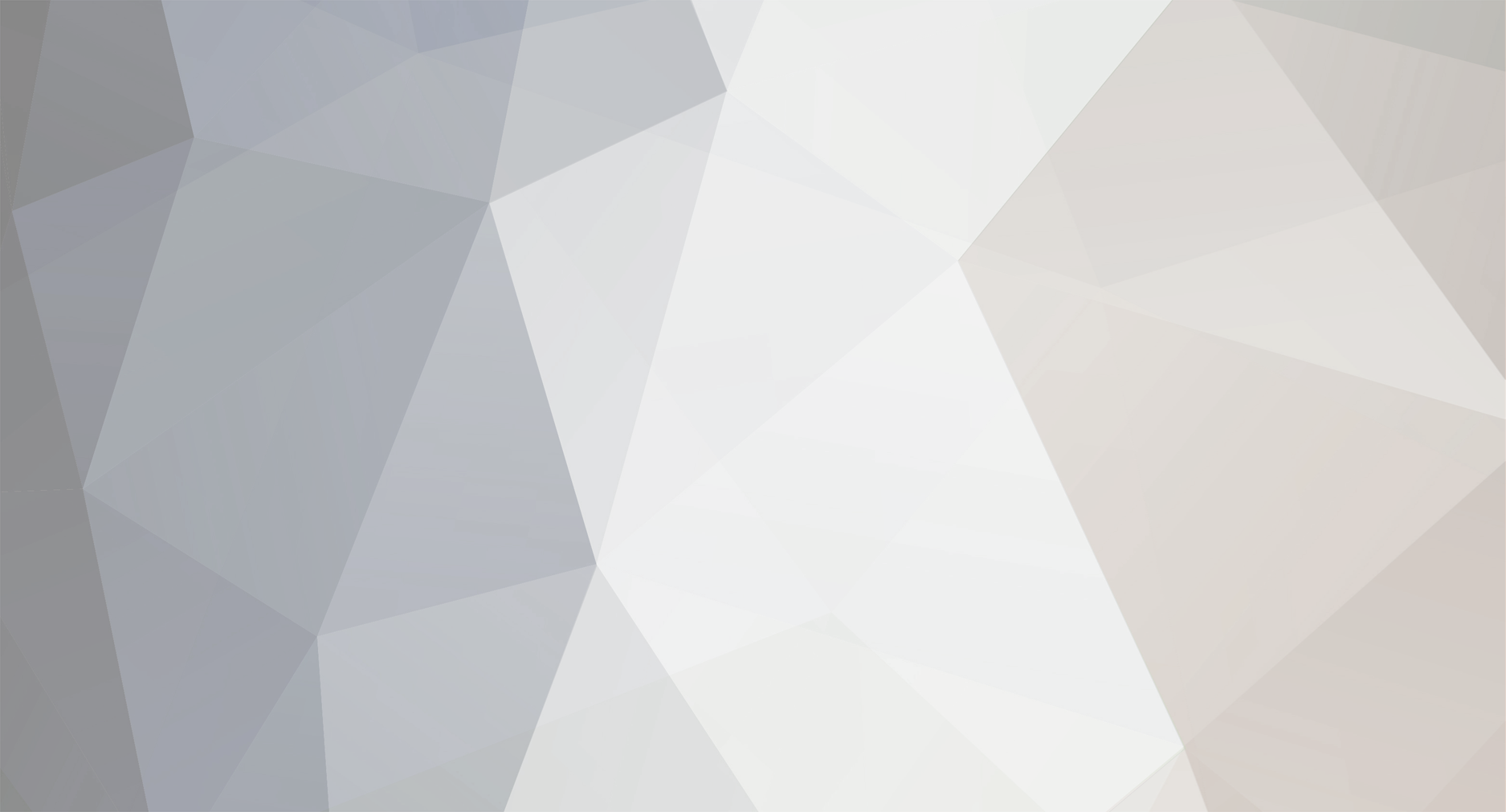
Basilisk
LSP_Members-
Posts
85 -
Joined
-
Last visited
Profile Information
-
Gender
Male
-
Location
Melbourne, Australia
Recent Profile Visitors
2,060 profile views
-
Greg W reacted to a post in a topic: My 109 Addiction: Bf109G6 in 1/48: Build-off! Complete
-
Alain Gadbois reacted to a post in a topic: Me109 E seat in 1/32? Any without the belts?
