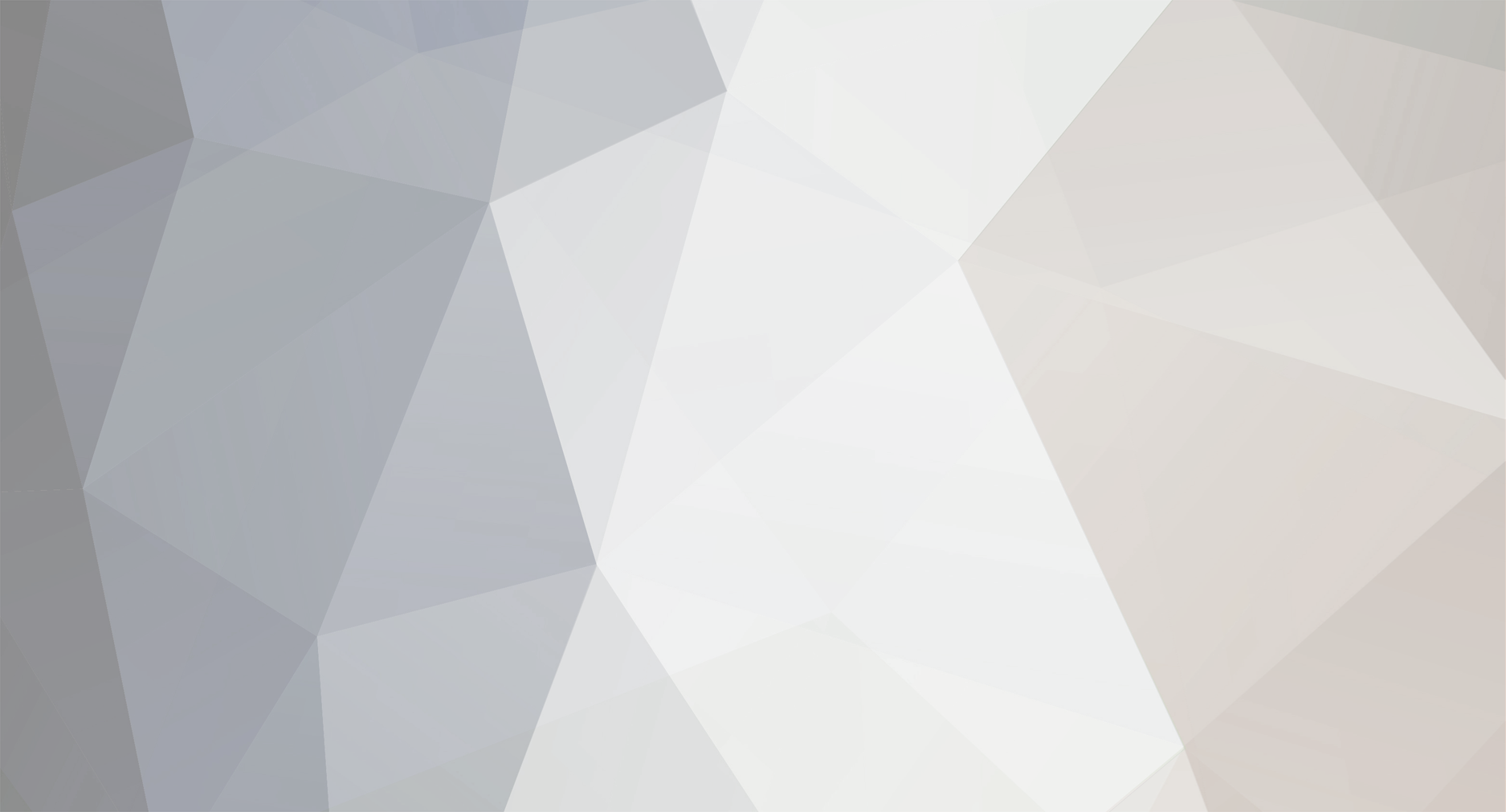
JayW
LSP_Members-
Posts
2,322 -
Joined
-
Last visited
-
Days Won
27
JayW last won the day on July 15
JayW had the most liked content!
