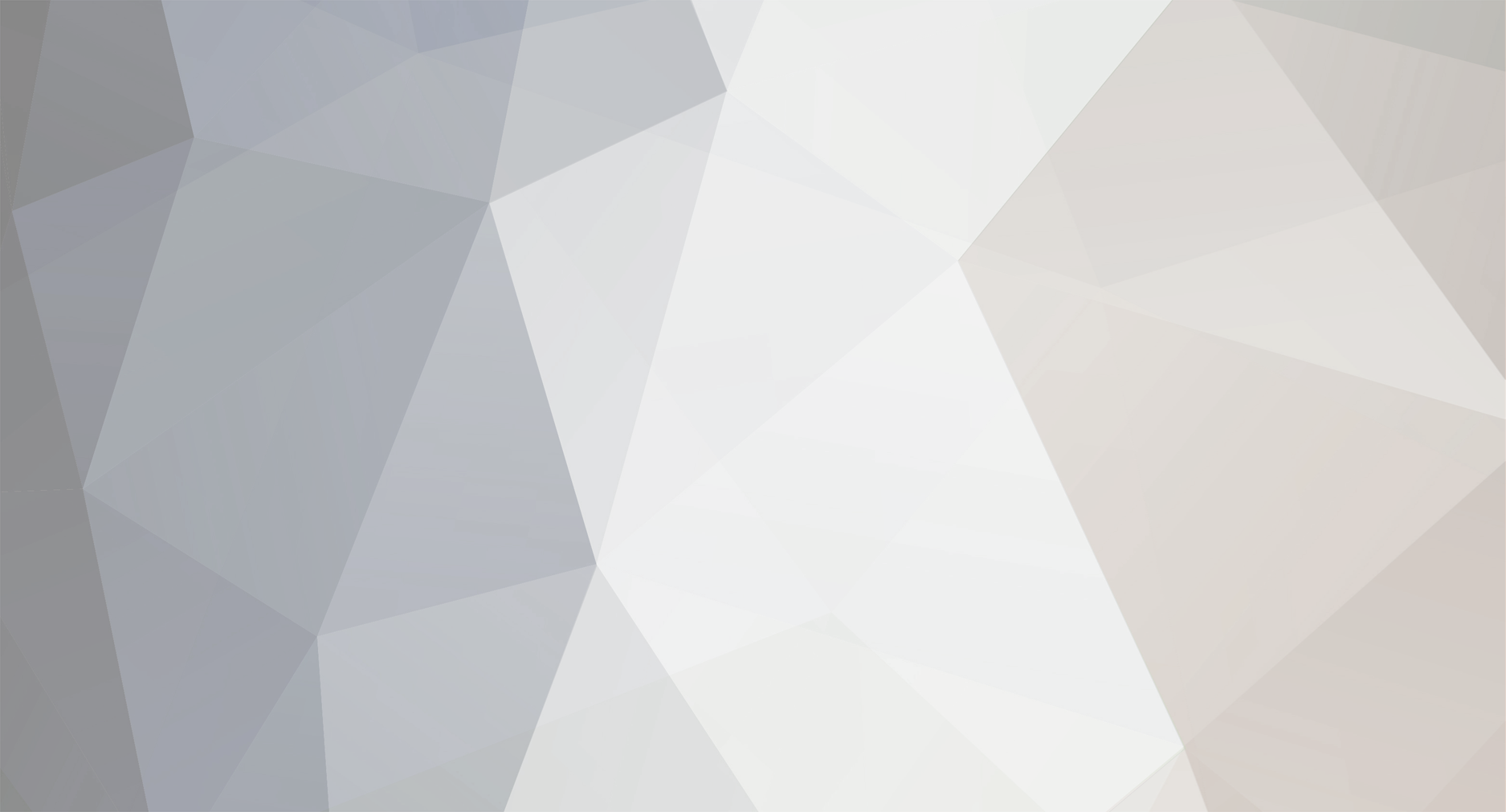
Bil
LSP_Members-
Posts
88 -
Joined
-
Last visited
-
Days Won
1
Content Type
Profiles
Forums
Events
Everything posted by Bil
-
Well.... looks pretty damned convincing to me. Exquisite workmanship.
- 1,636 replies
-
- r2800
- 1/18 scale
-
(and 4 more)
Tagged with:
-
Forget about the airplane model this is going in Jay... you should just build engines. It is a pleasure to watch your work unfold.
- 1,636 replies
-
- r2800
- 1/18 scale
-
(and 4 more)
Tagged with:
-
That engine truly is a work of art.
- 1,636 replies
-
- r2800
- 1/18 scale
-
(and 4 more)
Tagged with:
-
Beautiful work. Wow.
-
Peter, for another poster I took some detailed photos of the FW-190D (reproduction) at the local Military Aviation Museum... you can get them here: FW-190D Photos Additionally I also took photos of an original FW-190A.. as your model is kind of a hybrid, maybe they will also be helpful: FW-190A Photos Hope something in those links is helpful. Bil
-
All I can say is... wow. Simply gorgeous.
-
Thank you for this build thread, I have enjoyed every minute of it. Your final result is very easy on the eyes. Bil
-
I love the little guard for the MG to ensure the gunner doesn't shoot their rudder off. Bil
-
I love this build, its gorgeous... only one thing missing... the catapult for the display stand.
