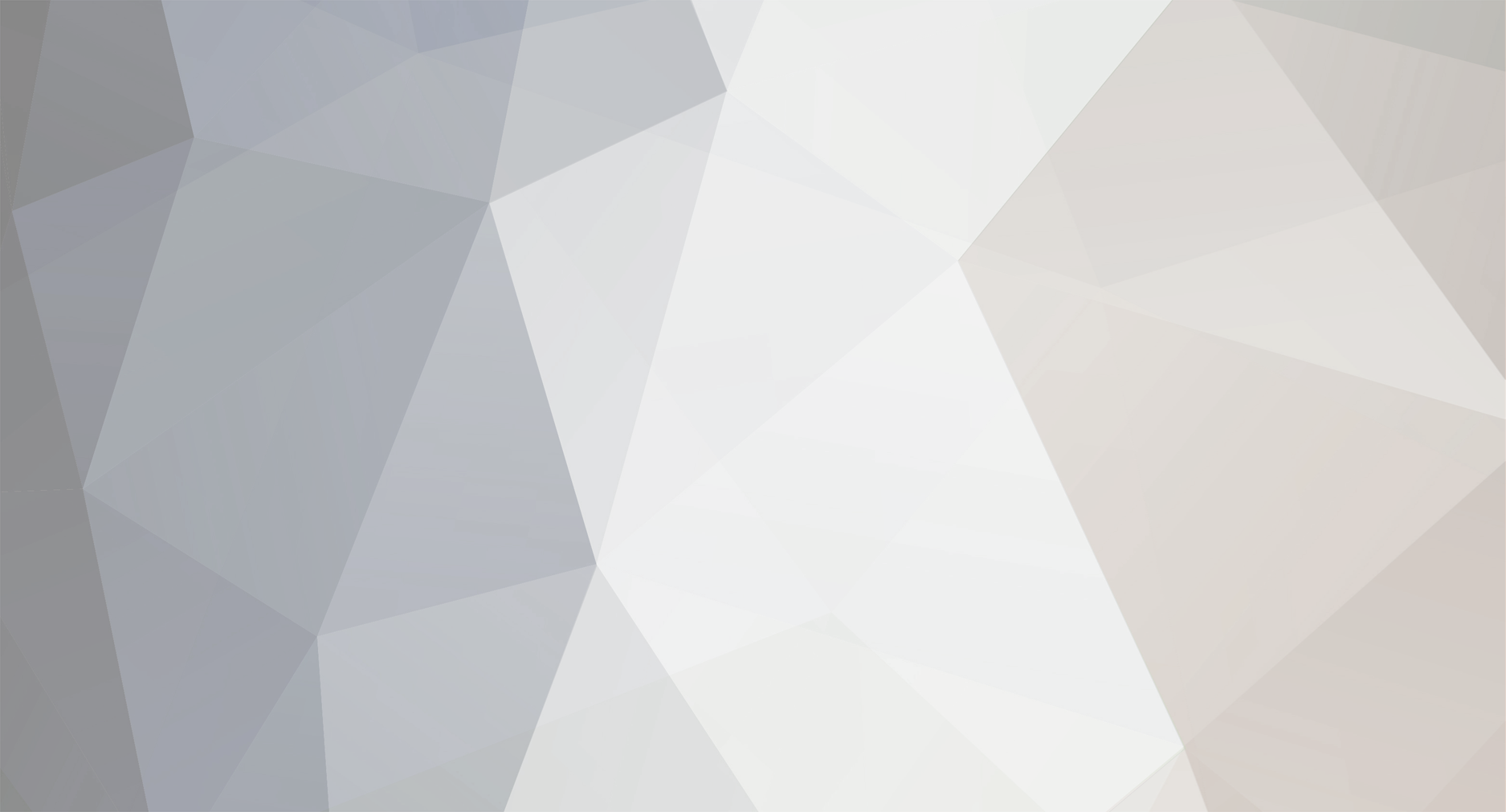
ericg
LSP_Members-
Posts
2,452 -
Joined
-
Last visited
-
Days Won
66
ericg last won the day on February 1 2021
ericg had the most liked content!
About ericg
- Birthday 03/03/1978
Profile Information
-
Gender
Male
Recent Profile Visitors
The recent visitors block is disabled and is not being shown to other users.
-
Troy Molitor reacted to a post in a topic: jig stands any big benefit?
-
sandokan reacted to a post in a topic: F-80C, Lt Roy Marsh 80th FBW, Korea 1950
-
sandokan reacted to a post in a topic: F-80C, Lt Roy Marsh 80th FBW, Korea 1950
-
Paul in Napier reacted to a post in a topic: Aussie FAC in Vietnam. Cessna Bird Dog FINISHED!
-
Michael931080 reacted to a post in a topic: Aussie A-4G Skyhawk FINISHED.
-
themongoose reacted to a post in a topic: Aussie A-4G Skyhawk FINISHED.
-
themongoose reacted to a post in a topic: Aussie A-4G Skyhawk FINISHED.
-
Hartmann352 reacted to a post in a topic: Aussie A-4G Skyhawk FINISHED.