-
nmayhew reacted to a post in a topic: Me109 E seat in 1/32? Any without the belts?
-
Fanes reacted to a post in a topic: Me109 E seat in 1/32? Any without the belts?
-
LSP_Kevin reacted to a post in a topic: Me109 E seat in 1/32? Any without the belts?
-
I think the Dragon seat is a bit too narrow at the top. I widened the one in my build a little, not too hard to do. Should get back on this build. Cheers, Peter
-
Gigant reacted to a post in a topic: WNW Junkers D.1
-
Great finished model. I currently building this model (my first WNW kit) in the Britmodeller Great War GB. I am afraid, it wasn't steel, it was Aluminium! I think you got some numbers mixed up The Junkers J.1 and J.2 where built with steel and mainly spot-welded, but ended up too heavy with poor climbing performance but a great top speed of 170km/h. Junkers then changed to using Aluminium on the J.3, but as this development wasn't funded by the military, the aircraft was never finished. He then used the Aluminium building method he developed when working on the J.3 in producing the J.4 (Army type J.I), which was the first (nearly) all metal constructed aircraft built in quantity. From then on all his upcoming aircraft used Aluminium as the construction material including the J.9 (Army type D.I). Looks to me you confused the Junkers J.1 with the Junkers D.I. There is an excellent new publication on Junkers' early aircraft development by Aeronaut Books in two volums and they are an interesting read. Cheers, Peter
-
mustang1989 reacted to a post in a topic: 1/48 Tamiya Me 262 A-1a from III./JG 7 flown by Major Rudolf Sinner
-
mustang1989 reacted to a post in a topic: My 109 Addiction: Bf109G6 in 1/48: Build-off! Complete
-
LSP_Kevin reacted to a post in a topic: 1/48 Tamiya Me 262 A-1a from III./JG 7 flown by Major Rudolf Sinner
-
DonH reacted to a post in a topic: 1/48 Tamiya Me 262 A-1a from III./JG 7 flown by Major Rudolf Sinner
-
1/48 Tamiya Me 262 A-1a from III./JG 7 flown by Major Rudolf Sinner
Basilisk replied to Basilisk's topic in Non-LSP Works
Thanks Brian. Yes, as soon as you add resin into a build things can get a bit complicated. Lud, Warbird explained it nicely. Thanks Gaz, so do I. Worked on the wings this week. I totally forgot to prepare the lower wing to accommodate the Aires parts for the slats. So some more scraping was in order. The outer undercarriage bays and the inner base for the slats in place. And the outer bases for the slats. As you can see, some rails for the slats are missing. No I didn't brake them, I received the parts with them broken. Fortunately they still where in the bag so that I can repair it later. The fitted parts of the undercarriage bay are a bit of an enhancement over the Tamiya rendition. The upper wing needed to be modified to accommodate the resin part. First the Tamiya representation of the undercarriage bay had to be removed. Then some more grinding was needed to make the wing fit without any interference. Looks ok now. But there are some gaps on the outer slat bases next to the engine mount which needs to be corrected before I glue the wings together. Thanks for watching. Any comments and suggestions are always welcome. Cheers, Peter -
Basilisk reacted to a post in a topic: First WnW: Albatros D.V Komplete 11/7/18
-
Great effort on your first WNW kit. But I have to make a comment on your prop. Event though many congratulated you on your prop, I feel it doesn't look right the way the separation runs between the layers. Your separation of the layers doesn't match the contour of the airfoil on the prop which makes it just not look right. Kind of surprised that no one has pointed this out. Cheers, Peter
-
1/48 Tamiya Me 262 A-1a from III./JG 7 flown by Major Rudolf Sinner
Basilisk replied to Basilisk's topic in Non-LSP Works
Much appreciate your reply. I came to the same conclusion and intend to paint mine also in 82/70/76 due to the high contrast on the pictures of the original. Would love to see your model painted with these colours. I am still undecided which way to go. The purpose of the late war camouflage was mainly to disguise the aircraft on the ground and a parallel pattern does make more sense than a V shaped pattern which wouldn't blend well with the background when seen from above. I did a lot of reading and looked through many photos and what you say is correct, but I see it different. The Me 262 was built to a large part with the use of (unskilled) forced labor and the quality of the finished airframe wasn't the best. And as the aircraft was urgently needed in Squadron use, the finish was rushed. Yes the rivet lines had been covered by putty, but only at spots where it didn't meet the RLM guidelines for surface finish, which meant that the application of putty varied from airframe to airframe. Here are two pictures from a post at Large Scale Planes which makes some interesting reading. Putty in place in front of the cockpit, but not below the cockpit. And here the Aircraft at Hendon. And the wing surface of the Hendon aircraft. At the end it is a personal choice to rivet or not to rivet. Cheers, Peter -
