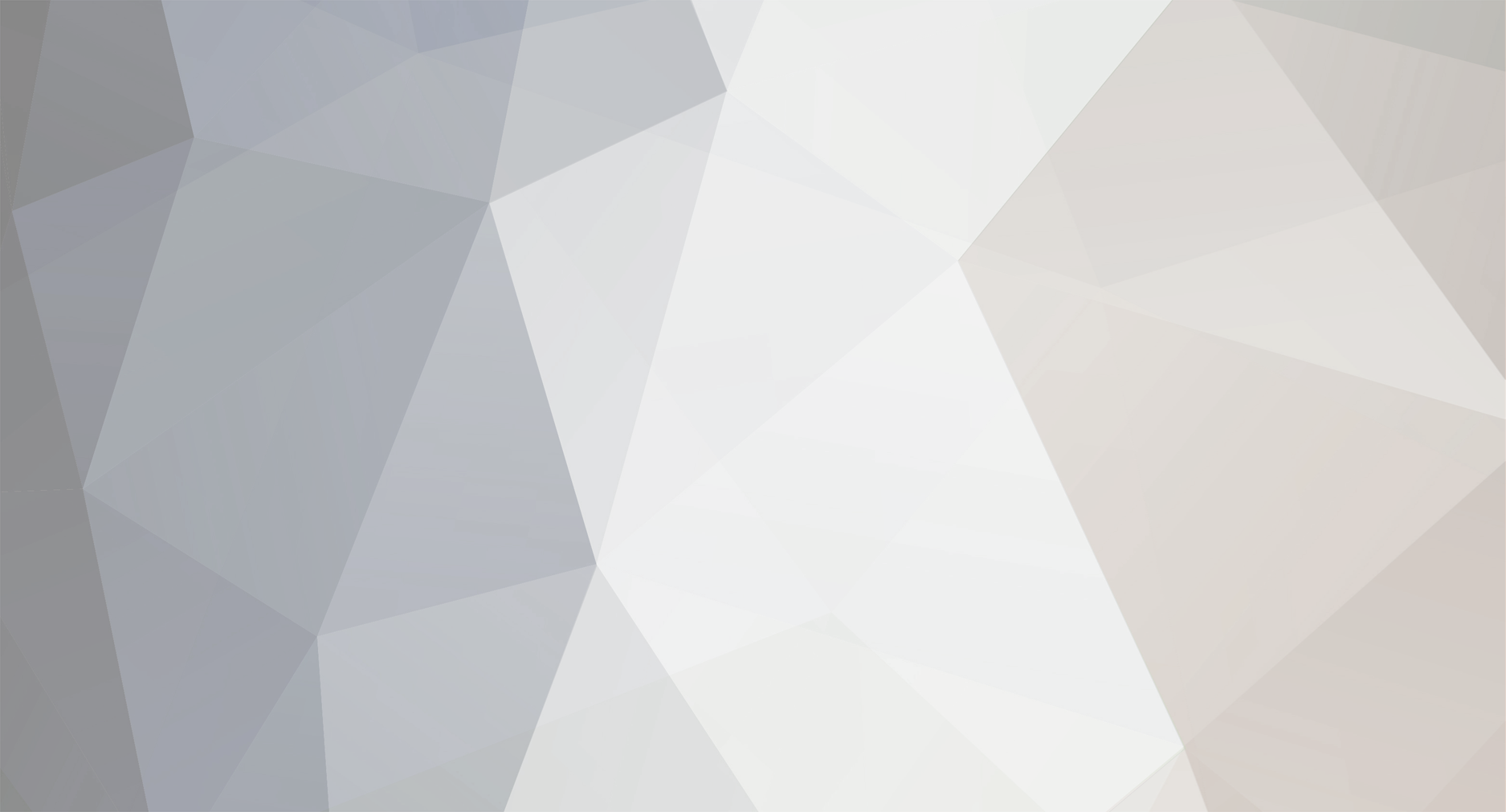
daveculp
Banned-
Posts
408 -
Joined
-
Last visited
Profile Information
-
Gender
Male
-
Location
Las Vegas, NV
-
Interests
Aircraft modeling. 3D printing. Post WW2 military aircraft, especially Cold War era.
Recent Profile Visitors
The recent visitors block is disabled and is not being shown to other users.
-
Model_Monkey reacted to a post in a topic: Strangest box cover contest, who will be the winner?
-
rafju reacted to a post in a topic: Strangest box cover contest, who will be the winner?
-
ColinR reacted to a post in a topic: Strangest box cover contest, who will be the winner?
-
chrish reacted to a post in a topic: Strangest box cover contest, who will be the winner?
-
TAG reacted to a post in a topic: Strangest box cover contest, who will be the winner?
-
daveculp reacted to a post in a topic: 2023 final year for air races at Reno
-
daveculp reacted to a post in a topic: 1/32 Revell F-4J Phantom (Blue Angel scheme)
-
GROWLER 96 reacted to a post in a topic: F11F vacuform Blue Angels
-
GROWLER 96 reacted to a post in a topic: F11F vacuform Blue Angels
-
daveculp reacted to a post in a topic: Trumpeter F4U-4 Corsair - FINISHED
-
daveculp reacted to a post in a topic: F-103, yep I am at it again.
-
daveculp reacted to a post in a topic: F-103, yep I am at it again.
-
daveculp reacted to a post in a topic: ID Models 1/48 CP-140 Aurora
-
daveculp reacted to a post in a topic: F-103, yep I am at it again.
-
daveculp reacted to a post in a topic: F-103, yep I am at it again.
