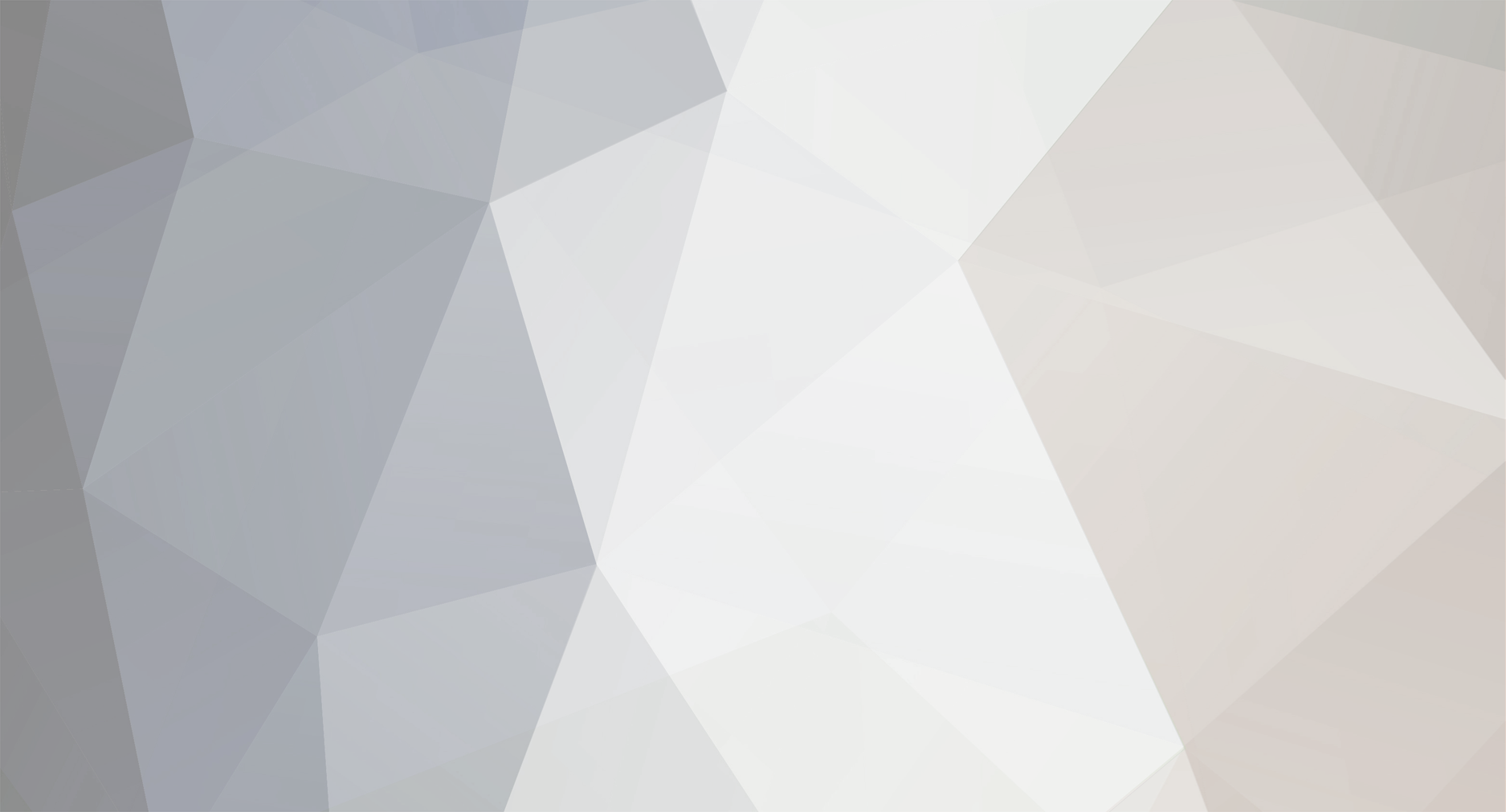
JayW
LSP_Members-
Posts
2,321 -
Joined
-
Last visited
-
Days Won
27
Content Type
Profiles
Forums
Events
Everything posted by JayW
-
Here is the RFI post:
-
Hello folks. I would like to present to you my 2-year long project "Cripes a' Mighty" P-51B-10NA Mustang, flown by Major George Preddy of the 352nd FG ("Blue-Nosers"). Scale is 1/18 - she is a big girl for sure. She is about 99% 3D printed using an Elegoo Saturn 2 printer. All components were designed in Rhino 7, using original NAA engineering drawings obtained from Aircorps Library. The build thread can be found here: Here she is: Before I present more pictures, let me offer some comments on the build. First, the reason I picked this subject (a P-51B) was mostly two-fold. One, I really wanted to do a Malcolm hooded, natural metal finished -B model. And two, the P-51 is just about completely defined by micro-filmed engineering drawings available from Aircorps Library. That, along with learning Rhino 7, and purchasing a good 3D printer, allowed me to produce a model with near perfect dimensional accuracy. That applies not only to the fuselage, wing, and tail, but also every detail I chose to include. No guesswork. No errors. As for the selection of "Cripes A' Mighty" - well that was mostly from a vote by many of those who were following the build, and my concurrence. This was my first effort at creating a model totally by 3D printing, and what a learning process it was. 3D print resin is amazing stuff, but it is fragile. I cannot count how many times I broke a part and either had to repair it or print a new one. But when done properly, what results is detail that often cannot be obtained from plastic, or scratch building. As a result Cripes is by far the most realistic model I have ever built. She is the most fragile model I have ever built as well. Also, this is my second effort with aluminum skinning using .005 inch thick aluminum sheet. Not easy to do, but this process results in very real-looking natural metal finish. I learned this technique from Peter Castle - we know him as Airscale. He has been doing it for years. This project was a mix of elation and pride - why we build models - and panic/anger/fear/frustration. Cripes was no easy build. And big mistakes were made (all were ultimately fixed). How about mislocating the flare gun hole one full bay and royally screwing up the left-hand cockpit sidewall. Or putting the three colored ID lights on the wrong wing. Or screwing up the main landing gear rake angle by a couple of degree. Or a huge one - tipping it over late in the build and breaking off the centerline gear doors and the left hand landing gear strut. OMG that was awful. There were painting disasters, disbond issues, fractured parts too numerous to count. But there were also moments of huge victory and accomplishment and pride. I think perhaps the most interesting and successful element of this build was the use of a 3D printed highly accurate fuselage assembly jig. Here is a picture of it: With some fuselage parts loaded onto it: I show this because this jig provided the foundation for the entire build - an accurate forward fuselage with cockpit, and accurate attach points for the wing, engine cowling, and aft fuselage. Had to have that before everything else. Another interesting element of this build was my decision to use 3D printed transparencies. As opposed to vacuform. Injection molded parts were of course not an option. Ultimately most (but not all) the canopy and windshield and aft window parts were provided by Shapeways at high prices, after I just flat failed on many of those parts. The concern of course was clarity. Most of the followers of the build were very skeptical of 3D printed clear resin to deliver. I will let you judge for yourselves. The area where I had to do some serious guesswork was the Malcolm hood and the cockpit modifications for same. Dozens of pictures