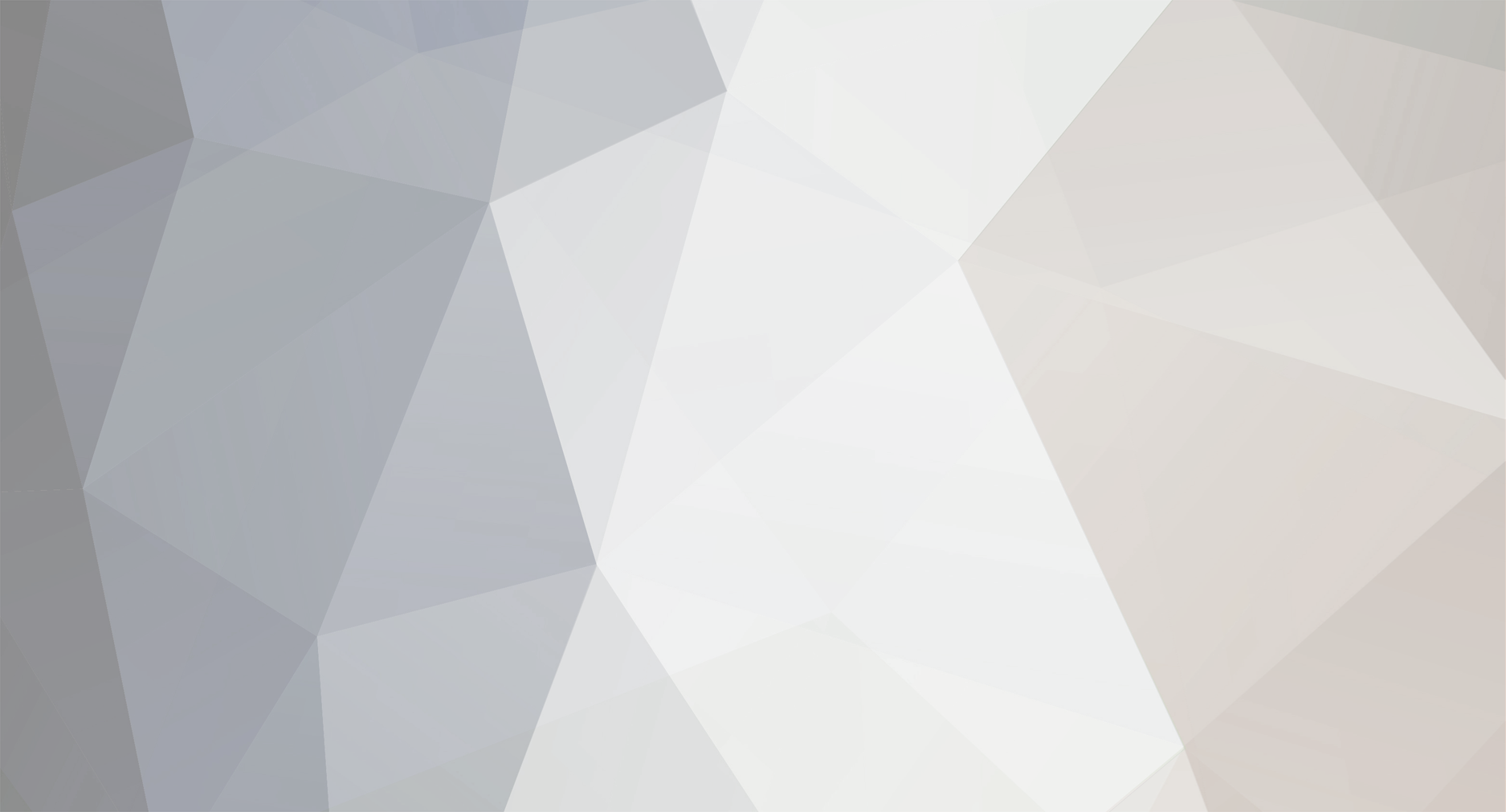
JayW
LSP_Members-
Posts
2,316 -
Joined
-
Last visited
-
Days Won
26
Content Type
Profiles
Forums
Events
Everything posted by JayW
-
Well now I stand corrected. And yes that would make for a nice paint scheme.
