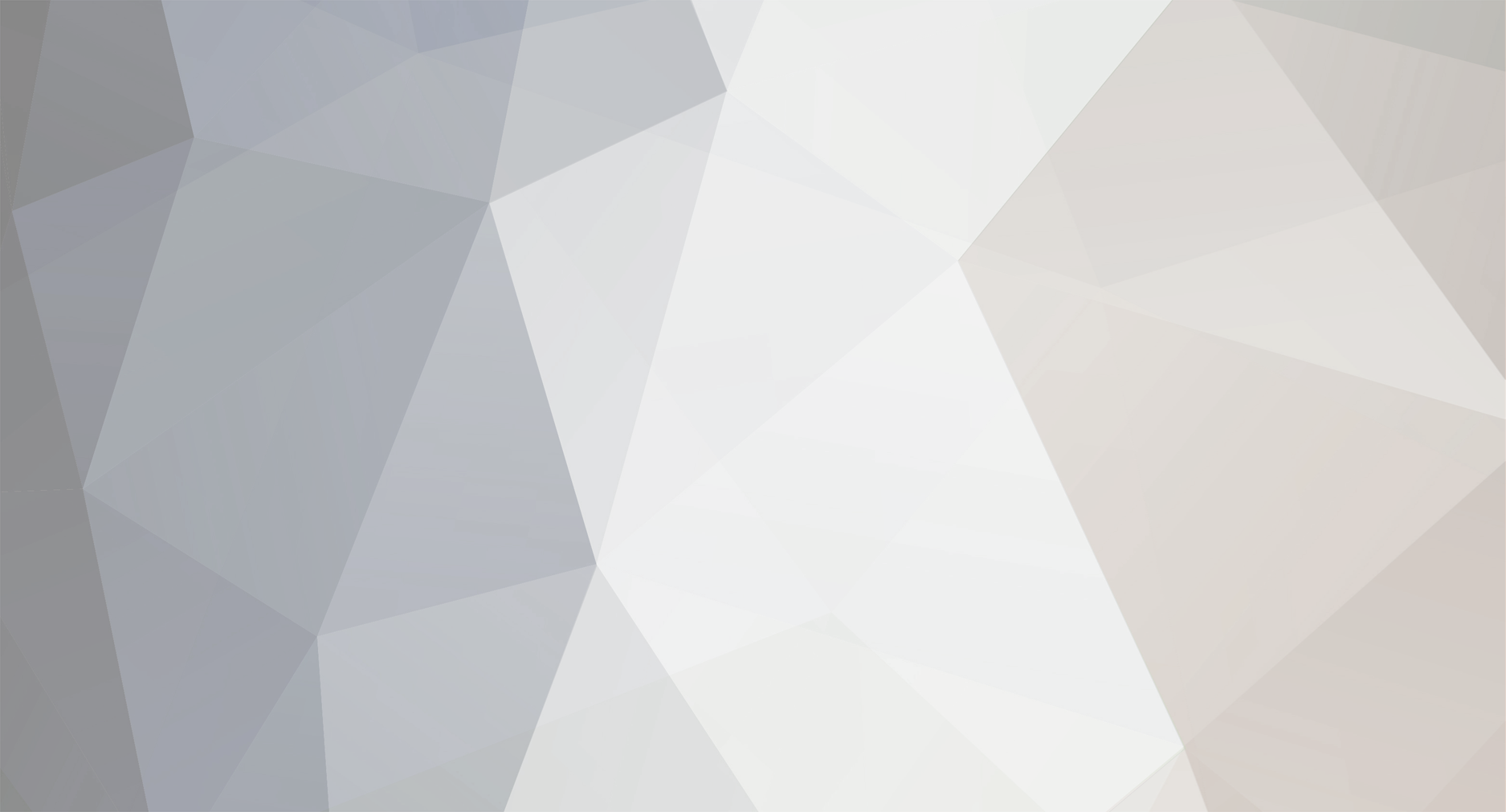
apauling
LSP_Members-
Posts
20 -
Joined
-
Last visited
About apauling
- Birthday November 1
Profile Information
-
Gender
Male
-
Location
Portland Oregon
-
Interests
fried chicken and blueberry pie
-
bstachel reacted to a post in a topic: Scratchbuild Phonix D1
-
bstachel reacted to a post in a topic: Scratchbuild Phonix D1
-
Out2gtcha reacted to a post in a topic: Scratchbuild Phonix D1
-
Starfighter reacted to a post in a topic: Scratchbuild Phonix D1
-
Starfighter reacted to a post in a topic: Scratchbuild Phonix D1
-
Gazzas reacted to a post in a topic: Scratchbuild Phonix D1
-
Gazzas reacted to a post in a topic: Scratchbuild Phonix D1
-
Alburymodeler reacted to a post in a topic: Scratchbuild Phonix D1
-
HerculesPA_2 reacted to a post in a topic: Scratchbuild Phonix D1
-
HerculesPA_2 reacted to a post in a topic: Scratchbuild Phonix D1
-
slow progress: 200 H.P. Hiero taking shape. Grey parts are Taurus resin intended for 160h.p. Mercedes.