both period and from restos helped immensely. During that time of the build, I learned a whole lot about the Malcolm hood modification, and how involved it actually was. Some of you may not be aware that the Malcolm hood was a field modification entirely. A -B or -C (or even an -A) model would go into the field hangar, and several days and hundreds of man-hours later, it emerged with a big fishbowl sliding hood replacing the greenhouse style canopy found on production aircraft. The mod was a big deal - major surgery for the cockpit. Pilots absolutely loved it, as seeing was everything (along with speed and fire power). Visibility with the Malcolm hood was superb. At any rate, the hood was driven by a crank handle and chain drive. I am not aware of any modeler other than myself attempting to model the various cockpit modifications for the hood. Look for that in the pictures. This model is heavy - about 2.5 pounds or so. So the landing gear struts needed help, especially the tail gear. This was the first time I re-inforced landing gear struts with metallic rod (brass or music wire steel). Here is a picture of the tail gear strut and an internal stiffening rod formed on a 3D printed forming block of my own design: The main gear struts were re-inforced similarly. The re-inforcements have worked. To my horror, after the main gear were installed onto the airplane, I discovered the rake angle was off by a noticeable couple of degrees. That after being so careful to design it right. I still don't know what happened. So I created a fixture where pressure could be applied over days to the gear struts via shims with ever-increasing thicknesses, to force the struts back to a correct rake angle: See the white shims? I show this because it was some of the most stressful days of the build - hoping to get some permanent deformation on very stout gear support parts without breaking something important. Believe it or not - it worked! Lastly some details to look for in the pictures: - Mismatched tires (you see alot of that in period pictures) - 3D printed chains nested in the upper longerons which drive the Malcolm hood - 3D printed clear transparencies - External rails and rollers for the Malcolm hood - Spitfire-style exteral rear view mirror - Malcolm hood that can actually be slid fore/aft - Movable tail surfaces - Head rest pad and seat back pad (thank Antonio Argudo for that!!) - The crazy shaped bomb racks Here we go: I guess that is enough. I would like to thank first of all the 40 or so followers of my build thread. All were very patient and supportive during the 2-year effort. And special thanks to Airscale for giving me the extensive decal set for his 1/18 P-51C Lopes Hope, hundreds of pictures, and a few helpful Rhino files. Oh, and the 1/18 scale seat belt hardware. Also Antonio Argudo for designing some really great models for me - the head rest, seat back cushion, and tail gear bay canvas cover. Also Thunnus who provided me with nose art decals and stencils, and stencils for other things like squadron buzz letters, tail serial numbers, national insignias, and kill markings. Also TAG and Antonio for priceless period pictures of anything and everything P-51B. And lastly Aircorp Library - OMG. Their collection of engineering drawings and other documents is absolutely priceless. I hope you like Cripes a' Mighty. She is not perfect, and she appears rode hard and put up wet. But it is the best I can muster! Thank you.
-
Well heck y'all. Or bloody hell in old English. The LH 75 gallon tank actually can be inserted into the hooks of the bomb shackles and stay in place as designed (the RH tank not so much). Here it is in all its glory: To my eye, that looks pretty darn cool. And, adding the fuel supply and pressure lines would add to the look. As well as the decals that are not there yet. What is lost is the unobstructed view of the landing gear and gear door, in a side view at least. What I think I cannot do is have this tank removable. For the reasons I already went through - the model is too fragile to subject it to alot of handling. So, I think this P-51 is either going to be with drop tanks, or without. I am on the fence. I would love to see some opinions from those who have been following this.