-
I have learned in the process of designing and building a 1/18 scale P-51B with Malcolm hood that the Malcolm hood modification was no simple thing. Quite involved. I wonder if Eduard would be doing a standard greenhouse canopy B/C or the Malcolm hood mod. Or both? If so I hope they did their homework. And, if they were to include a RAF paint scheme - then that would force them to offer the Malcolm hood.
-
1/18 Hawker Sea Fury - VX628 - 1831 Squadron RNVR
JayW replied to airscale's topic in Works in Progress
Dammit Peter - you just keep raising the bar. This is a monster - where are you going to put it? -
1/18 Hawker Sea Fury - VX628 - 1831 Squadron RNVR
JayW replied to airscale's topic in Works in Progress
Wow Peter - can hardly believe my eyes. Do you have an electron scanning microscope to assist with your detailing? -
Good god man!! Looks like you topped out the Anycubic! How many hours did that take?? And, how many hours of design time?? I'd better get a move on with my 3DP P-51.....
-
1/24 Spitfire Mk IXc, Kicked Up A Notch, July 6/25. On hold for now.
JayW replied to chuck540z3's topic in Works in Progress
Of course I want to tag along for the ride. Following. Good start Chuck. -
Wow - and you must have a pretty big printer. How big?
-
Beautiful photo-etch work John!
-
1/18 Hawker Sea Fury - VX628 - 1831 Squadron RNVR
JayW replied to airscale's topic in Works in Progress
Oh man can I relate - I was indeed $hitting myself as I went through the several day process of painting the big Corsair. And I hated every minute of it. I have to ask - what problems did you encounter. Did the tamiya x-22 work out OK for you? Any paint lifting? And Peter - that monster looks awesome! -
Thank you Juggernaut and Antonio. And as usual, Antonio backs up his responses with extensive photo documentation! This is an oft repeated subject of discussion I know. I want to describe for you some good points about aerodynamic drag that I learned during my years at the big airplane company. For wings, surface smoothness is more important on the upper surface than the lower surface. What we are looking for is delay of the onset of flow separation. Flow separation = loss of lift and high drag = the enemy. And it is the upper surface where flow separation occurs (negative pressure on higher curvature). Also, a smooth surface is more important on the front part of a wing than the aft part. Even with a smooth surface, a boundary layer builds up as air flow travels aft. Inside this boundary layer, air flow isn't really a flow at all; it is air molecules more or less "stuck" to the surface. This boundary layer becomes thicker the further aft you go. So, a closely manicured smooth surface is more important on the leading edge than the trailing edge. There are three kinds of panel joints - a butt join, a forward facing lap join, and an aft facing lap join. The kiss of death for flow separation is the aft facing lap join; by its very nature it causes a flow separation. Second worst is the forward facing lap join, and the best is the butt join. But even a raw butt join gives a surface discontinuity that can result in flow separation and drag especially when the wing is working hard, like a tight turn with high g's, or a slow approach at high angle of attack. All of this can explain the requirement of smoothing putty over the forward 40% of the P-51 wing - a wing BTW with its max chord height further aft than most wings of that day (the "laminar flow" wing) making it more sensitive to flow separation, but as long as you avoided that flow separation (e.g. maintained laminar flow) you got more speed than your adversary. A smoother surface helped avoid that flow separation and minimized the boundary layer effect. More on panel lines - joints that are perpedicular to flow direction are the worst. Of course. Joints parallel with flow direction have the least effect on drag and flow separation. That could explain why it was less important to address that wing tip join. Let me summarize what I think I heard. Smoothing putty of some sort is applied to the wing from the leading edge back to 40% chord, 40% being a line not far aft of the front spar, and easy for me to determine. In this zone, as far as the modeler is concerned, there ought not be any exposed panel edge joints or evidence of fasteners. With some exceptions however. The leading edge access panel directly in front of the landing gear trunnnion is, for some reason, not included. Why? Who knows. Also, it appears the panel that includes the landing light is not included. Why? Who knows. These two items, along with the gear doors and lower fuel tank access panels and trailing edge devises (flaps and ailerons), on my model would be NMF, with flush rivet heads represented. The entire wing (not just the forward 40%), except the items listed above, is painted with silver paint. However, from 40% aft I think I should represent fastener heads. That is what I think I am going to do. Y'all good with this?
