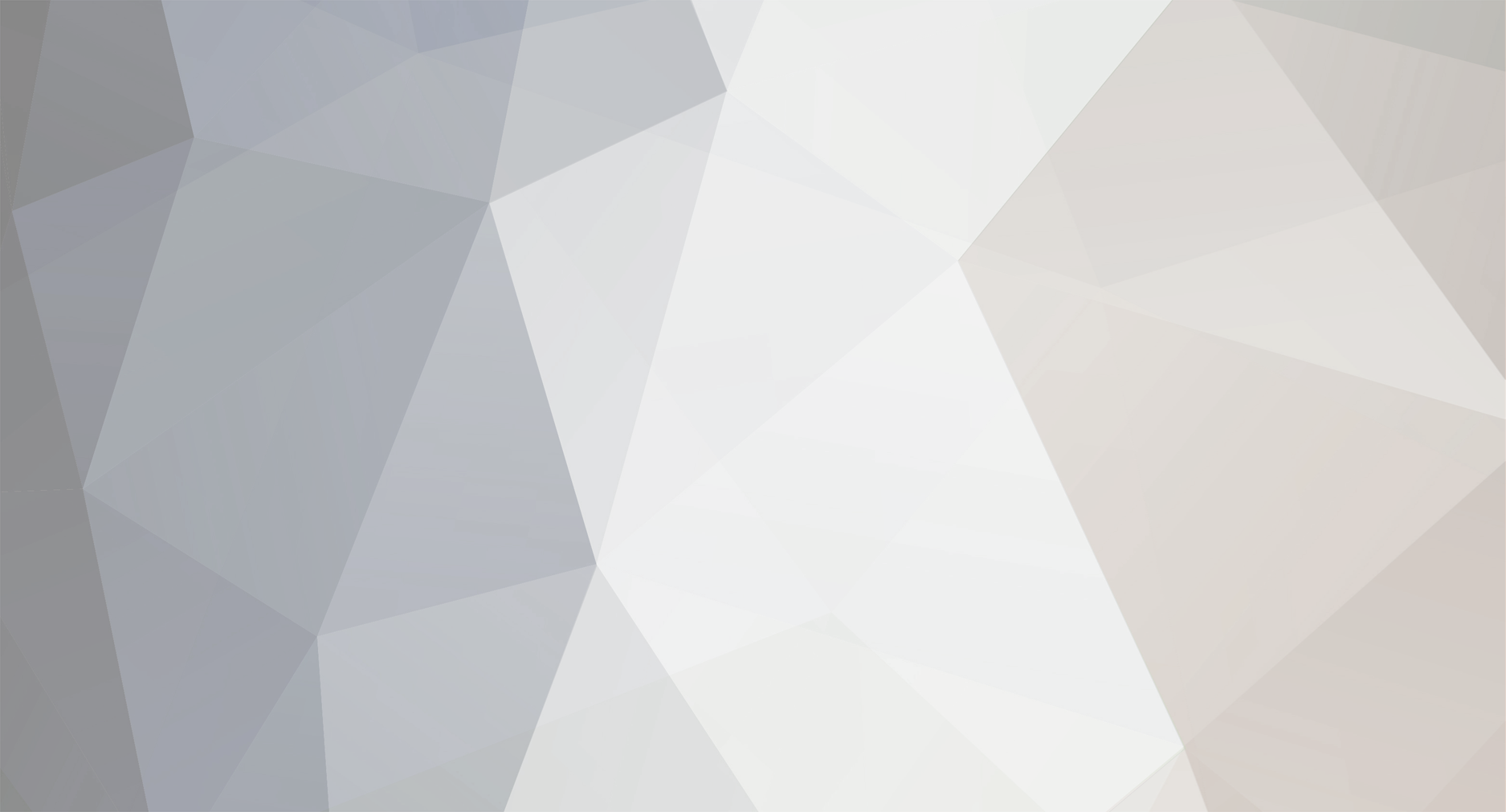
GMK
LSP_Members-
Posts
691 -
Joined
-
Last visited
-
Days Won
1
GMK last won the day on January 13 2022
GMK had the most liked content!
Profile Information
-
Gender
Male
Recent Profile Visitors
3,910 profile views
-
GMK reacted to a post in a topic: RAF FG.1 XV571 WILD HARE Phantom Conversion
-
GMK reacted to a post in a topic: Heavy Attack - US Army AH-64E Apache Guardian
-
GMK reacted to a post in a topic: New 1:32 Spitfire Mk.XII conversion on the way
-
Anthony in NZ reacted to a post in a topic: RAF FG.1 XV571 WILD HARE Phantom Conversion
-
GMK reacted to a post in a topic: 1/18 Scale P-51B 3D Print Build
-
GMK reacted to a post in a topic: 1/18 Scale P-51B 3D Print Build
-
GMK reacted to a post in a topic: Tamiya 1:48 F4U-1 Birdcage converted to FAA Corsair Mk.I
-
GMK reacted to a post in a topic: Tamiya 1:48 F4U-1 Birdcage converted to FAA Corsair Mk.I
-
GMK reacted to a post in a topic: Tamiya 1:48 F4U-1 Birdcage converted to FAA Corsair Mk.I
-
GMK reacted to a post in a topic: Tamiya 1:48 F4U-1 Birdcage converted to FAA Corsair Mk.I
-
RAF FG.1 XV571 WILD HARE Phantom Conversion
GMK replied to Anthony in NZ's topic in Works in Progress
Maintaining a really impressive level of quality there, mate. Well done. -
GMK reacted to a post in a topic: RAF FG.1 XV571 WILD HARE Phantom Conversion
-
So much so, I did my own.