-
Can anyone provide some pictures?
-
The last project on Cripes a Mighty would be the bomb racks. These (the real thing, on Lope's Hope): Surprisingly, effective on -B/C models, the bomb rack is made of some kind of internal re-inforced molded plastic. Earlier versions were magnesium (on -A models, A-36, etc - I think). The two configurations vary a bit but not much. Anyway, the drawing says the rack is to be gray, to match the underside of the wing with the standard gray and OD paint job that these aircraft were delivered with, up until they began to arrive with un-painted aluminum. As discussed already, -D models introduced an entirely different rack. Also previously discussed was sway brace bolts, and whether or not they included the large round pads. Mine would have the round pads: I designed the holes in the pads to have a lip at the opening with a tiny bit of interference fit for the bolt ends. And the bolt ends had a bit of a bulge at their ends to snap into place in these holes. The bolts: See the bulged ends? Put together (carefully) and I got this: Snap! Yes they actually swivel. I was amazed - true micro-engineering. There they are next to my 3D printed and gray painted bomb rack. For the umpteenth time, I thank Airscale for the decals. My intent here was to be able to mount 75 gallon tanks and have the pads swivel into place with little to no gap betwen pad and tank. It worked, but read on. A finished bomb rack with sway brace bolts: And here are the 3D printed tanks: I had to do some educated guess work as to the shape and size of the tanks. Both my racks and my tanks are designed at the attach points for removal and re-attach. It works somewhat but not great. In real life the tanks were identical, but I have a LH and a RH tank. That is because the little fittings where fuel lines connect are oriented differently LH to RH. These tanks are not ready for prime time, and will receive decals one day. But for now, I have decided NOT to use them. I never intended drop tanks to be installed permanently on Cripes - they hide too much of the landing gear and I do not want them hidden. They would instead be removable. But I have found that what I have here is an amazingly large, unwieldy, and fragile P-51 model. Every corner of it has something that breaks off all too easily. And installing or removing those tanks, along with their plumbing, would be a labor intensive and delicate task, subjecting Cripes to part breakage every time I mess with it. MOF - turning the model upside down to install the racks resulted in this: The external rear-view mirror broke off, after being on the aircraft for what - a week? Well, that was merely an opportunity to tweak the mirror design a bit - a touch shorter, with slightly wider base pads - print it up with some spares, and re-bond it to the windshield. No prob. But - the wing tips are uber-fragile, and the fix is much much more complicated. Here one is, BTW, finally freed from its protective padding and tape: Just look at how delicate that tip is. It just had to be a frequent maintenance item during the war. I am proud of it and I do not intend for it ever to be subjected to potential for breakage. Other parts are very fragile. The pitot mast for example, that part very close to the bomb rack. The gear doors - they cannot be bumped or the links will break. That would break my heart. The movable tail feathers - also fragile. So I will keep the tanks around, but I will not install them at this time, perhaps never. Here is Cripes with its newly installed bomb racks: Pan back and you see here the final WIP picture of Cripes, with her racks and new mirror, before I put together the RFI post: Oh one more thing - Antonio made up a model of pilot George Preddy,and gave me the file. After some back and forth about George's height (he was a fairly small person I understand), I scaled him to be about 5 foot 6 inch and printed him up. And here he is: Dam Antonio - you are one talented dude. I will paint him one day, but not today. OK RFI post upcoming. Thank you all so much for sticking with me on this 2-year adventure. So appreciated.
