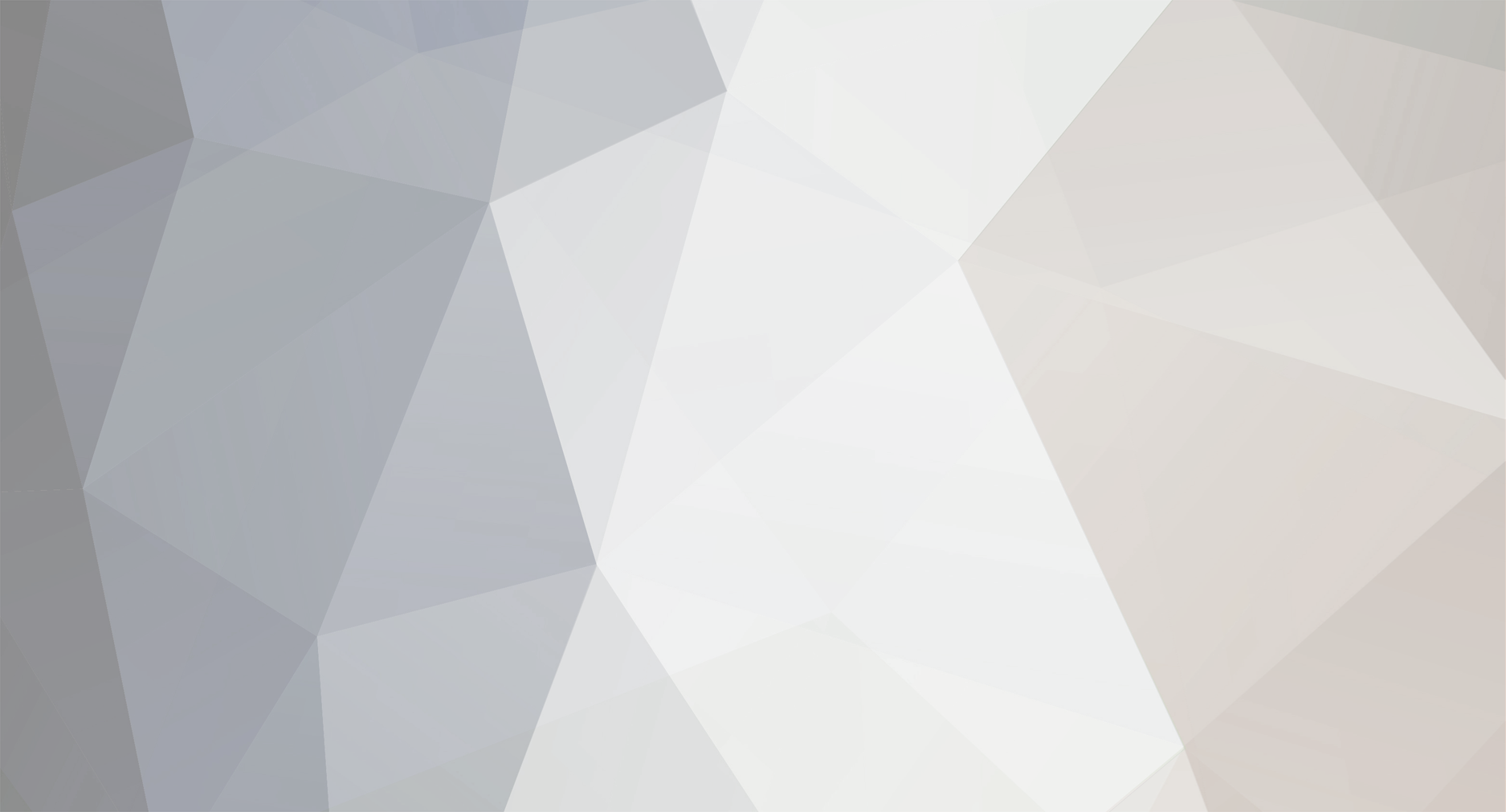
jumpjack
LSP_Members-
Posts
50 -
Joined
-
Last visited
-
jumpjack reacted to a post in a topic: 1/18 Hawker Sea Fury - VX628 - 1831 Squadron RNVR
-
jumpjack reacted to a post in a topic: RAF FG.1 XV571 WILD HARE Phantom Conversion
-
jumpjack reacted to a post in a topic: 1/18 Hawker Sea Fury - VX628 - 1831 Squadron RNVR
-
jumpjack reacted to a post in a topic: 1/18 Hawker Sea Fury - VX628 - 1831 Squadron RNVR
-
jumpjack reacted to a post in a topic: 1/18 Supermarine S6B - S1595
-
jumpjack started following DESERT STORM! Building the new Revell Hurricane kit , 1/18 Hawker Sea Fury - VX628 - 1831 Squadron RNVR , JETMADS 1/32 X-3 Stiletto and 7 others
-
jumpjack reacted to a post in a topic: Airfix 1/24th scale Mk.IX Spitfire........March 2024. All done
-
jumpjack reacted to a post in a topic: 1/24 FA.2 Sea Harrier Conversion
-
Biggles87 reacted to a post in a topic: Airfix 1/24th scale Mk.IX Spitfire........March 2024. All done
-
geedubelyer reacted to a post in a topic: Airfix 1/24th scale Mk.IX Spitfire........March 2024. All done
-
jumpjack reacted to a post in a topic: Pennys Pitstop HKM 1/32 Lancaster (Plus Intro)
-
jumpjack reacted to a post in a topic: Airfix 1/24 Hawker Tornado, 2nd prototype P5224
-
jumpjack reacted to a post in a topic: Airfix 1/24 Hawker Tornado, 2nd prototype P5224
-
Landrotten Highlander reacted to a post in a topic: Airfix 1/24th scale Mk.IX Spitfire........March 2024. All done
-
Airfix 1/24th scale Mk.IX Spitfire........March 2024. All done
jumpjack replied to geedubelyer's topic in Works in Progress
I by mine in traditional 'corner shops', the sort of place that still stocks stuff the supermarkets will tell you is no longer made/illegal to sell etc. Main uses for me are removing tape residue, degreasing and thinning enamels. -
daHeld reacted to a post in a topic: 1/18 Hawker Fury
-
daHeld reacted to a post in a topic: 1/18 Hawker Fury
-
daHeld reacted to a post in a topic: 1/18 P51C Mustang "Lopes Hope the 3rd"
-
-
Panzerwomble reacted to a post in a topic: DB Model Kits will release de Havilland DH.103 Hornet & Sea Hornet in 1/32
-
scvrobeson reacted to a post in a topic: DB Model Kits will release de Havilland DH.103 Hornet & Sea Hornet in 1/32
-
thierry laurent reacted to a post in a topic: DB Model Kits will release de Havilland DH.103 Hornet & Sea Hornet in 1/32
-
Rick Griewski reacted to a post in a topic: DB Model Kits will release de Havilland DH.103 Hornet & Sea Hornet in 1/32
-
As the restoration of TT193 gets under way by Pioneer Aero in New Zealand there will be a greater world wide awareness of the Dh103 , and keen interest in securing the to-date elusive 'accurate model'. It would seem those now closest to the definitive source material are the ex Wingnut folks of Kotare. Regarding market viability, the following are amongst those who have been convinced; Frog (1/72), Dynavector (1/48), Classic Airframes (1/48),Special Hobby (1/72), HPH Models (1/32) and the currently available AZ Models plastic kits and Oxford diecasts in !/72 plus the strange 1/48 renditions of Trumpeter with a 1/32 vacform on the pending list of Tigger Models. Not bad for a subject of ' little wide interest'. Les