-
Unless the wings are covered with wood, like the D-VIII, I am pretty sure that rib-tapes were a mandatory safety feature for fabric covered wings. I would bet that even though they aren't prominent on photos that doesn't mean they aren't there. This is a gorgeous build so far, love the engine and the framing especially... very well done.
-
There is also Eugen Lorcher's FW-190-F8 which was mostly bare metal.. sorry couldn't find much else about it online:
-
This is incredible workmanship. Amazing really.
-
Absolutely gorgeous.
-
PZL P11 III “Cleveland” 1932 from scratch scale 1/32
Bil replied to Marcin_Matejko's topic in Works in Progress
So it has earned everything except an Oscar. Congrats! -
Lesson learned, eh?
-
Love it, a HUGE improvement over the kit part... learning to solder is on my to-do list. Bil
-
Nice work Tim.. if you turn that cowl the other way around the supports will be on the inside and it'll leave your exterior surface blemish free... the inside can be as ugly as you want, eh? As far as shrinkage with the Anycubic Photon printer.. I have not noticed that at all. in fact the parts are coming out exactly the right size, and months later there has been no shrinkage that I can notice... real thin parts can indeed warp though.. so you have to be careful of that... but once glued in position they are usually fine.
-
I made some edits to this spreadsheet... you can now enter any scale (its now a direct entry rather than a drop down menu) and I also added a calculator to help convert a plan drawing to any scale. Bil
-
Wing Dry Fit Been doing some traveling over the last few weeks so have had little time to devote to this project, but I should be off that for a while now. I printed out all of the wing parts, cut the spars out of some thin plywood and assembled some of them together to check the fit and scaling... I am having trouble with getting a usable print of the Root Rib, the gray resin version had an issue and the green version also had some flaws, I think I need to thicken up some of the components that make up this part... it is included in the images below for context, but I will be reprinting this one. Other than that all looks good now, so I can finish cleaning up the ribs, give all of the resin parts some paint and then assemble this thing. I ran out of the gray resin and had to move to another color... doesn't really matter as these parts will all be painted anyway.. but I have noticed some difference in the strength between the gray and green parts... the gray resin is stronger, but more brittle (less flexible) than the green which is a different brand. I also printed out some (near) scale turnbuckles for the rigging.. near scale because they are a few mm too long, but the actual scale turnbuckles were REALLY tiny at this scale.. these will work, though I need to do some strength tests as the eyelet neck looks awful weak to me: More images of the wing dry fit:
-
Amazing work for sure. Bil
-
I have created a Google Sheets spreadsheet to help with converting real world measurements to scale measurements in either imperial or metric units. Feedback or issues are welcome. I hope it is useful! Scale Convert Spreadsheet You can make entries in the red outlined fields, first set your scale (1/48, 1/32, 1/24, 1/18, 1/16, 1/15, or 1/12), then enter whatever your real world measurement is in the appropriate field. The Output field will contain your scale measurement in either imperial or metric units. Bil
-
Thanks fellas. I have discovered that laying a part flat as you suggest tends to make the print soft and you lose detail... maybe it has something to do with the way the resin is deposited, but if you tilt your part slightly (around 20-25 degrees) the detail is sharper and the print is overall more likely to be successful. I also never print without some sort of support. most of the time I just let the program add auto-supports, but sometimes, when I want to ensure the supports don't get in the way of the detail I will manually add them or adjust them by deleting and adding supports as required. At times I have added supports manually in my 3D program, but not often. Here is an example (from my Stearman project) showing my wing rib print tests.. one was printed flat while the other was tilted slightly.. the difference in quality and ease of clean up was night and day... though I found the tilted rib needed some supports at the top to help maintain that detail. These were printed with auto-supports added in the slicer program... The detail is clearer when printed in gray (these are 100% scale, in thickness and component part size).. this print was with supports added in my 3D program making contact at the reinforcement locations on the back side of the rib: The ribs clean up rather quickly.. there are several supports for each, along the bottom edge and along the back side... but they snip off easily and from there are rather simple to finish. I use the lightest supports for delicate parts as they leave a very small contact point. Hope that helped.
-
Love your presentation... very cool model!
-
Two Tone or Not Two Tone... That is the question...
Bil replied to Garage21's topic in General Discussion
Definitely go two-tone Andy... it would look better in my opinion. Oh and the photo is indeed of a Camel not a Pup and it is a reconstruction not an original... though I'm sure you can find examples of those online. -
Finished the base 3D wing model... I had to build it in 3D because I was finding errors in the drawings I downloaded online. I knew the exact width and the exact chord and used those measurements as my base to ensure the scale and spacing was perfect. From this I generated the plan to scale that I will use to build on: I also started to print out the components required for this build... namely the root rib, several main ribs, a few false ribs (of two types), and the tip rib. I will also be printing out the spar rigging supports and the wing tip. The spars, trailing and leading edges will all be made from wood. Impossible for me to cut these intricate ribs by hand at this scale.. so printing them in 3D ensures they are all identical and perfect, I can just throw out any that are less than perfect. These are about 3/64" thick (edges of cap strip).. so very thin, but the cap strip actually provides some strength,, more than you might think actually... the main part of the rib is about 1/64" in thickness. Sorry for the poor photo.. but the clarity on these prints is very good, the cap strips and other details are very clear and crisp.