-
Wow - it's been a minute Guy. That wing, when you pan back a bit, looks like a real wing. It's just spectacular. You have a gigantic project going here, glad to see you are back in business!
- 1,592 replies
-
- scratchbuild
- rivets
-
(and 4 more)
Tagged with:
-
1/24 Spitfire Mk IXc, Kicked Up A Notch, July 6/25. On hold for now.
JayW replied to chuck540z3's topic in Works in Progress
Here in western TN, USA, I have the opposite going on. In the heat of the day, everyone who is sane, or who doesn't have to, stays indoors. So I get some of my best modeling time during the summer. 😁 -
So y'all didn't think I was finished did you? The bomb racks and the 75 gallon tanks have been occupying me lately. I realized fairly quickly that if I am to make removable 75 gallon tanks a reality, then I have to integrate the design of both. So I have begun the design of the bomb racks from scratch - a Rhino adventure extraordinaire, what with the teardrop shaped sway brace cross-sections and ends, and their faired connection to the rack housing. And also the tanks from scratch - easier. Some guesswork on the tanks; no guesswork on the racks. Here is what I have so far: Parts will be printed up in the next few days I think. Will report out soon as I can. Then it will be RFI.
-
Similar questions - where do you put these dioramas? Including this one which is stunning!
-
Gosh Peter - I agree with these other folks. The model itself is so convincing, but with the base, it looks very fast! I have a new-found interest in the scooter.
-
Well Kevin I am glad you like it; I am not as impressed. First of all, nearly all the model is skinned in aluminum. That alone will give you a realistic metallic finish. But for me, it is too new looking. Fine for a factory fresh subject. But my subject, Cripes a' Mighty P-51B, is far from factory fresh. It has seen a tough 1944 winter, a muddy spring, and some serious battle time. So I wanted the finish more flat and dirty. First though, in order for the metal to be painted without alot of lift-off, I sprayed the metallic surface with Tamiya clear X-22, thinned about 50% with lacquer. Got that trick from Chuck540z3, and it works as well or better than any self-etching primer I have found. Then any paint needed. Then I got it dirty and messy with Tamiya weatherine pastes and/or Flory wash. Then seal it with Tamiya TS-80 flat clear either air-sprayed or straight from the rattle can. I could have used sem-gloss instead and maybe gotten a better result. Don't know. Then, weeks and weeks of handling it, wearing some of it off. Add it all up and it looks pretty weathered. Not much science there, and some of LSP's finish masters could do much better. Thank you though! Ah yes. But the -B/C models all got the one I am going to use. The more streamlined one you speak of is used on the -D/K. You know OBG you are probably correct. A bombing mission interspersed with escort missions might necessitate changing out the padded bolts with the smaller versions. Not a difficult task for the ordnance guys. I am not sure at all if the padded versions would work well with the bombs. I think I am going to do some guess-work and make the padded versions. And I probably will not make the tanks. They tend to hide the MLG in a side view, and I am very proud of my MLG and doors. Instead this kite will have returned from a mission where the tanks were jettisoned. That might mean a raw tube hanging out of the wing. I'll research that.