About JayW
- Birthday 06/05/1951
Profile Information
-
Gender
Male
Recent Profile Visitors
15,364 profile views
-
MikeMaben reacted to a post in a topic: P-51B "Cripes a' Mighty" 3D Printed in 1/18 Scale
-
Merad reacted to a post in a topic: P-51B "Cripes a' Mighty" 3D Printed in 1/18 Scale
-
JayW reacted to a post in a topic: …And Kill MiGs - Tamiya F-4B conversion (16 Jul: aft cockpit)
-
Anthony in NZ reacted to a post in a topic: 1/18 Scale P-51B 3D Print Build
-
JayW reacted to a post in a topic: 1/18 Scale P-51B 3D Print Build
-
JayW reacted to a post in a topic: 1/18 Scale P-51B 3D Print Build
-
I might mount those tanks one day Anthony. Not now though. When I finished Miss Velma (P-51D) years ago, some months later I made and mounted 108 gallon "paper"tanks on her, plus the plumbing. Just because I wanted to. Who knows - I may do same for Cripes with the 75 gallon tanks.
-
Modelboy reacted to a post in a topic: P-51B "Cripes a' Mighty" 3D Printed in 1/18 Scale
-
KUROK reacted to a post in a topic: P-51B "Cripes a' Mighty" 3D Printed in 1/18 Scale
-
Rocat reacted to a post in a topic: P-51B "Cripes a' Mighty" 3D Printed in 1/18 Scale
-
patricksparks reacted to a post in a topic: P-51B "Cripes a' Mighty" 3D Printed in 1/18 Scale
-
RBrown reacted to a post in a topic: P-51B "Cripes a' Mighty" 3D Printed in 1/18 Scale
-
Philbucknall reacted to a post in a topic: P-51B "Cripes a' Mighty" 3D Printed in 1/18 Scale
-
PROPELLER reacted to a post in a topic: P-51B "Cripes a' Mighty" 3D Printed in 1/18 Scale
-
Here is the RFI post:
-
Hello folks. I would like to present to you my 2-year long project "Cripes a' Mighty" P-51B-10NA Mustang, flown by Major George Preddy of the 352nd FG ("Blue-Nosers"). Scale is 1/18 - she is a big girl for sure. She is about 99% 3D printed using an Elegoo Saturn 2 printer. All components were designed in Rhino 7, using original NAA engineering drawings obtained from Aircorps Library. The build thread can be found here: Here she is: Before I present more pictures, let me offer some comments on the build. First, the reason I picked this subject (a P-51B) was mostly two-fold. One, I really wanted to do a Malcolm hooded, natural metal finished -B model. And two, the P-51 is just about completely defined by micro-filmed engineering drawings available from Aircorps Library. That, along with learning Rhino 7, and purchasing a good 3D printer, allowed me to produce a model with near perfect dimensional accuracy. That applies not only to the fuselage, wing, and tail, but also every detail I chose to include. No guesswork. No errors. As for the selection of "Cripes A' Mighty" - well that was mostly from a vote by many of those who were following the build, and my concurrence. This was my first effort at creating a model totally by 3D printing, and what a learning process it was. 3D print resin is amazing stuff, but it is fragile. I cannot count how many times I broke a part and either had to repair it or print a new one. But when done properly, what results is detail that often cannot be obtained from plastic, or scratch building. As a result Cripes is by far the most realistic model I have ever built. She is the most fragile model I have ever built as well. Also, this is my second effort with aluminum skinning using .005 inch thick aluminum sheet. Not easy to do, but this process results in very real-looking natural metal finish. I learned this technique from Peter Castle - we know him as Airscale. He has been doing it for years. This project was a mix of elation and pride - why we build models - and panic/anger/fear/frustration. Cripes was no easy build. And big mistakes were made (all were ultimately fixed). How about mislocating the flare gun hole one full bay and royally screwing up the left-hand cockpit sidewall. Or putting the three colored ID lights on the wrong wing. Or screwing up the main landing gear rake angle by a couple of degrees. Or a huge one - tipping it over late in the build and breaking off the centerline gear doors and the left hand landing gear strut. OMG that was awful. There were painting disasters, disbond issues, fractured parts too numerous to count. But there were also moments of huge victory and accomplishment and pride. I think perhaps the most interesting and successful element of this build was the use of a 3D printed highly accurate fuselage assembly jig. Here is a picture of it: With some fuselage parts loaded onto it: I show this because this jig provided the foundation for the entire build - an accurate forward fuselage with cockpit, and accurate attach points for the wing, engine cowling, and aft fuselage. Had to have that before everything else. Another interesting element of this build was my decision to use 3D printed transparencies. As opposed to vacuform. Injection molded parts were of course not an option. Ultimately most (but not all) the canopy and windshield and aft window parts were provided by Shapeways at high prices, after I just flat failed on many of