrong wing tip
Well after sleeping on this, I think this ID, or "recognition" lights mistake is too serious to ignore. I will not be sawing off the tips or some such thing; I have to be careful that the cure is not worse than the disease. However, the light rings and some colored acetate can be pretty easily bonded to the other tip. And the original side just covered with little .005 thick round plates, and then a bit of gap filler. The plates will be flush with contour so perhaps the fix on that side can be all but invisible. However I don't think I can make a flush installation at the new location like the other side where it was all designed into the part. And I will not have the fancy depressions with light bulb heads, although maybe I can do something clever. But that would be the price to pay - I will not be getting away with this mistake for free. Boy do I wish I discovered this before I applied the silver paint (just hours before I discovered it). Any comments from our master fixers?
-
-
Hello folks - as I was continuing skinning and surface work at the wing tips, I realized that a couple of things were missing in the gear bay which need to be there, and need to be there at this stage, not later. MOF should have been done earlier. Two items - the major wire bundles (one LH and one RH), and the bomb control cables. Both go the full length of the gear bay, and both would have benefited greatly had I created them before gluing on the upper panels.
That's OK, they got done. As did the skinning and surfacing work at the tips.
Here are the (more complete) gear bays before the lower panels get glued on:
The unterminated wire bundles are in evidence, hanging out of the bays. They were made from 14 or so strands of .003 inch diameter wire, each one meticulously threaded through holes in the ribs. Yes it was hard and excruciating work. They will get terminated along with quite a few hydraulic and fuel lines, once the wing and fuselage are joined. And that is on the radar with a strong signal! The newly printed lower skin/stringer panels are in front, waiting for installation. That will cover some of that busyness. Here:
Now that should be a familiar sight for Mustang enthusiasts. A bit more bondo work on the panel lines, and the wing is now ready for masking and paint:
The pictures just do not do a good job of conveying how large and unwieldy this wing is. But so far I have been very careful, and nothing has broken.
Except this:
And this:
Those are (or were) lugs for the landing gear torque links, on the upper struts. On both LH and RH sides, the ouboard lug is broken off, while the inboard lug remains. I discovered this randomly; I don't even know when it happened. But it kinda ruined the moment when I discovered it. A brief and fruitless seach for the broken lugs (each about the size of an ant) was undertaken. So I will make new lugs. I'll fix it at an appropriate time, but the fix just won't be as good. And it's my own fault - I did not protect the lugs well enough and it would have been easy to do. This build has its ups and its downs.
OK - next post you will see the painted wing. I can't wait!
- TankBuster, denders, Model_Monkey and 20 others
-
23
-
Golly Chuck - beautiful engine! Your spit is coming along nicely, and swiftly.
- chuck540z3 and Martinnfb
-
1
-
1
-
-
My sequencing plan has me moving away from the partially completed gear bays and doing outer wing surface work, to prepare the wing for joining to the fuselage, at which point the gear bay work can continue. First task to that end was to take those freshly installed IBLE upper skin panels, and bondo over the panel lines, just as was done on the actual aircraft. But also there is a small removable skin panel right in front of the LG strut, no doubt used to service the strut and the down lock mechanism:
And that is going to be aluminum skinned, and I think will be kept natural metal while the wing itself is painted silver. Don't know why - but I seem to recall that's the was it was. Or, at a minimum, its panel lines and fasteners will not be puttied over. Here is one of them cemented onto the wing:
You can see the upper skin panel lines have been filled in and smoothed. Yahoo!
The other:
Very pleased with those little panels - I designed the nose beam skins and upper skin panels to be .005 inch under contour locally to allow for those panels to be flush on contour. It worked great.
And then, it was on to the wing tips. Boy - how long have they been sitting around....
The wing tips could have been attached at any time, but I just didn't want to deal with such a long wing if I didn't have to. So I delayed. Now though they must be attached if I am to paint the wing before wing/fuselage join. And here I show a wing that is now about 5 1/2 inches longer in span:
I have to be oh so careful not to bump it into things. Big wing for sure.
The joins are not very pretty, as shown here:
3D printing is not as exact as some think. Otherwise those joints would be much smaller. But fear not! Much of the joint is covered by an aluminum skin panel, and the portion that is not is bondo'd and smoothed and later painted silver. Like this:
That aluminum panel came out really nice. I am a happy camper. It was difficult to trim it around those two external stiffening members, but success. One down, three to go. Sure hope my new bottle of Evo-Stik fixes the disbond issues.
So now the challenge is to continue to prepare the wing surfaces for paint without breaking off a wing tip, or a LG strut. Aluminum skinning and bondo sanding are heavy handed tasks and great care must be taken to protect the more fragile parts of the wing.
Later alligators.