-
John1 reacted to a post in a topic: Aussie A-4G Skyhawk FINISHED.
-
Ryan reacted to a post in a topic: Scribing panel lines - corrections
-
Hi John, thanks for the input. Tom (the subject pilot) can’t recall the exact sidewinder that he carried on that day so I went with my best guess based upon some images that I had at the time. Someone put up a stack of pics of the cruise that Tom was on which featured a great pic of an A-7A from VA-82 carrying an AIM-9B, so that is the one I went with. Subsequently, I have found a picture that Tom took of a stack of A-7A’s and also F-4’s in formation, bombed up and heading out to a sortie. This picture actually has -305 in it and was the basis for my small correction on the cam demarcation at the end of the tail cone. It also has -305 carrying a sidewinder with a longer nose than the -9B so I have considered that I might have the wrong - winder on. I have also got a very good pic of an A-7A on the carrier deck, loaded with the large Bullpup, which is rare to find. The sidewinder loaded has its nose partially covered but it features the same colouring as the later models. I have used brass pins to attach the missiles to the rails so can easily change them based upon any new information that comes to light. cheers, Eric.
-
Thanks for the comments guys. Some more work. I designed and printed up a new exhaust pipe to replace the kit one. In some cases, it is easier to make a new part rather than try and clean up the kit part with all of its ejector pin holes! Using my mask cutter, I designed and cut the rest of the markings, and sprayed them on. The small Bu No. under NAVY was the smallest I was going to go. I finished off the rest of the markings with decals, using a combo of kit and Airdoc ones. Strangely, the Airdoc decals were designed for an A-7B which shares a lot in common with the A. I also painted a test shot of the Bullpup missile which I am in the process of reprinting as I detected an error in the CAD file. I also detected a small difference with the way the white cam demarcation kicks up right at the rear of the tailpipe on -305, so had to sand back the last few letters of USS America, reprime, respray the cam and then respray some of the lettering, which can be compared to the first side on shot of the model. Visible here is the yellow Fiberglass strips around the edges of the windscreen. I wasn't happy with my first attempt at them and had to sand/scrape/rub off the paint and start again.
-
Some more work. The bulkhead area around the exhaust is bare. I designed a new piece that fits into it by snapping into place after the fuselage haves have been joined. The new part installed. Really only visible if you shine a torch up there but it is still an area that needs attention in the kit. Just before I was about to start priming the model, I noticed that the tail are was a bit different on the A and B model to the E of the kit. This required cutting out the sensor, as well as the bullet shaped fairing above the exhaust as it was too long. I then designed two new pieces and printed them up. The small formation light was repositioned further forward. Finally ready for priming! it is surprising the amount of work that has gone into this model. I have test fitted the excellent Eduard AIM-9B sidewinders on the new Flying Leathernecks rails, as well as my own Bullpup missiles. Also visible is the new step that I made from Brass. I painted the model using SMS Insignia White, with Gunze Laquer grey on top. Radome was painted with SMS White and the fin was painted with Tamiya Sky Blue. Whilst probably the most plain tail art on an A-7 ever, it still required a lot of thought as to how I was going to accomplish it. Starting with the bare rudder I made up a mask using my sillhouette portrait mask cutting machine that fitted the rudder profile exactly, which then enabled me to flip it horizontally in the program to also cut the opposite side and get exact alignment. It was a sweet sound in my workshop today when I had the sounds of my 3D printer and mask cutting machine working at the same time. SMS White sprayed in two thin layers, being very careful to not build up paint on an inner edge of the mask. Done. Now onto all the other markings.
-
Over the last ten years I have travelled extensively within Australia and have also done a couple of trips across to New Zealand to attend model shows and usually take up to 6 or 7 1/32 scale aircraft with me. I pack them all in two cardboard boxes, both the maximum size allowable as carry on baggage. These boxes are filled with plastic shopping bags and the models are piled in on top of each other. I have never had an issue with breakage. Looks like the Texas show is only around 80 kilometres away from where my F-100 subject pilot lives. Hopefully travel is open by then, I would love to try and get there for it.
-
A few weeks ago, I received an email from Rob Thomson, son of my subject pilot. Whilst researching Alan, the trail went cold after the small biography that I was able to find of him and to say that I was surprised by the email is an understatement. Rob managed to track me down and got in contact. I was stoked to find out that he lived in the same city as I did, and that he had a significant amount of his fathers war time memorabilia. We arranged a meeting and I spent a few hours going through Alans log book, photo albums and various documents and artefacts. Here are some pics of the special day. Alans Log book, Distinguished Flying Cross, hat badge and cloth wings. The DFC. DFC presentation box and cigarette box. This was quite a nice piece, being handcrafted from aircraft perspex. The inscriptions were engraved on the inside of the sides of the box meaning they would have had to be done in reverse. The parts of the box were dovetailed jointed. Alans combat knife A special insert to the local RAAF produced paper `The Tarakan times' which commemorated the surrender of Japan which was signed by the pilots and ground crew. Pic of 76 Sqn pilots. Alan is 2nd from the left, top row. Alans DFC Citation One of the highlights of the day was reading this poem about the pilots day to day life in Borneo. Its pretty good.