Basilisk reacted to a post in a topic: My 109 Addiction: Bf109G6 in 1/48: Build-off! Complete
-
My 109 Addiction: Bf109G6 in 1/48: Build-off! Complete
Basilisk replied to Gazzas's topic in Non-LSP Works
Nice progress Gas. Are you still waiting for the upper wing replacement from Eduard? I am currently doing a similar comparison at Britmodeller, but included the Zvezda kit into the mix. I am still in the cockpit assembly stage, so it is interesting to see your experiences with the two builds. I found the Tamiya kit the leader of the pack in regards to accuracy and amount of incorporated detail. The Eduard kit on the other hand is lacking in detail (compared to the Tamiya kit) and has a lot of errors when it comes to detail which is a real shame. And as you already noted, the Eduard fuselage is unfortunately still a bit out of wack, being too tall and too wide behind the cockpit. And yes. it is not by much, but still results in a noticeable difference. Talking about noticeable, I question the accuracy of the AK Interactive 74 and 75 tones. I am not an expert, but the contrast between the two looks very low on your model and 74 looks more like an olive green, at least on your pictures. The picture below is the Australian 109G which as far as I know is still in the original colours. Looking forward seeing your progress. Cheers, Peter -
Basilisk reacted to a post in a topic: 1/48 Tamiya Me 262 A-1a from III./JG 7 flown by Major Rudolf Sinner
-
Basilisk reacted to a post in a topic: 1/48 Tamiya Me 262 A-1a from III./JG 7 flown by Major Rudolf Sinner
-
1/48 Tamiya Me 262 A-1a from III./JG 7 flown by Major Rudolf Sinner
Basilisk replied to Basilisk's topic in Non-LSP Works
Thanks Kev. It's nice to be back and my two LSP builds are not forgotten. Indeed Kevin, but it is my first since I built the old Airfix kit in the sixties. Did try something new with this build and it will be interesting to see how it work out at the end. Stressed skin effect After I got this far I thought I better buy a new kit as this doesn't look too good. But then I thought just get on with it and see how it works out. Here I thought maybe not everything is lost I used the round chisel in the top of the picture to scrape the "dents" in the plastic. After several trials to polish the surface I found a 600 grid sanding sponge is working wonders. After progressively using finer sponges up to 4000 grid the wing was ready to once more mark the lines where the rivets go. I then used above five Rosie the Riveters to add the rivets. The riveters with the red dot on it are double row riveters which ensure a constant width of double row rivets After another work-out with some sanding sponges the wings didn't look bad at all. But where is my stressed skin effect gone? Well, here it is. Have to lower the light to create shadows to make them visible. The question is, will the effect be visible on the painted model? I guess only under certain lighting conditions - as with a real aircraft. Did also some of the detail painting on the internal parts. This is still work in progress and the parts still need the final semi-gloss varnish to seal everything in. For the undercarriage bay I will airbrush some translucent yellow paint first as most of the pictures I have seen the aluminium has a kind of yellowish hue to it. And the cockpit tub is also done. Will finish it off after the tub is incorporated into the undercarriage bay. Thanks for watching. Any comments and suggestions are always welcome. Cheers, Peter -
Some seriously nice scratch building happening here with great results As you encourage comments, critiques, and criticism I like to mention one thing. After all the great work you done on the interior, I find the engines a bit underwhelming. Why not use your scratch building skills on them as well? Cheers, Peter
-
Basilisk reacted to a post in a topic: 1/48 Revell B-24D Fuselage Closed
-
1/48 Tamiya Me 262 A-1a from III./JG 7 flown by Major Rudolf Sinner
Basilisk replied to Basilisk's topic in Non-LSP Works