those parts. The concern of course was clarity. Most of the followers of the build were very skeptical of 3D printed clear resin to deliver. I will let you judge for yourselves. The area where I had to do some serious guesswork was the Malcolm hood and the cockpit modifications for same. Dozens of pictures both period and from restos helped immensely. During that time of the build, I learned a whole lot about the Malcolm hood modification, and how involved it actually was. Some of you may not be aware that the Malcolm hood was a field modification entirely. A -B or -C (or even an -A) model would go into the field hangar, and several days and hundreds of man-hours later, it emerged with a big fishbowl sliding hood replacing the greenhouse style canopy found on production aircraft. The mod was a big deal - major surgery for the cockpit. Pilots absolutely loved it, as seeing was life (along with speed and fire power). Visibility with the Malcolm hood was superb. At any rate, the hood was driven by a crank handle and chain drive. I am not aware of any modeler other than myself attempting to model the various cockpit modifications for the hood. Look for that in the pictures. This model is heavy - about 2.5 pounds or so. So the landing gear struts needed help, especially the tail gear. This was the first time I re-inforced landing gear struts with metallic rod (brass or music wire steel). Here is a picture of the tail gear strut and an internal stiffening rod formed on a 3D printed forming block of my own design: The main gear struts were re-inforced similarly. The re-inforcements have worked. To my horror, after the main gear were installed onto the airplane, I discovered the rake angle was off by a noticeable couple of degrees. That after being so careful to design it right. I still don't know what happened. So I created a fixture where pressure could be applied over days to the gear struts via shims with ever-increasing thicknesses, to force the struts back to a correct rake angle: See the white shims? I show this because it was some of the most stressful days of the build - hoping to get some permanent deformation on very stout gear support parts without breaking something important. Believe it or not - it worked! The hope of course is that it stays that way. Lastly some details to look for in the pictures: - Mismatched tires (you see alot of that in period pictures) - 3D printed chains nested in the upper longerons which drive the Malcolm hood - 3D printed clear transparencies - External rails and rollers for the Malcolm hood - Spitfire-style exteral rear view mirror - Malcolm hood that can actually be slid fore/aft (if very careful) - Movable tail surfaces - Head rest pad and seat back pad (thank Antonio Argudo for that!!) - The crazy shaped bomb racks Here we go: I guess that is enough. I would like to thank first of all the 40 or so followers of my build thread. All were very patient and supportive during the 2-year effort. And special thanks to Airscale for giving me the extensive decal set for his 1/18 P-51C Lopes Hope, hundreds of pictures, and a few helpful Rhino files. Oh, and the 1/18 scale seat belt hardware. Also Antonio Argudo for designing some really great models for me - the head rest, seat back cushion, and tail gear bay canvas cover. Also Thunnus who provided me with nose art decals and stencils, and stencils for other things like squadron buzz letters, tail serial numbers, national insignias, and kill markings. Also TAG and Antonio for priceless period pictures of anything and everything P-51B. And lastly Aircorp Library - OMG. Their collection of engineering drawings and other documents is absolutely priceless. I hope you like Cripes a' Mighty. She is not perfect, and she appears rode hard and put up wet. But it is the best I can muster! Thank you.
-
JayW reacted to a post in a topic: 1/18 Scale P-51B 3D Print Build
-
JayW reacted to a post in a topic: 1/18 Scale P-51B 3D Print Build
-
JayW reacted to a post in a topic: 1/18 Scale P-51B 3D Print Build
-
Well heck y'all. Or bloody hell in old English. The LH 75 gallon tank actually can be inserted into the hooks of the bomb shackles and stay in place as designed (the RH tank not so much). Here it is in all its glory: To my eye, that looks pretty darn cool. And, adding the fuel supply and pressure lines would add to the look. As well as the decals that are not there yet. What is lost is the unobstructed view of the landing gear and gear door, in a side view at least. What I think I cannot do is have this tank removable. For the reasons I already went through - the model is too fragile to subject it to alot of handling. So, I think this P-51 is either going to be with drop tanks, or without. I am on the fence. I would love to see some opinions from those who have been following this.
-
JayW reacted to a post in a topic: 1/18 Scale P-51B 3D Print Build
-
JayW reacted to a post in a topic: 1/18 Scale P-51B 3D Print Build
-
Can anyone provide some pictures?