-
David Hansen and Steve Bakke put me in touch with Jerry Robinson (an awesome and generous guy) who is retiring from the hobby. Jerry had seen a couple of my WWI builds and decided to entrust me with about 60lbs of his WWI aviation references. I want Jerry to know that I will try to make sure that his stuff gets put to good use, so I am clearing off the workbench to start a scratchbuild Phonix D.1 in 1/32nd scale. The wheels and cylinder jackets are turned on a lathe.
-
How to make propellers out of paper...
apauling replied to apauling's topic in Construction & Scratch-building
sorry to take so long to answer your question, I haven't visited in a while. When I was browsing in the store I didn't pay any attention to the weight or brand of the paper, I just grabbed what I thought would work. it was smooth and matt-finished and maybe a little heavier than children's construction paper. -
Thanks. I finished the propeller back in May: http://forum.largescaleplanes.com/index.php?showtopic=68531
-
HI Kevin, yes publish if you like.
-
I thought that the paper propeller that I scratchbuilt back in May looked a little bare, so I built a plane to stick onto the back of it. This is the Wingnutwings Roland D.VIb. I wired the engine, installed steel wire pushrods, and insulated the intake manifold with tape. I used Gaspatch guns (very nice and easier than rolling the brass cooling jackets provided in the kit). Rigging is a mix of fishing line, E-Z line elastic thread, Gaspatch turnbuckles and Bob's Buckles. Rolands had a variety of fabrics and rib tapes applied to the wings so Wingnuts provides these as individual strips of decal. It's nice to have all the options but this way you have to trim and apply about 120 decals to finish the wings! I was mostly done before I found out that Aviattic makes decals with all the options custom fit to the kit. http://www.aviattic.co.uk/132-roland-dviab.html WARNING! THE NEXT PART OF THIS POST CONTAINS ANTI-WINGNUT HERESY! I may be the first to say this about a Wingnuts kit but I can't recommend this one. When Wingnuts released the D.VIb they used their D.VIa kit and provided a different engine sprue and a sprue for engine panels and interior bulkheads. The fuselage sides are the same as in the D.VIa kit. The D.VIa had four small vents per side, the D.VIb had one small and one large vent. The D.VIb instructions have you shave off six of the eight small vents. This is not much fun because you have to be careful to avoid damaging the clinker-built effect molded into the fuselage. I noticed after my fuselage was already painted and decaled that the remaining small vents are actually in the wrong place for a D.VIb. They should be lower and further back. So, to make it really accurate you would need to make a mold of a smaller vent and then remove all eight. The D.VIa and D.VIb look nearly identical so unless you really must have one of the marking options in the D.VIb kit (or you are a masochist) build the D.VIa instead. If you have the D.VIa kit you can build an accurate model right out of the box without all the extra fuss. If I had known in May what I know now I would have built the D.VIa and put the D.VIb on Ebay.
-
I built the WNW Fokker D.VII last year and was frustrated to find that the top of fuselage wouldn't close up behind the cockpit. After discussing this with others I found that I wasn't the only one to have this problem. Now that the kit is available again I thought that I would test fit this area first (the problem is still there). The top rear corners of B10 and B11 have raised circles with a hole in the middle to accept pins from the top corners of the seat bulkhead. If you deepen the holes in the circles then cut them level with the rest of the fuselage frame the fuselage will close around the cockpit. modified parts at the top original parts at the bottom. Another thing that frustrated me with my first build of this kit was the fuel tank. After carefully painting and weathering it I found that it is completely invisible when you finish the kit. It is structurally necessary however. I found that getting the filler pipes to line up with the holes in the coaming was a fiddly experience. It might be easier to attach the filler pipes to the coaming rather than the fuel tank. The scale thickness of the landing gear makes the kit very wobbly on its wheels. The gear legs should be rigged with fishing line or wire or your kit will jiggle every time a butterfly farts.