-
Hi folks - ya keeping up? Last we visited the pilot's seat was some three months ago. At that time Antonio had presented me with a stunning digital rendition of that first aid kit on early P-51's which served as a head rest. Saving me from having to sculpt out one of my own and doing a lousy job of it. So I asked Antonio if by chance he also had a back cushion defined - he didn't but in about a day he had produced one! He sent it to me in STL format, I tweaked it a little, printed it off, painted, dirtied up, and voila: Is that cool, or what? But why is it that ugly yellow Jay? Because - that is the way it was! My guess is that it served as a flotation devise and needed to be easily seen. ??? Anyway, thanks again Antonio - you're the greatest. So once again I dodged the need to break out the milliput and sculpt. Now for seat belts and shoulder harness. Peter (Airscale) scaled up to 1/18 a set of his 1/32 photo etch buckles and other hardware, and sent me a set along with some lead foil. Many thanks Peter. So I quit my dawdling and delaying and got to work on it. Not my favorite modeling sub-project. Here we go: First, while wrestling with the seat assembly preparing it for belt attach, I first fractured a side brace and fixed it with CA. No biggie. But then, I dropped the seat, it fell in my lap where I instinctively closed my legs on it to avoid it falling to the floor, and broke one of the support tubes: And it fell to the floor anyway. Yes, a momentary seizure. Ordinarily a disaster. But folks on this site show me time and again that disasters are merely opportunities to flex one's modeling muscles. So I put aside my feelings of panic and despair and got to work with the fix. I won't show it, but it worked fine. Man - this P-51 is full of fixes.....that's 3D printing for you. So here is the finished product, ready for installation into the cockpit: I guess it's OK. I think Antonio's seat back cushion is the star of the show. Glue that jewel into the long-awaiting fuselage: Yay!!! Note the throttle lever has been fixed too. Dry fit the windshield and IP and it's done: A P-51B man, with WM seat. Note in that last picture the aft half of the Malcolm hood roller bar has departed the airplane. Fixed that too. All right - what to do next. Wing work. So now is the time for a bit of discussion on wing paint. When one pulls up the exterior markings drawing 102-00010 for P-51B/C, there is a note: OK, so I go to drawing 102-00024, and I find this among very many other instructions: OK - that "airfoil smoother" is a thin putty of some sort which is supposed to fill in panel butt joins and also smooth flush fastener heads. I think all Mustang enthusiasts know that. What about that "leading edge to 40% chord"? I do not know where I could find "process manual P-6" but I'll bet it describes the application of silver paint over the smoother. Does the paint end at 40% chord? No, I don't think so. I believe that with a few exceptions, the entire wing top and bottom is painted with this silver paint. Not just to 40% chord. Seems like this picture is definitive: Where the lighter of gray is silver paint. This is for the D-model, but I understand the B/C was the same. Note that absent from the silver paint are the following: Gear doors flaps and ailerons the lower fuel tank access covers (the ones I just finished) Those items are NMF, or OD, or gray, or black/white invasion stripes. If any of you have a better definition, I'd like to see it. Then comes the question about what the aircraft came with fresh from the manufacturer versus how it held up after fighting a war for a while in all kinds of weather and other tough conditions like flying debris from exploding locomotives or enemy aircraft. I think, unless I get strong arguments from a follower or two, I am going to go with silver paint per the picture above. Plain and simple. How does that affect my wing skinning? Why do I skin a wing or a fuselage in the first place? Two reasons - to accurately depict a natural metal finish, and to accurately depict fastener head marks. A secondary reason is to make for convincing chipping for weathering. In the case of a silver painted wing that has been smoothed over so that there are no fastener head marks, then why skin that part of the wing at all? Methinks I will do this - already I have most of the inspar skin panels done, and they are designed to accept .005 inch thick skins (they are under contour that amount). So I will skin the remainer of the inspar wings in aluminum but with no awl punch fastener marks. That leaves the leading edge skins - I think I will just design them to be on contour as printed, with no fastener marks. No skinning in aluminum. Much easier, and historically accurate. Am accepting any comments on this plan; but hurry, I am off and running with my plan! A good amount of time is now going to be taken Rhino designing the landing gear bays, with skins on contour, not under. You will see some of that work next. It is about as highly anticipated (by me) a thing as anything else on this project. Stoked to the max. Will report out when I get something good.