- Fanes, Philbucknall, LSP_Kevin and 20 others
-
23
-
Very late comment! Hands down best looking 262 I have ever seen John. Rivals your Corsair which made me a Thunnus fan forever.
-
It was on November 4 when I posted my initial progress on the inboard leading edge (IBLE) and landing gear bays. A sub-project I had been looking forward to (even dreaded) ever since I began this project. That was 2 1/2 months ago, where I began by designing and printing some IBLE test parts to see if they would all fit OK with the rest of the airplane. It was a good test, so full speed ahead. Since then, with the exception of some difficult fuselage painting and aluminum panel repair, it has been all IBLE and gear bay work. So what do I have to show for 2 1/2 months work?
First, I'd describe the phases that I am going through to produce a good IBLE and gear bays.
1. Create structural details - ribs, skin panels, and nose beam mostly. Status - done.
2. Create systems details - actuators, valve bodies, pumps, electrical components, etc. Status - done.
3. Decorate individual structural details with systems parts as much as possible (hydraulic tubing, mechanical system parts, brackets, fuel lines, electrical parts, etc). Status - done.
4. Assemble structural details to wing (except upper panels so as to maximize access). Status - done.
5. Add systems runs - hydraulic tubing, fuel lines, mechanical system push rods, cables, etc as much as possible in absence of upper panels. Status - done
6. Add more systems runs - hydraulic tubing, fuel lines, mechanical system push rods, cables, etc as much as possible with upper panels installed. Also, permanently fix landing gear upper struts in down position to allow completion of some systems runs that end on the gear strut (brake lines, LG position indicator system cables, the LG actuator push rods, etc). Status - done.
These steps are pretty much complete, and I will show you what it looks like:
First though, here is the tool I have had to use for nearly 100% of the items in 5 and 6 above:
That and high magnification goggles over reading glasses.
The picture above signifies the end of phase 5 above, where the upper skin panels are still left off to allow max access. And the gear struts have not yet been fixed in the down position. Recall that I have had them usually rotated up to stay out of harms way. Both were GREAT ideas. But now the struts and skin panels can wait no longer - here is phase 6:
From the outside:
Upper panels are now permanently fixed in place, as are the LG upper struts. The upper struts are very robust I am pleased to say. They are going to get bumped, so they need to be.
Let's zoom in a little into the gear bays. LH side:
Alot there - I will not bore you with a description of all of it. Of special note though are the now completed fuels lines emanating from the silver fuel selector valve. A giant wrestling match and big victory. Peter will be able to relate I am sure, as he had to do same on his Lope's Hope. Also dig the cable and brown (phenolic) pulley wheel hanging above the cutout in the skin panel. That is part of the ridiculously complicated landing gear position indication system. The cable is 0.008 inch diameter fishing line, and snakes its way through pulley brackets and rib penetration holes all the way back to the upper LG strut.
RH side:
Alot there too, and there will be more later. Look at the relatively thick and wiggly fuel line that passes through the ribs. That was one of the toughest tasks to do - part breakage was a big risk, as the tube (1.0 mm solder) is stiff relative to the thin 3D printed ribs. There is one on the LH side too - they are for the droppable tanks on the wing pylons, and make their way to the aforementioned fuel selector valve on the other side of the centerline rib. My advise to others attempting to do similar work - patience. And walk away when you start to get flustered. Take a deep breath..... You will also see the other side of the LG position indication system run with its fishing line cable - kinda proud of that. And another item requiring patience and the ability to walk away when the going gets tough.
Here - I especially like how the brake lines worked out:
Those couplings on the wing and on the strut were designed and printed off by yours truly, and designed to accept the .015 inch solder on one end and the .04 inch wiring insulation on the other. Or, in full size, .25 inch tube and .75 inch high pressure hose. They worked pretty darn well.
Well that is my 2 1/2 months worth of work so far. This all was some of the most difficult and exasperating work I have done to date on this model. Heart pounding too - risk of breakage of parts that I really do not want to break was always there. Thankfully, nothing broke. It should also be said that the lower skin panel, once created and installed, will hide some of this stuff, but not that much.
Here is final phase I will go through to finish this part of the build up:
7. Attach wing to fuselage, and finish all remaining systems runs where the longerons and firewall need to be present. Status - not started.
That item 7 is a big ask, and to start it, all kinds of pretty big things have to first happen - bondo and smooth upper skin panel to the rest of the wing upper surface, add the wing tips, add the four remaining (and large) aluminum skins, bondo some more, and paint most (but not all) the wing silver as described in previous posts on P-51 wing painting. Oh, and skinning the forward fuselage.
So no more gear bay work for a bit while I do all those big pre-requisite tasks. Which I will report on next post. Stay tuned!