-
Another thing - Peter, in the absense of engineering drawings, how are you coming up with all this fantastic detail? I have seen you do this on a number of your projects, where technical data is not there. I know that alot of pictures and diagrams can be had, short of acctual drawings, but how much guesswork are you resorting to? And I guess the same can be asked of the basic shape. Are there enough diagrams of the Tiffie's fuselage and wing cross sections that you can use with some confidence? Inquiring minds want to know.... 🤔
-
Well I have a few things - There are a couple of reason for 3D printing model aircraft. One, an IM kit might not exist, or if it does it might be inadequite. And two, IM may not get you the detail you are looking for. IM today is far better than IM yesteryear, but still there are limitations due to the rules Peter is getting familiar with. That is why there have been aftermarket kits out there for cockpits, wheel wells, etc. To model what cannot be modelled with IM. So what I would look for is to IM big parts in such a way as to not compromise the detail we want. Hopefully that is possible. And then 3D print the detail rich areas wher IM will surely fail us. As for part count - some good reasons for separate parts as opposed to integral one-piece parts might include detail painting. Another might be part detail. Even 3DP has its limitations when combining parts, which can be overcome by separating out parts. Lastly, some of us like the idea of building complicated multi-part kits. Pre-assembling in the form of one-piece parts that could be multi-piece parts can kinda take some of the fun out of it. So it is a balancing act. I would say design us a Tiffie that is super-accurate and super-detailed but offers some challenges for the modeler. Building is the fun of it after all. Drive on Peter - this is most exciting.
-
Something curious has come up WRT the bomb rack sway braces. Here is a picture from the installation drawing 97-63001, which shows the threaded sway brace bolts: The bolts are merely 4 1/2 inch long fully threaded bolts with a spherical head on them, 3/8 inch diameter. They look perfectly suitable for carrying bombs, which have hard thick casings. And these bomb racks were designed for bombs, not drop tanks. Even though we all know that as the war progressed, they were used primarily for drop tanks for long escort missions. Now look at this picture of Lope's Hope: Note the more familiar (at least to me) large diameter swiveling pads instead of the small diameter spherical bolt heads. More suitable, it seems to me, for the combat drop tanks which no doubt had thinner walls that might not do well with the small diameter spherical bolt heads. I cannot find anything in the P-51 drawing system that defines these sway brace bolts with the large pads. However I am all but certain they replaced the spherical bolt head type at some point. Can anyone help?