Had to start somewhere and chopping the wing apart to accommodate the slats was as good as any. Used a razor saw for the vertical cuts. And a scriber for the horizontal cut. Next was thinning the wheel bay surrounds. Right side is done. And all done here. The Aires outer wheel bay parts fit nicely. And the front part of the wheel bay fits well too. Also attached the PE stuff to the cockpit. I am not a great fan of that cream coloured resin as details are so hard to see. What I noticed on the Tamiya kit are rather thick trailing edges on the main wing and one thing I HATE are trailing edges out of scale. So had to do something about this. The wing on the top of the two pictures is how the trailing edge looks on the kit and the wing below that is the one I sanded down. Next in line was a coat of black primer and the base coats of some of the internal parts. Detail painting of these parts is next. Thanks for watching. Any comments and suggestions are welcome. Cheers, Peter -
1/48 Tamiya Me 262 A-1a from III./JG 7 flown by Major Rudolf Sinner
Basilisk replied to Basilisk's topic in Non-LSP Works
Here is the comparison between the Aires and the kit parts which is maybe of use for others. I do ask myself if the resin parts are a worthwhile addition. most of the additional stuff is the cabling, so will be interesting to see how it all looks with some paint on. One challenge with Aires resin are the instructions. They show how all the resin parts go together. But unfortunately no information at all how it all fits into the Tamiya kit -
I haven't been here for a while and when seeing Thunnus' excellent Me 262 build, I thought a comparison of building the Tamiya kit using Aires resin detail set is maybe of interest to some. I started this build three weeks ago, so progress is still moderate. I know I shouldn't comence a new build as I still have so much to finish .... The aircraft I chose is one of the two mounts from Major Rudolf Sinner, Gruppenkommandeur (CO), III./JG 7 in its attractive striped camouflage. All drawings of this aircraft show the stripes in a diagonal pattern across the whole aircraft. I couldn't find out from what information this originated, but based on the picture below, I paint the stripes in a V pattern. With the exception of the nose, all other stripes do line up reasonably well. Of course it could be a third aircraft in this camouflage, but I find this rather unlikely as III./JG 7 had only six aircraft on its strength. And if it is a third aircraft, my model will represent two aircraft - one on each side. If someone knows more about the origin of the "diagonal" stripes I would love to hear it.
-
Basilisk reacted to a post in a topic: VVS Yakovlev Yak-3 from the 402nd FAR, Spring 1945
-
VVS Yakovlev Yak-3 from the 402nd FAR, Spring 1945
Basilisk replied to Basilisk's topic in Works in Progress
Thanks Alex, I too like to read through other peoples builds as there is always something to learn from. I have to say that the side panels do bother me. Here a comparison. The extension where the trimming wheel is mounted should be part of the tubing and not above as on the kit. Extending the side panels so they cover the horizontal tube will then also hide the crack in it And here is how the real red cross kit does look like. Looks like still some work for me to do in the cockpit. Cheers, Peter -
VVS Yakovlev Yak-3 from the 402nd FAR, Spring 1945
Basilisk replied to Basilisk's topic in Works in Progress
Thank you Martin. Sometimes I wish not having an eye for details as it does slow things down... As promised in my last post, the next post will have the wings on. The fit was solala, but the bigest problem was that the wing was not sitting horizontally, creating a larger wing dihedral on the port side. I corrected this as much as I could by adding a shim to push the wing down on the port side. There was also a larger gap at the front of the fuselage to wing joint which I also filled with plasticard. Some of the resulting stresses when forcing the wing into place made the fuselage tubing crack on both sides in front of the seat. Also to make the tubing parallel to the hinge line, the cockpit insert needed to be raised by 1mm which I done with a shim when attaching the cockpit insert to the wing prior fitting the wing to the fuselage. All these little mismatch are unfortunately the hallmark of a short run kit. But I actually enjoying solving these challenges The next challenge is the correct placement of the two side panels above the metal tubing as the instruction is rather vague about it. This picture fortunately shows were they go. They are in line with the vertical tubing. And that how they look in the kit. This pictures shows unfortunately some discrepancies in the kits lay-out. The horizontal metal tubing is above the hing line covered by the wooden side panel construction. The kit has it below the hing line and not covered by the side panels. Unfortunately there are some other issues if you like to build the kit with an open cockpit. 