-
Use a mule.
-
Yes, perhaps another time. I should have thought of that! However, think how small they would be. Just barely larger than the support sprue that they attach to while being printed. You have not seen it yet, but I printed up two versions of the landing gear torque links - one with integral lube fittings and one without (the lube fittings were printed separately). Those separate lube fittings ("zerk" fittings), are really tiny, probably similar in size to the screw heads (and presumably a shank) you suggest. I can tell you dealing with such small parts is infuriating. Any little thing makes them disappear. High magnification glasses are a must first off. Fine. Then snipping them off their supports, unless done with exceeding care, causes a part to dart into a parallel universe before your very eyes. First its there, then it isn't. Similarly, if a part has survived being separated from its support, it probably needs a bit of trimming. That borders on the impossible - again the part will likely disappear. And a part that survives that step is subject to the modelers own breathing - an errant sigh or god help you a well directed cough, and the part (or parts) are suddenly gone. And then to top it off - there is the delicate task of placing the part in position for installation, another golden opportunity for disappearance. I could tolerate such frustration for a few parts - but hundreds? Anyway - I abandoned the separate zerk fittings idea! It occurred to me the frustration mechanics in the field must have felt extracting hundreds of screws to remove that cover panel, and then reversing the process. I wonder back then if they had pneumatic drills..... Actually this wasn't that bad. I started with little awl punch depressions for drill starts using templates given to me by Peter Castle, which gave a good even fastener pitch on a straight line. That made the hole drilling easy enough. For the plug punching, I did ten at a time to keep my sanity. The plugs fit in the holes just about to perfection - carefully place one on the hole with a dampened tooth pick, and push down with a fingernail, and usually the plug slid in the hole with a slight press fit such that it stayed there. Usually, but not always. Similar to what I describe above, some plugs would instantly transfer into an alternate universe. A tiny tiddly wink. Poof! Anyway do that ten times, bathe with thin CA, wipe off, and repeat. Well now - you are right. I looked on E-bay and they are everywhere. Not cheap, but everywhere. I might have to give that a go, although that approach only works well on round heads. Most but not all protruding fastener heads are round. Thanks for that suggestion!