-
daveculp reacted to a post in a topic: ID Models 1/48 CP-140 Aurora
-
daveculp reacted to a post in a topic: B-24D 1:32 my first large scale build
-
Rick Griewski reacted to a post in a topic: Lithophane
-
Well, that's the coolest thing I've seen in 2023, and I don't think anyone's going to top it.
-
This photo looks definitive to me: link to a photo at f-100.org https://f-100.org/pages/f-100f_63879.shtml
- 6 replies
-
- f-100d
- euro decals
-
(and 1 more)
Tagged with:
-
ICM considering OV-10A in 1/32, vote on their FB page
daveculp replied to Jan_G's topic in LSP Discussion
According to Scalemates ICM decided on 1/72 scale. Rumor is release of OV-10A kit in Q2 2023, and the OV-10D in Q4 2023. I see nothing at the ICM site to confirm this. -
Here's the evolution of a part. At far left is the main gear door part as cut out from the vacuform fuselage. I was careful to cut it out cleanly in case I decided to use it to make the door. I later decided to print the whole door, so next is a test print of the basic shape. Third is an improved version with details added, including the door actuator. Last is the final part.
- 65 replies
-
Some version of the Douglas A-3 Skywarrior in 1/32 scale. Yeah, it's huge, but the wings fold. Also, it comes in a gazillion varieties so it can be modded 'til kingdom come.
-
For those those of you looking for something else to do with your resin 3D printer here's a project you might like. Lithophanes are images which have been converted to STL format and then printed. Basically the light/dark attribute at each pixel is converted into a thickness attribute. This conversion can be done for free at several online sites. Once you have the STL you then lay it flat on the build plate in your slicer app and slice away. The result prints very quickly, about 15 minutes, since it's only a few mm thick. You may have to experiment a bit with thicknesses settings to get the right amount of translucency for the resin you're using. When back-lit the image appears like magic. You can also do this with an FDM printer, but I haven't tried that. -- Dave
-
Sorry, this isn't a progress report, but still interesting I think. The Quickboost package arrived from the Czech Republic in record time. Here's a photo of the OV-10 propellers in 1/48 and 1/32 scale. I was hoping this resin correction set will solve the long standing problem of OV-10 prop pitch. It turns out it's only a partial solution, but with a little work it can be a full solution. The blades are separate parts, which is great, but when you look closer you see the issue: Here's a photo of the 1/32 scale parts (1/48 work the same way). The blades are keyed so that they go in at only the wrong pitch. I think the best way to correct this is to file the flat spot on the blade so that it can be installed at flat pitch. I haven't done the correction yet, but I plan on being careful to not make the seat too wobbly lest the blades then sit at bad angles with respect to each other.
- 15 replies
-
- 3d printing
- ov-10 bronco
-
(and 2 more)
Tagged with:
-
I've got the nose gear printed and the left main gear. This is enough that I can turn the airplane over and check that it sits at the proper nose up attitude. It looks right.
- 65 replies
-
Finally! I see that Quickboost has made resin propellers for 1/72, 1/48 and 1/32 scale OV-10A/C. These have the blades as separate parts, so I'm hoping this means the blades can be set at any angle. If so then we finally have the solution to all kit makers providing propellers with the wrong blade angle. (Except Kitty Hawk 1/32 scale). https://www.aires.cz/en/catalog/?search=OV-10&searchButton.x=8&searchButton.y=7&category=18 -- Dave EDIT: I just ordered a 1/48 set and two 1/72 sets.
- 15 replies
-
- 3d printing
- ov-10 bronco
-
(and 2 more)
Tagged with:
-
First appearance of the term "razorback" for P-47s
daveculp replied to daveculp's topic in Aviation Discussion & Research
Good links, however the text is modern. I still haven't seen evidence for the use of these terms before the 1960's. -- Dave -
First appearance of the term "razorback" for P-47s
daveculp replied to daveculp's topic in Aviation Discussion & Research
OK, it looks like Scalemates database is 3 years off on the release date for this one. I like the price! -
I read an recent interview with a pilot of P-47's in the 1940's and he said the term "razorback" was not in use while he was flying them. This got me curious about when the term was coined, at least when used to describe the P-47. As far as I can tell the first written use of "razorback" to describe a P-47 was from the 1965 Hawk P-47D kit (number 500-100). Interestingly this was a re-boxing of the 1964 kit (number 212-200) which did NOT use the terms "razorback" or "bubble canopy". The 1964 box showed side-view drawings of both versions and the text said, "Build either version". You may rightly wonder why anyone would care when the term was coined. Glad you asked! I do a lot of genealogy work and have seen names and other "facts" about people made up decades after their decease. Sometimes it's just bad genealogy, and sometimes it's intentional re-rewriting of history. A very common example of this is applying "Sr." and "Jr." to men who never used those suffixes during their lifetimes, but it's convenient for genealogists so it gets used after the fact. Innocuous? Maybe. Ahistorical? Definitely. -- Dave
-
I do think there are trends, or fashions, in paint effects. I'm reluctant to use the term "weathering" because it seems to have no definition, and is often used to describe paint effects that are unrelated to weather. It would be nice to have a set of well defined terms for all the paint effects, but I don't think it'll ever happen. This is the internet, where people like to argue about completely unrelated subjects while pretending they're not. Dave
-
Test fitting the first iteration of a main landing gear. This first print is just to get the size and geometry right. The wheel well is in CAD, but the cutout in the fuselage is done by hand and is not in CAD. This means I'll have to make adjustments after the test fit in order to clear the fuselage skin. This might take a few tries, and the process will have to be repeated for the right side.
- 65 replies