1. You can notice that the two side panels stick out a little from the cockpit. I haven't seen this in any of the other builds. But it is most likely because i raised the cockpit insert by 1mm ... 2. The rail for the canopy to slide it open should go all the way where you can see the red line and not just at the rear. As it is on the kit is fine for a closed canopy, but not for an opened one. Same picture as above which shows this clearly. What it also shows is that the side panels are actually flush with these rails for the canopy! So after extending the rail, the location of the side panels will be correct, Lucky me. Oh, and I have to do something about the red cross box, just doesn't look right. Still a bit more work to be done around the cockpit. But first I will get the airframe cleaned up and completed which be a fair amount of work. So still lots to do. Cheers, Peter -
VVS Yakovlev Yak-3 from the 402nd FAR, Spring 1945
Basilisk replied to Basilisk's topic in Works in Progress
I think you are right with your assumption. Unfortunately it isn't an isolated case. Sets from Eduard, Quickboost and many others are in the same boat. Modellers think they have to be better and correct which isn't always the case. The good news is that I got some answers to my questions regarding the mystery pipe! KL at Sovietwarplanes had following information: "The pipe shown in the cockpit drawing is clearly labeled as "gil'zootvod" which means "spent cartridges chute". In early Yaks, empty cartridges were collected in canister which was located under the canon breach. Following diagram shows how cartridges and links were collected in Yak-9: Following drawing shows how cartridges and links were collected in "3-point Yak-3" Canister for empty canon cartridges was now located above the canon muzzle. Cartridge route is indicated with curved arrow in the left side of the drawing. If your model is a standard Yak-3 with 2 UBS, it did not have cartridge chute in the cockpit..." So it is confirmed that the pipe is the ejection chute for spent ammunition and wasn't fitted in the Yak-3 with two UBS guns! There is also a discussion about the radio arrangement of the A-Resin detail set on Scalemodels.ru which contains some interesting information of which this sketch is noteworthy. It shows all the components fitted which make up the radio system in a Yak-3. Most is not visible, but it clearly shows how the cabling was routed from the radio and as luck has it, I got it very close Unfortunately other commitments slowed things a bit on the build, but I got a few things done. I know I said the next picture will be of the completed cockpit. Well, it isn't complete yet, but I do have the new lap harness fitted and I think this harness made of paper looks stunning. But more important, it is now the correct type! Also got he gun blisters glued on. They still need a bit of work and the riveting will be re-done at the correct locations. The next post will be definitely with the completed cockpit and the fuselage on the wings. Promise. Cheers, Peter -
Basilisk reacted to a post in a topic: VVS Yakovlev Yak-3 from the 402nd FAR, Spring 1945
-
Basilisk reacted to a post in a topic: Tamiya Birdcage Corsair
-
Basilisk reacted to a post in a topic: Tamiya Birdcage Corsair
-
Basilisk reacted to a post in a topic: Tamiya Birdcage Corsair
-
Thanks Bryan for the additional information. Toothpicks are indeed some of the most versatile tools in making models I assume you airbrushed the Mig heavy chipping fluid. How long did you let the last coat dry until you airbrushed the MRP paint and did you do the chipping with a wet brush? I find the comparison between yours and Carl's chipping interesting. Yours represents chipping, that is paint flaking off and the effect is very realistic. Carl's on the other hand does look more like wear from ground crew sliding off the wing and looks very good too. Maybe the optimal effect would be a mixture of both methods where appropriate. I guess the study of pictures is the best guide. As I said, this is just an observation from someone who hasn't done any chipping to the levels shown here. Looking forward seeing your progress. Cheers, Peter