-
Tamiya F-16 "Ghost" Aggressor, Kicked Up a Notch
JayW replied to chuck540z3's topic in Ready for Inspection
This looks like a show winner Chuck. Congratulations. It is a sight to behold. -
Tamiya F-16 Aggressor, Kicked Up a Notch- KLP Shout Out
JayW replied to chuck540z3's topic in Works in Progress
Chuck - one, I am glad to hear you are on the mend. Yay! Two - what a butt kicking F-16!!!!! It turned out great. Three - I cannot wait to watch your 1/24 Spit build. -
I would be surprised if Tamiya didn't do exactly that. They already have that superb D-model - it is probably the definitive 1/32 Mustang kit. It would not be a big stretch to do a B/C. No I cannot say I have. Nor have I considered putting a pilot in the cockpit. Nor a diorama. I am just interested in the aircraft itself, as it could have been when it existed. I will dedicate this post to one set of wing skin panels, or better - wing fuel tank covers. NAA engineering drawing 102-14060. And I will dive into it some, at the risk of boring some of my followers. I hope not though. The P-51 had 90+ gallon rubber self sealing fuel tanks inside its wings, one LH and one RH: As can be seen in the RH picture a lower surface access cover can be removed to get to that tank (it is shown being installed). The tank fits between the front and rear wing spars, and spans from the airplane centerline out to the major wing rib at wing station 75. It is a big tank with a big access cover. And it is held in place by about 130 1/4 inch diameter button head screws. Not flush head, but protruding button head screws: From the panel installion drawing, the specified screw part number is 7S2-428 series. Here is the spec for the screw: Some of you knew this already. Here is a shot of a real aircraft showing some of those protruding head screws: The P-51 wing, like all good aerodynamic wings, is built up using flush head fasteners, almost entirely, to reduce drag. And the P-51 goes further - most of its wing has filler type silver paint which covers the flush fastener heads and skin joints, to further reduce aero drag. So why do we see hundreds of drag-inducing protruding head fasteners for the wing tank cover panel? First we could ask why 1/4 inch screws? Pretty capable - wouldn't 3/16 screws be OK? I cannot answer that one. One 1/4 inch 125 KSI steel screw is good for approximately 4000 lbs tension ultimate load on its own. 130 of them is good for 520,000 lbs ultimate load (4000 times 130). 3/16 screws are just over half as strong as 1/4's in tension. So the same amount of screws would be good for about 260,000 lbs, a bit more actually. So much for capability - what is the actual load? Likely, the max load on those screws is a full tank undergoing max g's. A full tank with 6 lb per gallon avgas weighs something like 600 lb all told. At 6 g's that is 3600 lbs limit load. Multiply by 1.5 for ultimate load and that is 5400 lbs. 5400 versus 520,000. Not even in the same ball park. But wait - the basic gage of the cover panel is .08 inch. The countersink depth for a flush head 1/4 inch screw is more like .12 inch. So the countersink will "knife-edge" the panel, wiping out the basic 1/4 inch hole. Even a 3/16 inch countersink will, but to a lesser extent. This would greatly reduce the ultimate capability of the joint - you would get a pull-through at far less load than the tension capability of the screw itself. All that to say NAA chose to eat the drag and use protruding head screws in good holes to attach the lower fuel cell cover panel, for whatever reason. So be it. How to model it? Some of the other modelers on LSP, who are scratch building using aluminum skinning, reverse the direction of the skin when awl-punching rivet marks, and do this using the softer annealed skin material. This pooches out the material locally and approaches the look of a protruding head fastener. I was going to do this, but I would prefer a more realistic look if I can. So I tried using drilled holes and little punched pieces of plastic inserted into the holes, and I think it worked better. Here is one of the cover panels laid out and undergoing prep: A finished panel detail: The important detail here is the array of .028 inch diameter holes (about 100 of them) along three sides of this panel (one side is covered by the centerline bolt cover, so no holes required). How did I get .028 inch diameter? Look at the 7S2 spec above for 1/4 inch screw head diameter (column "A"). It is .49 to .51 inch (or .50 nominal). For 1/18 scale, that works out to be .028 inch. I have a .028 inch diameter drill bit, so I drilled all those holes in addition to the all the hundreds of awl punches to simulate rivet heads, and the tricky cutout for the access door. I also have an awl punch set