-
Seems appropriate to mention this here- I build a lot of fuselages/bodies with a bread and butter profile technique and have learned not to use superglue. Its shrinkage produces wonderful bananas! Les
-
Have you seen that Kinetic has recently issued a 1/48 kit of the Pucara with what may be some useful reference graphics appearing on the web? EG, some renditions including cockpit here #https://www.besserepreise.com/modellbau/kinetic/kinetic-maßstab-1:48/kinetic-k48078---ia-58-pucara-in-1:48.htm Les
-
Hi Peter- Limonene (as sold by Mr Cement but widely available as a commercial product) is a much less aggressive solvent useful for bonding very thin styrene to styrene and other material with a surface key. Smells of citrous fruit. Seasonal Best Wishes to All.
-
And there was me hoping for a Wyvern TF1! Should it come to making brass look like steel/aluminium, I guess you know about 'immerse tin powder@ used for cold tinning? Les
-
RAF FG.1 XV571 WILD HARE Phantom Conversion
jumpjack replied to Anthony in NZ's topic in Works in Progress
FWIW, I did some very similar butchery to my Revell 1/48 FGR to eliminate the fuselage/wing joint issues. -
De Havilland DH 82 'Tiger Moth' - Matchbox
jumpjack replied to kkarlsen's topic in Works in Progress
Excellent- thanks for the Queen Bee clarification. I wonder if any still fly in private hands. Sorry fo the topic diversion. Les -
De Havilland DH 82 'Tiger Moth' - Matchbox
jumpjack replied to kkarlsen's topic in Works in Progress
Wasn't the floatplane Tiger Moth known as the Queen Bee? -
I sometimes wish the AM resin suppliers would offer some sort of premium service optimized for minimum shrinkage. I do a fair bit of home casting and generally use clear acrylic resin for just this purpose. Some of the resin aircraft I have bought have demonstrated up to 10% shrinkage- always assuming the masters had been worked to some closer approximation of actual scaled dimensions! les
-
Brilliant masking! Just a question- were the blades entirely wood with no leading edge sheathing? les
- 340 replies
-
- rb productions
- zoukei mura
-
(and 1 more)
Tagged with:
-
1/32 ERA-3B Skywarrior - 3D printed / scratchbuilt
jumpjack replied to Starfighter's topic in Works in Progress
I was intending to ask your recommendations for 3D print glues! feeling your pain. Les -
1/32nd scale Avro Shackleton - scratchbuild project
jumpjack replied to tomprobert's topic in Works in Progress
Is this one of the more welcome results of Corvid isolation? Les- 452 replies
-
- Scratch-build
- 1/32nd scale
-
(and 1 more)
Tagged with:
-
May I suggest the gear door fits may well have varied from aircraft to aircraft and have been adjustable to fit the particular airframe? (wheels up test etc). I have dealt with enough refits (not aircraft) to demonstrate stuff as made only approximately fits a drawing and even more rarely matches a stablemate to the nth degree. Otherwise my hat's off to North American for perfection. Les