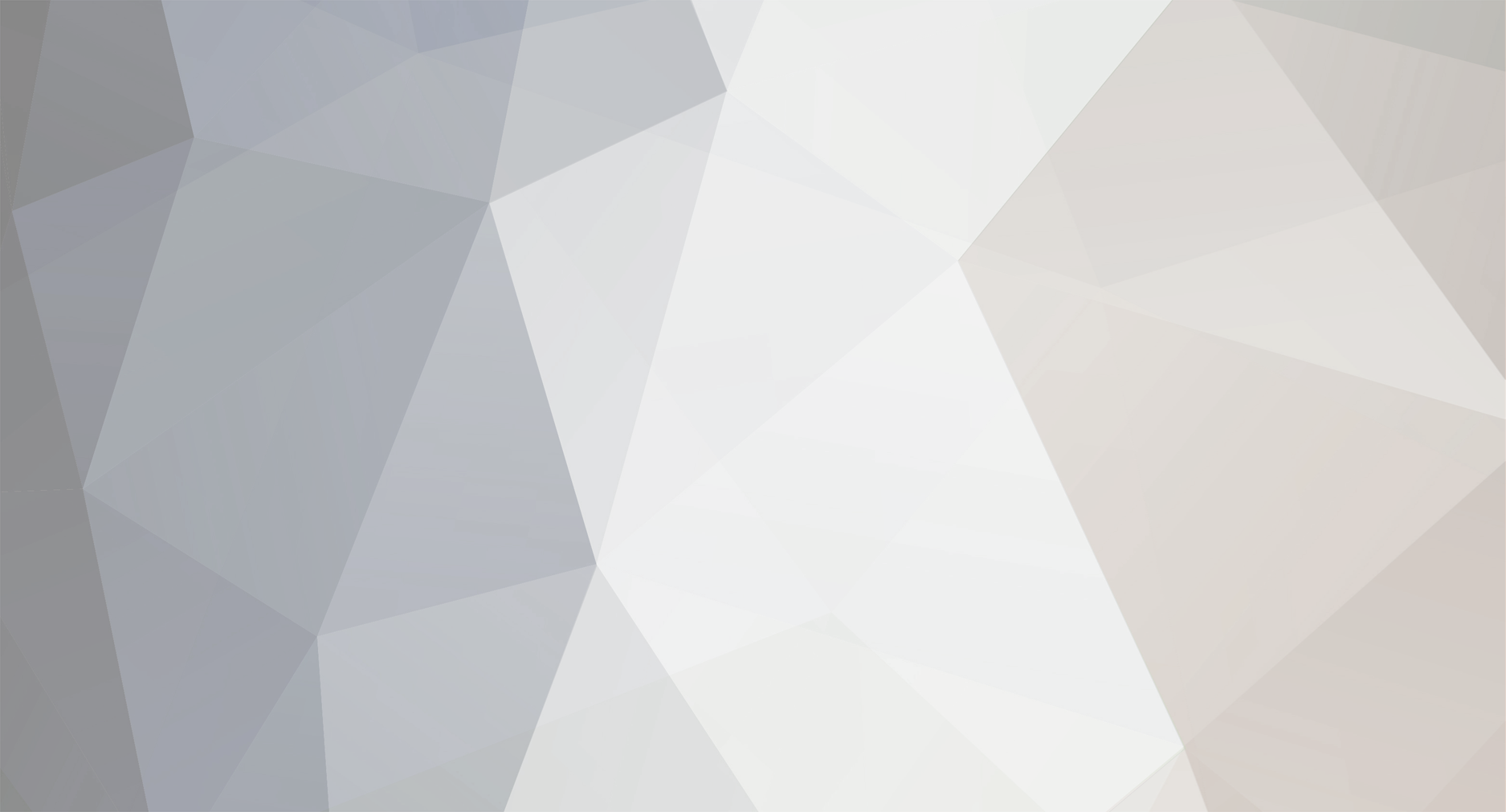
steinerman
LSP_Members-
Posts
114 -
Joined
-
Last visited
-
Days Won
1
steinerman last won the day on March 15 2020
steinerman had the most liked content!
About steinerman
- Birthday 08/13/1942
Profile Information
-
Gender
Male
-
Location
Grand Rapids, Michigan
-
Interests
Modeling, Computers, photography, gardening, trains
-
KiwiZac reacted to a post in a topic: HPH has closed up?
-
scvrobeson reacted to a post in a topic: HPH has closed up?
-
chezzie reacted to a post in a topic: HPH has closed up?
-
Kagemusha reacted to a post in a topic: HPH has closed up?
-
Damn, I was saving up to buy the B-36. Was about 2/3rds there. Now I have a boatload of AirScale 1/48 instrument kits as well as bottles and bottles of Alclad paint and primer for this beast. CRAP!!!
-
steinerman reacted to a post in a topic: The Christmas Lizard
-
MikeC reacted to a post in a topic: Accuracy conundrum - settings
-
Just one statement. I build for fun and enjoyment. To me, it's a hobby and something I find relaxing. 100% accuracy comes a distant second.