-
JayW reacted to a post in a topic: 1/18 Scale P-51B 3D Print Build
-
JayW reacted to a post in a topic: 1/18 Scale P-51B 3D Print Build
-
The last project on Cripes a Mighty would be the bomb racks. These (the real thing, on Lope's Hope): Surprisingly, effective on -B/C models, the bomb rack is made of some kind of internal re-inforced molded plastic. Earlier versions were magnesium (on -A models, A-36, etc - I think). The two configurations vary a bit but not much. Anyway, the drawing says the rack is to be gray, to match the underside of the wing with the standard gray and OD paint job that these aircraft were delivered with, up until they began to arrive with un-painted aluminum. As discussed already, -D models introduced an entirely different rack. Also previously discussed was sway brace bolts, and whether or not they included the large round pads. Mine would have the round pads: I designed the holes in the pads to have a lip at the opening with a tiny bit of interference fit for the bolt ends. And the bolt ends had a bit of a bulge at their ends to snap into place in these holes. The bolts: See the bulged ends? Put together (carefully) and I got this: Snap! Yes they actually swivel. I was amazed - true micro-engineering. There they are next to my 3D printed and gray painted bomb rack. For the umpteenth time, I thank Airscale for the decals. My intent here was to be able to mount 75 gallon tanks and have the pads swivel into place with little to no gap betwen pad and tank. It worked, but read on. A finished bomb rack with sway brace bolts: And here are the 3D printed tanks: I had to do some educated guess work as to the shape and size of the tanks. Both my racks and my tanks are designed at the attach points for removal and re-attach. It works somewhat but not great. In real life the tanks were identical, but I have a LH and a RH tank. That is because the little fittings where fuel lines connect are oriented differently LH to RH. These tanks are not ready for prime time, and will receive decals one day. But for now, I have decided NOT to use them. I never intended drop tanks to be installed permanently on Cripes - they hide too much of the landing gear and I do not want them hidden. They would instead be removable. But I have found that what I have here is an amazingly large, unwieldy, and fragile P-51 model. Every corner of it has something that breaks off all too easily. And installing or removing those tanks, along with their plumbing, would be a labor intensive and delicate task, subjecting Cripes to part breakage every time I mess with it. MOF - turning the model upside down to install the racks resulted in this: The external rear-view mirror broke off, after being on the aircraft for what - a week? Well, that was merely an opportunity to tweak the mirror design a bit - a touch shorter, with slightly wider base pads - print it up with some spares, and re-bond it to the windshield. No prob. But - the wing tips are uber-fragile, and the fix is much much more complicated. Here one is, BTW, finally freed from its protective padding and tape: Just look at how delicate that tip is. It just had to be a frequent maintenance item during the war. I am proud of it and I do not intend for it ever to be subjected to potential for breakage. Other parts are very fragile. The pitot mast for example, that part very close to the bomb rack. The gear doors - they cannot be bumped or the links will break. That would break my heart. The movable tail feathers - also fragile. So I will keep the tanks around, but I will not install them at this time, perhaps never. Here is Cripes with its newly installed bomb racks: Pan back and you see here the final WIP picture of Cripes, with her racks and new mirror, before I put together the RFI post: Oh one more thing - Antonio made up a model of pilot George Preddy,and gave me the file. After some back and forth about George's height (he was a fairly small person I understand), I scaled him to be about 5 foot 6 inch and printed him up. And here he is: Dam Antonio - you are one talented dude. I will paint him one day, but not today. OK RFI post upcoming. Thank you all so much for sticking with me on this 2-year adventure. So appreciated.
-
Wow - it's been a minute Guy. That wing, when you pan back a bit, looks like a real wing. It's just spectacular. You have a gigantic project going here, glad to see you are back in business!
- 1,592 replies
-
- scratchbuild
- rivets
-
(and 4 more)
Tagged with:
-
1/24 Spitfire Mk IXc, Kicked Up A Notch, July 6/25. On hold for now.
JayW replied to chuck540z3's topic in Works in Progress
Here in western TN, USA, I have the opposite going on. In the heat of the day, everyone who is sane, or who doesn't have to, stays indoors. So I get some of my best modeling time during the summer. 😁 -
So y'all didn't think I was finished did you? The bomb racks and the 75 gallon tanks have been occupying me lately. I realized fairly quickly that if I am to make removable 75 gallon tanks a reality, then I have to integrate the design of both. So I have begun the design of the bomb racks from scratch - a Rhino adventure extraordinaire, what with the teardrop shaped sway brace cross-sections and ends, and their faired connection to the rack housing. And also the tanks from scratch - easier. Some guesswork on the tanks; no guesswork on the racks. Here is what I have so far: Parts will be printed up in the next few days I think. Will report out soon as I can. Then it will be RFI.