- SwissFighters, Philbucknall, Paulpk and 32 others
-
34
-
1
-
Great first try on molding John. Boy does this bring back some memories. I bought the same alumilite kit you have when I was in the middle of my big Thunderbolt build quite a few years ago now. I attempted to mold cylinder heads for the R-2800, without success. And I molded a fourth prop blade from a master, successfully. I found, BTW, that I had to increase cure times over the recommended, and this resolved the sticky rubbery issue.
-
1 hour ago, geedubelyer said:
So Jay, what are the possible solutions?
I imagine the easiest is keeping the model at a roughly stable temperature?
Beyond that are there any other steps you can think of to lessen the risk of your panels pulling off?
Guy - Peter tells me he is not experiencing the same thing, and he has alot of skinned models. I doubt any of us want to add climate control to our modeling area other than just locating the area indoors. And even then, most of us probably keep our abodes at a different temperature during the night versus the day. Peter suspects I didn't bond some of those panels very well. I have a can of Evo-Stik where I decant some of it into a smaller bottle, and then thin it down from there. With time it tends to thicken, so I continue to add thinner. Peter does the same thing. It could very well be that it is time to get rid of what I have in the bottle (been there for months if not more), and start anew with some fresh Evo-stik from the can. My older Corsair, which recall is almost fully skinned, is not having these issues nearly as much. Although one wing panel did disbond a bit a while back.
47 minutes ago, checksix said:I wonder if spacing the panels slightly (similar to expansion joints in sidewalks, driveways, and bridges), would reduce the expansion/contraction stresses for large models such as this where the effects of each panel add to those of its neighbors.
That would not be that hard to do. The panel edges get final trimmed at installation time anyway. It's a thought. Thanks for that.
-
2 hours ago, checksix said:
With regard to panel pop-offs, my guess would be differential expansion between metal sheeting and resin parts.
A few of you have thermal expansion on top of the list for potential cause of these disbonds. Geedubelyer even suggests printing off a square and measuring the width at low and high temperature. Well, according to several sources on the web, the coefficient of thermal expansion (or CTE) for 3D print (or photopolymeric) resin is between 70 and 100 micrometers/meter/deg C. And the CTE for aluminum is 21 - 24 mm/m/deg C. So, that says the resin will grow or shrink with temperature change at roughly 3 times the rate of aluminum. I was surprised. And incidentally, polystyrene plastic has about the same CTE as the resin. Further, if a drop in temperature in my hobby office occurs, relative to the temperature at which the parts were bonded together in the first place, that means the resin will shrink more than the aluminum. And the more the difference in temperature, the more the mismatch in shrinkage. At some point then, the aluminum/resin combination would overcome the strength of the bond, and want to buckle and break the bond. Makes sense. No doubt some of my panels are glued down better than others. And that could be why some are disbonding and some are not.
2 hours ago, checksix said:Is it possible that the resin parts shrink slightly over time if they aren't completely cured initially?
I believe the opposite is the case. Post curing of parts appears to grow them, not shrink them. Frequently I have parts that have pins or posts going into holes on other parts. And where I show clerance between pin and hole on the digital model, I can get interference fits on the actual parts. The holes shrink (because the material around them expands), and the pins expand. At any rate, the areas where I have been having disbonds involve 3D printed parts that have been around a while and ought to be pretty stable by now.
1 hour ago, Mike_Robinson said:Jay I read all the way through but maybe I missed it, what type of adhesive did you use to bond the aluminum?
Mike - previous to this build was an F4U Corsair I did in 1/18 scale, where I skinned nearly the entire model with aluminum prior to it getting its tri-color paint scheme. That project was my first skinning effort and was where lots of experimentation happened with adhesives. I ended up using the same product Peter Castle (Airscale) uses for his skinning efforts - Evo-Stik. It is a contact cement made in the UK. It is good stuff but perhaps not too different from any contact cement that can be found in hardware stores. But some seem work better than others in this application. Dilution was also a big deal, as most if not all contact cements are a bit too thick for this application. I ended up using a xylene paint thinner that seems compatible.
-
51 minutes ago, Landrotten Highlander said:
can the CA glue be removed from he apint with CA remover without damaging the paint?
Hey LH - thanks for that! Turns out that most of that stain was indeed CA residue where I thought it was dissolved paint. So I applied some steel wool to it and a good bit of the stain buffed out. That left some touch up here and there for all three colors. And now I have this:
I am going to declare "weathering" on this little crisis, or better a crisis averted. I have not even weathered this part of the fuselage at all yet, so I would like to say this is just a head start. A final coat of flat clear and this is going to be well within my definition of acceptability.
Ever stalwart.
- Shoggz, Serkan Sen, BiggTim and 14 others
-
17
-
Hasegawa 1/32 Bf109K-4 Yellow 1
in Works in Progress
Posted
You can say that again. John - what is your technique for avoiding or minimizing paint leakage into panel lines?