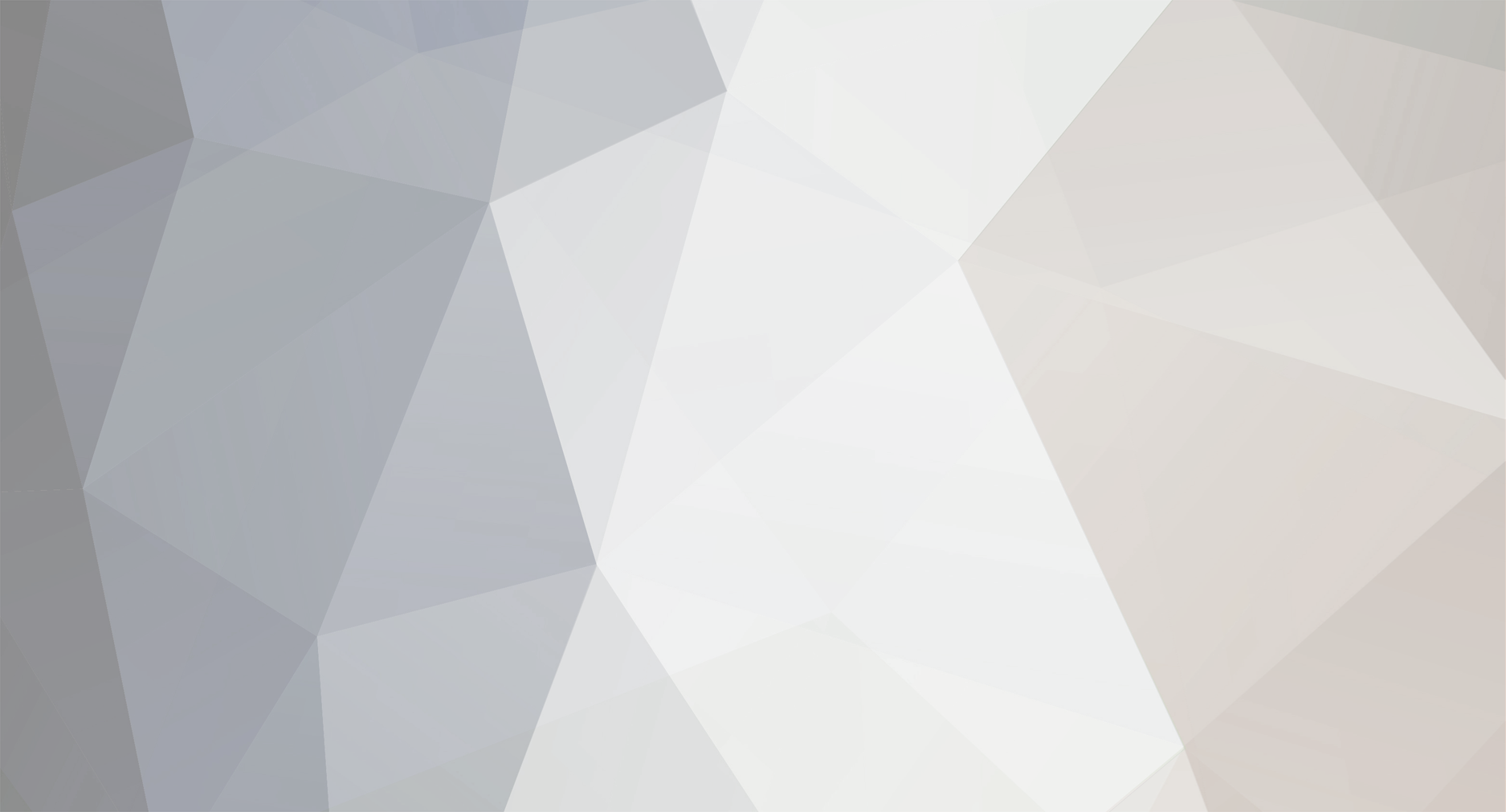
Mustang JBB
LSP_Members-
Posts
103 -
Joined
-
Last visited
Profile Information
-
Gender
Male
-
Location
San Antonio, Texas
-
Interests
All aircraft, but most WW2 Allied.
Recent Profile Visitors
The recent visitors block is disabled and is not being shown to other users.
-
I just bought the Fly 1/33 paper model, vac canopies, and laser cut frames about 2 months ago. Been on the fence with that one for a while. Of course when I finally break down and order the stuff, this happens. At least I haven't started the paper model yet.
-
alanash1963 reacted to a post in a topic: New HKM 1/32 Ju-52?? Is this real???
-
Dany Boy reacted to a post in a topic: New HKM 1/32 Ju-52?? Is this real???
-
https://www.scalemates.com/kits/hk-models-01e033-junkers-ju-52-3m--1295296?fbclid=IwAR0io5ZXMFiHEqQhM2LFtqgvnyH_LwjIACSE0zj5fSEhEIK88xTOVjq7t-g
-
Out2gtcha reacted to a post in a topic: Black CA glue
-
I also use it for gap filling, because it is easy ti see against the light colored plastics of most models. I agree that it is a little bit softer, and can be a little crumbly when tried to scribe through if you wait for maximum hardening. Sanding and scribing within a few minutes of initial hardening is the best way to avoid this. It does appear to take a bit longer to harden that standard CA, meaning 1 minute instead of two. Even if using accelerator. The black makes it very easy to see if you have properly feathered the edges and judge if you have filled all you need. It also makes it much easier to see if you have sanded all of the CA applied. As you sand, it runs from a shiny black to a rough finish to makes it easy to see the difference. I also use Bob Smith Industries Rubber-toughened CA glue, as that is what my hobby shop has. there is a guitar repair supply site on the web that sells various colored CA's that have no rubber in them. They are pricey though. https://www.stewmac.com/Materials_and_Supplies/Glues_and_Adhesives/Glues/StewMac_Super_Glues/StewMac_Tinted_Super_Glue.html
-
LSP_K2 reacted to a post in a topic: Article on Lou IV colors...