-
Sepp reacted to a post in a topic: A note of appreciation to the folks at Airscale
-
Christa reacted to a post in a topic: A note of appreciation to the folks at Airscale
-
scvrobeson reacted to a post in a topic: A note of appreciation to the folks at Airscale
-
D.B. Andrus reacted to a post in a topic: A note of appreciation to the folks at Airscale
-
Uncarina reacted to a post in a topic: A note of appreciation to the folks at Airscale
-
steinerman reacted to a post in a topic: A note of appreciation to the folks at Airscale
-
steinerman reacted to a post in a topic: A note of appreciation to the folks at Airscale
-
steinerman reacted to a post in a topic: A note of appreciation to the folks at Airscale
-
steinerman reacted to a post in a topic: A note of appreciation to the folks at Airscale
-
steinerman reacted to a post in a topic: A note of appreciation to the folks at Airscale
-
steinerman reacted to a post in a topic: A note of appreciation to the folks at Airscale
-
steinerman reacted to a post in a topic: A note of appreciation to the folks at Airscale
-
steinerman reacted to a post in a topic: A note of appreciation to the folks at Airscale
-
I feel it necessary to give a big shout-out to the folks at Airscale for their prompt, courteous and friendly service. Too often we are quick to criticize but when it comes to showing our appreciation, we many times fall flat on our faces. After much deliberation I have decided that after my 5 year project of super, SUPER detailing the 1/200 Trumpeter USS Missouri (Search for "USS MIssouri in the Non-LSP section) I needed to take a rest from ships. I have several aircraft and armor in my stash but I'm getting the itch to go big again. So, I'm going to build HPH's monster 1/48 B-36 Peacemaker. Yeah, I know, I'm crazy as a loon, and, knowing me, I'll probably want to detail the heck out of it. I haven't bought the actual kit yet - still saving up $$$$, but as I get free money, I am buying reference books and add-ons. This is where Airscale comes in. The B-36 cockpits have literally hundreds upon hundreds of dials, instruments, nameplates and the like. The flight engineer's panel has so many it takes 2 crewmen to operate it. Little by little, I'm buying Airscale packets to fill out the instrument panels with as much realism as I can. The folks at Airscale have been prompt, friendly, and helpful - so much so that I felt the need to pass on my appreciation and thanks for their remarkable service. Thank you, Airscale. You have a customer for life! Larry Steiner
-
steinerman reacted to a post in a topic: Veterans Day thanks
-
Very nice! Top notch work!!
-
Hi Peoples, Unless I'm hallucinating, I saw, sometime ago, a blurb from Res-Kit indicating that a landing gear set for 1 1/32 scale F-14D was forthcoming. Their catalog lists a set for 1/48 scale but none yet for 1/32. Does anyone know if this is still in the works, or did they figure the demand wasn't there? Thanks, Steiner
-
OMG!!!
-
Hey, Chuck, This is off topic, but what's the fire situation up around where you live? From the way the news is around here, the entire country is pretty much on fire. Are you safe?
-
I'd sing Happy Birthday to you, Chuck, but I'm afraid they'd kick me off the site if I did. Hope you have a great day and get lots of fun toys!!
-
I did what you suggested and the email came back undeliverable. Are they still in business?
-
I am sort of toying with the idea of buying HPH's big honking 1/48 model of their B-36. Nothing definite yet, but I'm thinking about it. I don't know how many of you saw my thread in "Non-LSP Works" on my Trumpeter 1/200 USS Missouri model. Well, I recently sold the ship for $3000 and I'm contemplating spending part of that money on another monstrous model. No, I'm done with ships for a long while! The HPH website lists this model for 475 euros, which is about $525 in US funds. For what you get, I feel this is a reasonable price. The thing I'm wondering however, is what the shipping charges would be to Michigan USA. I can't determine anything from their website and was wondering if anybody here had any wise ass guess as to the shipping cost. Are we looking at $50? $75? $100? or what. Any ideas?? Steiner
-
Evening Friends, Do any of you know of, or have any of you ever heard of anybody coming out with a 1:32 scale F-111? ScaleMates shows a vacuum formed kit but that's not my cup of tea. Stein
-
Tamiya F-15J - Umegumi, 305 Squadron
steinerman replied to themongoose's topic in Ready for Inspection
Now that is a work of art! - And a labor of love. Fantastic results, my friend. It's a winner! -
Welcome to the joint, Joe. We're all a little crazy here, so if you don't mind hanging put with a bunch of oddballs you should be happier than a fly on s**t. So, you're 68 and retired, huh? That means you're just a youngster as far as I'm concerned (81 in August). I hope you have a lot of fun here and learn a lot of new things. And, if you haven't already found out, this can be a very expensive hobby!!! And most important of all: THANK YOIU FOR YOUR SERVICE!!
-
I ordered mine from Sprue Bros. Should be here tomorrow. Can't wait!!