-
ericg reacted to a post in a topic: Zoukei-mura Bf-109 & Fw-190 updates - New The Old Man blog n.113
-
Zoukei-mura Bf-109 & Fw-190 updates - New The Old Man blog n.113
ericg replied to Jan_G's topic in LSP Discussion
Well said. I am very disappointed that as soon as someone has something different to say that this person has turned it into something completely different and chosen to be offended by it. It’s why people move away from forums like this if they can’t have their say. Get over yourself. It’s not all about you. You are the only one who’s ‘feelings’ have been hurt. -
ericg reacted to a post in a topic: Zoukei-mura Bf-109 & Fw-190 updates - New The Old Man blog n.113
-
ericg reacted to a post in a topic: Zoukei-mura Bf-109 & Fw-190 updates - New The Old Man blog n.113
-
Zoukei-mura Bf-109 & Fw-190 updates - New The Old Man blog n.113
ericg replied to Jan_G's topic in LSP Discussion
Unfortunately, in today’s world you can’t say **** these days without hurting someone’s feelings, especially if it doesn’t fit within their own opinion. I probably could have stuck myself out on a limb and written a nicely worded politically correct paragraph or two being critical of ZM for their kit choice that someone wouldn’t have found to be ‘rude’ but I am sure that I still would have offended someone due to having a different opinion to them. Instead I just cut to the chase. Eric. -
Zoukei-mura Bf-109 & Fw-190 updates - New The Old Man blog n.113
ericg replied to Jan_G's topic in LSP Discussion
Calm down Chris. Not all the comments can be warm and fuzzy all of the time. There are people out there that find endless repetition of subjects boring. It doesn’t have anything to do with being critical of the choices of other people but everything to do with having a balanced opinion, something which is lacking in this forum. It is great that ZM are releasing something that will sell and hopefully make them lots of money to be able to fund research and development of esoteric subjects. On the other hand, it’s just yet another 190/109. I am halfway through building their HE-219 and am enjoying it and only hope that they choose to do more interesting stuff like that in the future. Eric. -
Zoukei-mura Bf-109 & Fw-190 updates - New The Old Man blog n.113
ericg replied to Jan_G's topic in LSP Discussion
Sorry, what kit choice did I suggest would be better? -
Zoukei-mura Bf-109 & Fw-190 updates - New The Old Man blog n.113
ericg replied to Jan_G's topic in LSP Discussion
No problems, you are more than welcome. Although it wasn’t really a comment, I was about to write one, but fell asleep before I got to it. eric. -
Zoukei-mura Bf-109 & Fw-190 updates - New The Old Man blog n.113
ericg replied to Jan_G's topic in LSP Discussion
Yawn, yawn, yawn.... zzzzzzzzzzzzzzzzz -
RAAF F/A-18 Hornet, ELTA 8222 ECM pod and adaptor.
ericg replied to ericg's topic in Works in Progress
Some more work. But first, a couple more pics of Homer. Homer led the first airstrike during Operation Falconer 2003. Here he is before departing on that day. And here he is upon return from the same mission. Its stuff like the above that really make me strive to do the best that I can on each of my subject pilot builds. Early on in the build, I realised that there was a fair bit of stuff that was on Homers Hornet during his 2016 mission that I would have to scratch build, such as the BOL dispensers as shown earlier. Another feature was the ELTA 8222 ECM pod that was standard issue for our Hornets, mounted to a unique adapter on station 6. I was ready to make these in plastic card but this was during the aquisition of my 3D printer, so one thing led to another and I ended up designing each piece. I did investigate the Wolfpack 8222 pod but was not happy with it. And here are the parts. They are almost ready to go. I am still playing with various angles of printing to get rid of some of the small visible lines and a panel line or two need to be tweaked to give them a bit more depth. Test fit to the model. Its a shame that they wont be very visible! -
Here is the test shot of the AGM-12C Bullpup that I have been working on. Still a little bit of refinement to go with how it all fits together but I am pretty happy with how it has turned out. I printed this at .02 layer height and will go down to .01 after I sort out the few small issues. Whilst it will be a shame to leave all of the rest of the pylons empty, the model will look pretty cool with two of these huge things hanging off the middle ones. After discussion with Tom, we worked out that he should have been carrying a pair of AIM-9B Sidewinders on the fuselage pylons during the mission. Screen shot of the CAD work.
-
RAAF F/A-18 Hornet, ELTA 8222 ECM pod and adaptor.
ericg replied to ericg's topic in Works in Progress
G'day Michael, Yes, the whole lot will be available for sale. Planned list is: BOL ECM dispensers (ready), ELTA 8222 ECM pod (70% done), ELTA pylon adapter (90% done), JHCMS Sensor (ready) and I will also do pre cut plastic card parts for the strengthening straps on the left side of each tail. Cheers, Eric. -
RAAF F/A-18 Hornet, ELTA 8222 ECM pod and adaptor.
ericg replied to ericg's topic in Works in Progress
I design it scaled to 1/32 in mm and then print it directly as an STL file. I guess you could probably do what you said as there is a scale function in the program.