-
A Paper Propeller Back in 2009 when Wingnutwings released their first kits I was inspired to build their LVG C.VI kit. At the time I puzzled how to re-create the multi-colored laminated wood propeller. Keeping the lamination lines straight when viewed from the side makes painting them very difficult. Eventually I decided to laminate different colored sheets of wood together and carve my own prop. This worked at recreating the lamination pattern but I was never really satisfied with this method. When viewed up close the grain pattern of the wood looks out of scale and creating the very thin pieces of wood needed involves a lot of work with the planer. (a tool that a lot of modelers probably don't have). Eight years later I have decided to try again for my build of the Wingnutwings Roland D.VI. Reasoning that a sheet of paper is like a very thin piece of veneer I decided to make my laminations out of colored paper. I got some brown and tan colored paper at the craft store and cut it into 1†by 4†strips. The paper I used took three strips to build up the thickness of one of the seven layers. 21 strips stacked up makes the full thickness of the prop in 1/32nd scale. Next I ran a bead of super glue down the center of each strip and quickly stacked them up on the pad of a wood clamp. I tightened the clamp until the layers were nicely squished together and let it cure overnight. (there is a small fire hazard with super glue and organic matter you might want to leave the clamp outside while the glue cures). I traced the kit propeller onto the top of the paper stack and drilled a hole for the propeller shaft. Next I cut along the outline with a scroll saw.http: Next I carved the taper into the blank. The stack of paper will carve a lot like wood so cut from the hub toward the tip. Think about the pressure of the tool pushing the layers together as you cut. After you have the taper established, carve the twist into the blades. If the paper starts to shred, switch blades or use a little thin super glue to solidify the area you are working on. The paper can be filed and sanded like wood but pay attention to the grain so that you don't pull the laminations apart or tear out chunks of paper between the glue lines. I sealed the prop with Tamiya clear tinted with a little clear orange. top: a basswood prop I made back in 2009 bottom: a new paper propeller
-
Sure Kevin, Thanks!
-
Thanks, to answer your question the aircraft had a wooden prop sheathed in aluminum foil.
-
Hello This is my Wingnuts Fokker DVII. I decided to build it in American colors and install an American engine. I used parts from the Wingnuts Liberty V-12 accessory sprue and scratch built a new crankcase and manifolds to make a Liberty-six engine. I started this back in the fall of 2014 and have returned it to the box many times. Finally done. The national markings are Yellow Wings decals. The rudder stripes are painted and lettered with Microscale decals and Woodland Scenics dry transfers. Thanks to David Hansen for his advice on mixing insignia blue with Tamiya paints. ( I found an 8 to 1 mix of royal blue and black to match the Yellow Wings insignia blue although 9 to 1 looks better to my eye) I found this kit to be more difficult to build than other Wingnut kits. Wingnuts' faithful reproduction of the Fokker's steel tube construction makes the forward fuselage frame very fiddly and delicate. The fuselage did not want to close around the rear cockpit frame. This may be my fault but I don't know where I could have gone wrong. For those who plan on building one of these, don't spend a lot of time on the fuel tank, you will never see it again (but it is structurally necessary). Also, the landing gear is very wobbly, you will need to rig it with fishing line to give the structure some strength.
-
Thanks guys, Hey David, After seeing how much you add to 72nd and 48th corsairs I'm curious to see how much you add to the Tamiya corsair. I don't know enough about Corsairs to tell if the Tamiya kit has all the lights, drainpipes, springs, and widgets of the real deal to keep you happy. I did notice that there were no cowl flap actuators, I don't know if I would bother building something that only someone with a flashlight could find.
-
Here is my start for this group build: I just have to carve away anything that doesn't look like an airplane.
-
here is my start for the group build: I've heard bad things about the fit of the engine and nose of this kit. So far the rumors seem to be true. The instructions don't make it obvious that not all the fuselage formers are perpendicular to the engine bearers. Most of the formers fit in front of the alignment tabs on the fuselage, but the last one can only fit behind its tabs. From my test fits it looks like the fuselage former / engine bearer assembly is too narrow and that if you follow the instructions the nose will be too pinched at the top to get the upper fuselage on. My solution was to cut all the formers in half and glue them to the fuselage sides. The gaps in the formers will be directly underneath the oil pan, so I won't bother fixing them.
-
Nice job on the DH-2! I like how you made the replacement wing a slightly different color. I think you have the aileron position correct. I've seen pictures of DH-2s with just a little droop on both sides, yours matches the pictures. Maybe that was how they trimmed the aircraft?