-
Pretty excited - and I’ve already got my 1/16 build already done.
-
JayW reacted to a post in a topic: 1/18 Scale P-51B 3D Print Build
-
patricksparks reacted to a post in a topic: M1A2 SEP v3 - Australia’s new Abrams (1/16)
-
panzerrob reacted to a post in a topic: M1A2 SEP v3 - Australia’s new Abrams (1/16)
-
LSP_Ray reacted to a post in a topic: M1A2 SEP v3 - Australia’s new Abrams (1/16)
-
LSP_Kevin reacted to a post in a topic: M1A2 SEP v3 - Australia’s new Abrams (1/16)
-
Thanks, Ray. I’m pretty sure of the dimensions for the 1:1 fridge. I’m just hoping that the SEP v3-specific fitting on the bustle is scaled or located incorrectly, otherwise Army is in for an unpleasant surprise! One thing that has been a bit trickier than anticipated is the angle below the bustle where the bustle rack interfaces. Due to mold release considerations, the overall angles on the kit part aren’t perpendicular where you’d expect them to be. To resolve the integration piece, I’ve moved up the component tree one level. This part won’t be used on the build itself. You can see below how the kit bustle rack interfaces with the bustle along the top, horizontal surface, a vertical notch, & into the angled underside. As can be seen here with the kit bustle rack - this side omitting some parts - the angle I’ve calculated for the lower bustle is incorrect, causing a forward cant. Here’s the other side - excuse the print support remnants, I was in a bit of a rush - you may be able to see that the incorrect angle imposes fit issues & associated strain on the bustle rack uprights. Need a way to nail down that angle that’s better than trial & error! Thanks for looking in.
-
LSP_Ray reacted to a post in a topic: M1A2 SEP v3 - Australia’s new Abrams (1/16)
-
John1 reacted to a post in a topic: M1A2 SEP v3 - Australia’s new Abrams (1/16)
-
patricksparks reacted to a post in a topic: M1A2 SEP v3 - Australia’s new Abrams (1/16)
-
LSP_Kevin reacted to a post in a topic: M1A2 SEP v3 - Australia’s new Abrams (1/16)
-
Printed fit check. Bit worried that the fridge won’t open! Thanks for looking in.
-
Back to the bustle rack - this time for the VCSU (a.k.a. air conditioner) & the Australian-unique refrigerator. Will compete detailing of the fridge & mounting bracket before throwing them on the printer. Thanks for looking in.
-
Nice work, Jay, as always. If you’re in Canberra at any point, drop me a line!
-
Not much progress lately due to a bereavement in the family. Just messing with small, simple parts to keep things moving. 29 February 2024 was the handover of the first M1A2 SEP v3 to the Australian Army. I’m hoping that this’ll shake loose some images. On the v3, the rearmost skirt, sometimes referred to as #7, can be hinged forward 180 degrees & latched to the #6 skirt. When folded, this’ll be the inside part. Note the added dust/weather strip on the top. This’ll be the visible bit. The Tamiya upper hull is molded with the skirts attached, so the #7 on both sides were removed. Here’s a comparison between the kit components & the folded replacements. Time to do the weather strips along the top of the skirts. Thanks for looking in.
-
Nice work, Barry! I used the traditional methods for my Australian M1A1, but not to your high standards. Where did you get your mesh from? Really nice work. More fit & size checks. I’ve had a bit of trouble with the processor of my laptop handling the mesh models I’ve drawn, so may need to draw up the BRE for a third time. Ah well. New component time. No idea what this bit is called, but it’s unique to the SEP v3 & is located at the rear on the top of the turret. Thanks for looking in.
-
Thanks Tom, am enjoying the work. It took five sessions to re-draw the bustle rack & bustle rack extension, a lot shorter than the first go around. A lesson learnt from last time is incrementally adjusting the interfaces of the bustle rack with the rear of the turret before completing the detailing of the piece. The first interface step was horizontal spacing & the inlet step. The second was adding the top hangers, which was a problem on the first version of the part. Now I’ve added the mesh to the bustle rack & bustle rack extension assembly. A little bit of refinement to go & this is done. Thanks for looking in.
-
Brief segue back to the bustle rack & bustle rack extension. The previous iteration had been tweaked to be point that it was challenging my laptop’s ability to process it. Soooo, started it from scratch. Far easier & faster the second time around. Ideally it’ll be done before the start of the week. Here it is after two sessions. Unlike previous versions, the bustle rack of the SEP v3 has additional bracing at the corners. Thanks for looking in.
-
Moving on to the front of the hull, the lower glacis appears to have been thickened, along with the SEP v3 standard reinforcement of tow- & lift-points. Here’s the piece straight off the printer. Initial fit check. Will check the CAD vs the part to see whether shrinkage accounts for the alignment issues I’m seeing. Thanks for looking in.
-
1:18 Scale B-17G Flying Fortress Forward Fuselage
GMK replied to patricksparks's topic in Works in Progress
Feed chutes, now?! So good. -
Tamiya 1:48 F4U-1 Birdcage converted to FAA Corsair Mk.I
GMK replied to Rick K's topic in Non-LSP Works
Wow! That is some beautiful work right there. Very impressive. -
What I’m hoping is the last engine grill update prior to assembly & painting…. Looks like it’s all done & dusted. That was far fiddlier than expected! Thanks for looking in.