-
Last evening and today is when I got to enjoy the fruits of my two-year labor. Buckle up - I have many pictures to show. First, before I proceeded to fuselage join, there was the exterior rear-view mirror, and the pitot mast. These items were easy to Rhino design, and printing was straight forward. Take a look: I am pleased with the mirror, and it is not as wimpy as the mirrors I made for Miss Velma quite a while back. Never-the-less it is just one more item that begs to be broken off. This model is just "festooned" with fragile parts that are easily broken off. Handling it presents the constant risk of breaking something. It's nerve-racking. When done, I will display it and leave it alone! BTW, you are going to see in all these pictures that the Malcolm hood is in various positions. I do that just to show off. I am so proud that the hood can move, I just have to show that it can. 🥰 And speaking of fragile parts that beg to be broken off - the pitot mast: 3D printed of course. The early P-51's had a long mast like you see here. The -D has a much shorter mast. Why? And then - I just flat ran out of things to do before fuselage join. So fuselage join: What a huge Mustang! Look how it dominates my messy modeling table. It bumps up against everything - my foam wing tip protectors were vital! My heart was racing. I was careful as a heart surgeon doing this join, and my 3D printed round support tool was helpful maintaining a (fairly stable at best) upright stance. It was just such a position where the landing gear post breakage catastrophe occurred a month or so ago. Perilous moments for sure, but no problem this time. Once joined, I could bond on the main gear wheels/tires with flats properly oriented. And then it was on to the MLG strut fairings, or strut gear doors, which I have been patiently waiting for for a very long time. They are part of the signature look of the P-51. This is what I wanted: My Rhino MLG door layout, with deadly accurate kinematic geometry, taken directly from the engineering drawings. Needed to assure the gear doors are hanging as they should. Here are the parts (for the LH side), which have been waiting a long time: Installation of the RH door was straight forward, although very delicate work. But the LH door - I had long ago broken off one of the clevis lugs inside the wing which position the top of the door. So I had to jury-rig a couple of crude locator tools to help. And here are the results: The above picture includes the uber-scary repair of the LH gear strut, broken off last month in the most calamitous mistake of the entire build - a build that had plenty of calamities. I can make out the repair, but I hope nobody else can. I am happy with the gear strut fairings. And for new-comers, this Mustang has mismatched tires. On purpose. Also - that last picture shows the results of the big rake angle adventure, which took up lots of oxygen in this thread, and was a many-days-long hand-wringing affair. I think we have a correct rake angle here; let's hope it stays that way.... Once those doors were installed, this model was 99% complete. Lacking only these: Those bomb racks are from Model Monkey - I ordered them along with the rudder pedals and WM seat quite a while back. These racks are beautiful, and appear quite dimensionally accurate - I think I am going to use them, and you will see them installed next post. I am undecided whether or not to make 75 gallon tanks for this kite. But for now - let me flood the zone shamelessly with Cripes a' Mighty pictures: That, ladies and gentlemen, is a 3D printed 1/18 scale P-51B - a two-year effort. She is not perfect by any means, but by god she is dimensionally correct in all respects. Hope you like what you see. Next post will be about the bomb racks, and then I think it will be time for an RFI. Thanks all of you for supporting my effort on Cripes A Mighty.
-
Happy Birthday Pete!
-
Man - alot of banter about the next project. But first things first! Let me show you the tail gear doors. The tough part to Rhino model was the door insides, which are lumpy. The rest - easier. Here is the basically finished Rhino model: Note I incorporated the piano hinges into the doors. Which better assures they are open at the proper angle. And with surrounding structure: Sometimes I think I have as much fun in Rhino as actually making the model. Here are the 3D printed parts for the doors. You can see I have already skinned the door details: What you see there are the two quite dirty doors, two tee-section link attachment brackets, and two turn-barrel links. The links are desperately thin and fragile. And installed: I did NOT break the links. A victory. With the wheel and post: Antonio - if you are watching, I REALLY like my boot. It is the cat's meow. SH. So now, I am looking around for things to do before the fuselage join. Things better done while the airplane is locked secure in the main strut rake angle correction fixture, or MSRACF for short. Remember? This: Very shortly that very useful fixture will go to the bone yard. It has served its purpose. So first up was to replace the old unpolished malcolm hood (used just as a paint mask and a protector) with the nice polished one, which has been sitting around forever. Repeat forever: Look better? Also, now was the time to install that whip antenna and its bracket: Do any of you remember when I designed that bracket. It was over a year ago. Finally, it has found its home. Yay!! BTW - the antenna is .011 inch diameter fishing line. I guessed at its size. Coming later today or tomorrow are these two parts, currently existing only in Rhino: Yes - the exterior mirror. I designed it purely from pictures provided by followers of this build. It's great to be an LSP'er. I hope y'all will like it. And: The pitot mast of course. Soon as those last two parts are printed off and finished and installed, then take a wild guess what comes next. Stay tuned - a really momentous post is coming very soon.
-
Grumman - wonder why you prefer that..... Actually, the F6F is a possibility. If it came down to the F4F or the F6F, I think I'd do the F6F. Whatever I do, the subject must be supported by the engineering drawings. A full set preferably. Aircorp Library has alot of F6F drawings - perhaps all of them. They also have FM-2 drawings but it looks only partial and many are very poor print quality. The P-38, P-39, P-40, P-47 and P-51 all appear to have drawings, some are full sets. I think that is about it for single engine fighters on Aircorp Library. Oh - and the F4U has a full set.