-
Alburymodeler reacted to a post in a topic: 1:32 Douglas A-26 Invader from Trumpeter/Hobbyboss?
-
John1 reacted to a post in a topic: 1:32 Douglas A-26 Invader from Trumpeter/Hobbyboss?
-
1:32 Douglas A-26 Invader from Trumpeter/Hobbyboss?
Mustang JBB replied to Iain's topic in LSP Discussion
Man... this is disappointing. I was really hoping for a reasonably good kit. but the problems keep popping out. Has anyone mentioned the wing fillet? Very 90 degree and sharp, whereas the real plane has a nice rounded and smooth fillet. The P-61 had a few errors, but was not a bad kit overall. The issues on that one are all easily fixable. This one is just bad. I hope they fix the issues, but not holding my breath. I was really looking forward to the B-24, but that wing profile is unforgivable. -
Article on Lou IV colors...
Mustang JBB replied to Mustang JBB's topic in Aviation Discussion & Research
That is the one! Thanks amigo. -
Jan_G reacted to a post in a topic: Article on Lou IV colors...
-
About two years ago, someone did a great post on the blue green mixed colors of the P-51, Lou IV. Could someone please post a link to that article.
-
1:32 Douglas A-26 Invader from Trumpeter/Hobbyboss?
Mustang JBB replied to Iain's topic in LSP Discussion
That is why I was thinking it was a scam as I could not find the picture on any of the Trumpeter FB pages. Plus, the picture just looks a little too set up. The tires depicted on the front computer screen look like truck type tires, and the Invader models are very square to the desks, parallel with the edges etc. The rear computer screen has some kind of object on it, but nothing I can see as definitively "Invader". The two models are almost perfectly pointed right at each other. The other models in the room are all Tanks as well. Are these the armor guys? Why do they have a 1/32 airplane on the desk? Not sure what the open box is on the first desk. Tanker truck? Submarine? What ever it is, it does not look like Invader parts. Nothing else in the room says "Invader" to me except the two perfectly placed models on the desks. Though I am no expert analyst by any means. It just doesn't "look" right. But I sure do hope I am wrong, because I will be the first in line to buy one. or three. -
Out2gtcha reacted to a post in a topic: 1:32 Douglas A-26 Invader from Trumpeter/Hobbyboss?
-
1:32 Douglas A-26 Invader from Trumpeter/Hobbyboss?
Mustang JBB replied to Iain's topic in LSP Discussion
I hope it is real, I would love an Invader, but something tells me this is a hoax. Crossing my fingers though! -
Mustang JBB reacted to a post in a topic: Bachem Ba 349A-1 'Natter' in 1/18th and 1/16th scale
-
David66 reacted to a post in a topic: 1/24 F6F Build page on Facebook
-
David66 reacted to a post in a topic: 1/24 F6F Build page on Facebook
-
I guess that is a good question. I guess I will start a thread and see what happens. There are some aspects of FB that make sharing photos links quicker and easier though.
-
My FB page will draw content and users from all over the web. I have posted links to several LSP forum threads already about the 1/24 F6F. Lots of the people on my FB not did not know LSP(or LSM, Hyperscale, Nigel's Modelling Bench, and certain after market companies etc) existed before those posted links. So I am sending the love back this way as well, and promoting the hobby in general.
-
No offense taken. I do not have a build going right now, just collecting data, assembly tricks, and reference material, and asking the rest of the planet to join in and help each other out. The Facebook format has some advantages over forums and vice versa. I will be watching all of the builds here and on other forums as well. A lot of people are on FB and not the forums. Some people don't even know about this forum. I am using FB to link people to this forum and the various threads here, along with linking them to other forums, manufacturer pages, reference photos and web pages etc. LSP is great, but it is not a one stop shop, nor is FB. FB is just another avenue to get more info to me and others. I have 12 different knives on my hobby table. They all cut, but they all cut just a little different that the other. Someone commented above that they did not like the FB format. If you build a FB page or group, you have access to tools to change the format, pin certain threads and posts, and tag threads so they appear under certain classification buttons, like "after market", "tools", "paints" etc. Just like we tag threads here. All it takes is a few minutes to figure it all out. By the way... LSP has a FB page.
-
https://www.facebook.com/search/top/?q=1%2F24 airfix hawker typhoon mk.ib builds&epa=SEARCH_BOX
-
https://www.facebook.com/search/top/?q=1%2F24 airfix hawker typhoon mk.ib builds&epa=SEAR CH_BOX
-
I am a member of a Face book page that is dedicated to the 1/24 Airfix Typhoon kits. We share build pictures, advice, and reference material useful for a successful build of that specific kit. Since it has proved very beneficial, I decided to create a group just for the new 1/24 F6F Hellcat kit. If you intend to build the kit, consider joining the page and sharing what you can, or seeing what others have to say. I have posted a few starter links to build videos and aftermarket suppliers. https://www.facebook.com/groups/359388731442410/
-
I know it is supposed to be out in May, but any ideas as to what part of May? Is Airfix been good about releasing on schedule?