-
Similar questions - where do you put these dioramas? Including this one which is stunning!
-
Gosh Peter - I agree with these other folks. The model itself is so convincing, but with the base, it looks very fast! I have a new-found interest in the scooter.
-
Well Kevin I am glad you like it; I am not as impressed. First of all, nearly all the model is skinned in aluminum. That alone will give you a realistic metallic finish. But for me, it is too new looking. Fine for a factory fresh subject. But my subject, Cripes a' Mighty P-51B, is far from factory fresh. It has seen a tough 1944 winter, a muddy spring, and some serious battle time. So I wanted the finish more flat and dirty. First though, in order for the metal to be painted without alot of lift-off, I sprayed the metallic surface with Tamiya clear X-22, thinned about 50% with lacquer. Got that trick from Chuck540z3, and it works as well or better than any self-etching primer I have found. Then any paint needed. Then I got it dirty and messy with Tamiya weatherine pastes and/or Flory wash. Then seal it with Tamiya TS-80 flat clear either air-sprayed or straight from the rattle can. I could have used sem-gloss instead and maybe gotten a better result. Don't know. Then, weeks and weeks of handling it, wearing some of it off. Add it all up and it looks pretty weathered. Not much science there, and some of LSP's finish masters could do much better. Thank you though! Ah yes. But the -B/C models all got the one I am going to use. The more streamlined one you speak of is used on the -D/K. You know OBG you are probably correct. A bombing mission interspersed with escort missions might necessitate changing out the padded bolts with the smaller versions. Not a difficult task for the ordnance guys. I am not sure at all if the padded versions would work well with the bombs. I think I am going to do some guess-work and make the padded versions. And I probably will not make the tanks. They tend to hide the MLG in a side view, and I am very proud of my MLG and doors. Instead this kite will have returned from a mission where the tanks were jettisoned. That might mean a raw tube hanging out of the wing. I'll research that.
-
Another thing - Peter, in the absense of engineering drawings, how are you coming up with all this fantastic detail? I have seen you do this on a number of your projects, where technical data is not there. I know that alot of pictures and diagrams can be had, short of acctual drawings, but how much guesswork are you resorting to? And I guess the same can be asked of the basic shape. Are there enough diagrams of the Tiffie's fuselage and wing cross sections that you can use with some confidence? Inquiring minds want to know.... 🤔
-
Well I have a few things - There are a couple of reason for 3D printing model aircraft. One, an IM kit might not exist, or if it does it might be inadequite. And two, IM may not get you the detail you are looking for. IM today is far better than IM yesteryear, but still there are limitations due to the rules Peter is getting familiar with. That is why there have been aftermarket kits out there for cockpits, wheel wells, etc. To model what cannot be modelled with IM. So what I would look for is to IM big parts in such a way as to not compromise the detail we want. Hopefully that is possible. And then 3D print the detail rich areas wher IM will surely fail us. As for part count - some good reasons for separate parts as opposed to integral one-piece parts might include detail painting. Another might be part detail. Even 3DP has its limitations when combining parts, which can be overcome by separating out parts. Lastly, some of us like the idea of building complicated multi-part kits. Pre-assembling in the form of one-piece parts that could be multi-piece parts can kinda take some of the fun out of it. So it is a balancing act. I would say design us a Tiffie that is super-accurate and super-detailed but offers some challenges for the modeler. Building is the fun of it after all. Drive on Peter - this is most exciting.
-
Something curious has come up WRT the bomb rack sway braces. Here is a picture from the installation drawing 97-63001, which shows the threaded sway brace bolts: The bolts are merely 4 1/2 inch long fully threaded bolts with a spherical head on them, 3/8 inch diameter. They look perfectly suitable for carrying bombs, which have hard thick casings. And these bomb racks were designed for bombs, not drop tanks. Even though we all know that as the war progressed, they were used primarily for drop tanks for long escort missions. Now look at this picture of Lope's Hope: Note the more familiar (at least to me) large diameter swiveling pads instead of the small diameter spherical bolt heads. More suitable, it seems to me, for the combat drop tanks which no doubt had thinner walls that might not do well with the small diameter spherical bolt heads. I cannot find anything in the P-51 drawing system that defines these sway brace bolts with the large pads. However I am all but certain they replaced the spherical bolt head type at some point. Can anyone help?