-
Pete - I swear, if I had access to the nose art on his a/c, that is exactly what I would do. I have tried in vain to get pictures (if they exist), but my first cousins, all three - his kids, who would have those pics, seem to be nowhere to be found. I am afraid we were not close over the years, and have lost contact entirely. I am noodling another project. Being a home grown American guy, I was thinking about replacing my P-47 which began life as a 21st Century Toys model. Would make a fabulous 3D print project.
-
So the rudder was next on the list. Here is a picture of the rudder for Lope's Hope: It is one of hundreds of pictures Peter Castle sent me long ago to help me with my own P-51 build. I put up this picture partly because it shows a couple of pretty sexy features of the P-51 rudder that I worked hard to accurately reproduce - the tab control rod fairing and the upper balance weight housing. Particularly the tab control rod fairing. I was puzzled how to represent this well, and it occurred to me that I can 3D print another form block to form some annealed aluminum sheet - a luxury I have used multiple times now. Here is the little form block: Very easy to Rhino model and print. And with a nearly finished fairing (.005 inch annealed alum sheet): And positioned on the rudder body: I must say - I was pretty jacked with that result. That is one hard detail to reproduce well. The rudder 3D print dump (minus the form block), after a half day of printing at the .03 mm setting for greater detail: Rudder body (with tab rod fairing), upper tip fairing, bottom fairing, balance weight housing, and tab are shown. The rudder body, with its dozens of pinked edges, is a huge Rhino file that takes several seconds to save, and I saved often. Here is the semi-finished end item on the saw horses: The tip and bottom fairings are dry fit in those shots. They go on permanently after the rudder is installed with its hinge pins. Like this: And this: This model has a rotatable rudder FWIW. So it was time to install the elevators as well, which have been sitting around now for a couple of weeks. The elevators have a through- shaft that runs through the fuselage and connects the two such that both rotate together. That plus .025 inch diameter hinge pins on the ends, and I now have rotatable elevators to go along with the rudder (FWIW): That last shot shows all the control surfaces in other-than-neutral position. I kind of lucked out and found some LED light clear rod 1 mm diameter on the web - which scales pretty good for the tip light: File/sand a rounded end, cut to size, spray with clear coat, and voila: Kinda jacked about that too. So the tail feathers are complete. All that remains before I attach to the rest of the model are the tail gear doors. You will see that next post in a few days. Stay tuned - exciting times as we near the finish.
-
Yes I do see that. The challenge of course for producing a mirror and support bracket is the gage. The bracket looks to have a gage of roughly .10 or .12 inch. Divide by 18 and you get 5 or 6 thousandths of an inch - too thin to have any kind of strength at all. And too thin to effectively 3D print. My previous 1/18 P-51 (Miss Velma) had three external mirrors similar to the above, and I used .010 plastic strip for the support bracket - about twice the gage if you do the arithmetic. And the brackets were ridiculously fragile and flexy. So my mirror is going to have a quite exaggerated gage.
-
Dennis, Guy - heartfelt thanks. I will not be guessing anymore on that mirror! Stay tuned for that delicate little project in the coming weeks. And the purpose of this post - a sneak preview of the rudder as defined in Rhino 7: I am super pumped about the rudder. Separate upper and lower fairings so that I can install hinge pins - I want this rudder to be able to swing about. And OBG will like all the pinked fabric edges. Printed parts are around the corner - just a few details to add. So stay tuned!
-
And Bravo to you sir. Take care.
-
This picture: Big thank-you Guy! Yes - that kind. The P-51B has more separation between the two windshield frames than the Spit, but I suspect the mirror mounts the same, only with a wider base. Would love to see an equivalent pic of the P-51B. Let's see if some more pics come up.
-
Can anybody out there provide any pictures or other sources regarding how the Spitfire-style exterior mirror that Cripes has (along with very many other P-51's) is attached to the windshield? Within the next few weeks that item is going to be done, and that is just about the only question mark I have left.