that allows for a .70 mm punch. .7 mm = .0273 inch. That ought to fit pretty nicely into a .028 diameter hole. And it does. How thick material should I use? Per the 7S2 spec the head height for a 1/4 inch screw (column "B") is .115 inch to .127 inch (or .121 inch nominal). For 1/18 scale that works out to be .007 inch. But remember, I will be sinking the plug into the aluminum skin, which is .006 inch thick. So total thickness of the plug should be .007 + .006 = .013 inch. I have plenty of evergreen .015 inch sheet - good enough! So I was off to the races: Many many little .7 mm dia by .015 inch thick wafers, to simulate screw heads. And yes - very very tedious. Not a perfect simulation, but I think pretty good. BTW - the .7 mm hole in my rptoolz die is well worn now.... A cover panel bonded to the wing, and plugs being inserted and bonded into holes: Fiinished product: I managed to mislocate one of the access doors relative to the other somehow, by a little as can be seen. But it's going to be OK - they are largely covered by the radiator inlet fairing. Those were interesting panels. I am happy enough with the protruding heads. The panels will be largely painted with invasion stripes, some day. Next on the docket is the pilot's seat and the addition of seat belts, shoulder harness, and back pad. I have all the parts and materials; just gotta do it. Will update soon! Thanks for looking in and putting up with an exhaustive description of just one set of wing panels.
-
Hello ladies and gentlemen - I am currently doing three subprojects in parallel, a mistake. It gets to be too much and I get anxious. They are as follows: Wing box skin panel skinning Main landing gear (MLG) upper struts Pilot's seat cushion, shoulder harness, seat belts I will report on the MLG upper struts; next post or two will be on the others. I got to work on the upper struts just to take a break from the endless rivet punching on the wing box lower inboard skin panels. Next post you should see those, and I think we will have the mandatory discussion on P-51 wing skin painting, exactly where, and if that means some rivet punching is no longer necessary. But not right now. The upper struts turned into little "tar babies" - they involved soooo much micro-surgery - the struts themselves (3D printed), the internal strengthening of the struts, torque link design, brake line routing, decals, and a maddening little rube-goldberg gizmo called a safety lock system, not present on the D-model, but present on -A's, -B's, -C's (LH side only). Oh, and a delicate yet successful repair of a broken torque link lug - breaking off that lug really set my hair on fire! All in all, I got pretty frustrated with it, to be honest. Internal strengthening - already, as you know, I have seen to the lower struts. They now have internal metal rods, that were tested to see how they hold up under load. A-OK. I felt the upper struts were going to need some strengthening also. So I got to work designing some internal metallic components for them. Here is an exploded view from Rhino: Essentially the 3D printed upper strut, which has an integral elbow, or better called a trunnion, is lined with aluminum tube and a .093 rod that runs inside that trunnion. All swimming in 2-part epoxy. It's gonna work believe me. Here are the finished products: Took FOREVER!!! Stiff little buggers. You see lugs for torque links, lugs for door attach, brake lines with large diameter clamps, and that safety lock gizmo on the right crowding the torque link lugs. You also see decals. The big black one (the vendor decal - for Bendix) I made myself - my first try at laser jet decals. The red one is from Peter Castle's Lopes Hope set. Here I have dry fit some MLG components together for your viewing pleasure: The assemblies lack the torque links, which I have but are not ready for prime time. They must sit around for quite a while - I am not ready to join the lower and upper struts. See that YZC fitting in the background? That is one of two Station 75 leading edge ribs, which serve as the landing gear supports: I am very very proud of those 3D printed parts, and they printed up better than expected. It was a major effort to design them in Rhino, and they closely resemble the actual heavy fittings, with identical basic geometry, and have the identical function. Crtitical that the geometry is correct - these fittings in concert with the upper strut trunnions will dictate the rake angle of the gear struts. You see two major holes. The big hole is for the upper strut elbow trunnion, and the smaller hole is for the down lock mechanism pin. Also there is the pair of lugs for the gear door upper attachment. Down lock mechanism you ask? Well here is part of it: The plate (with the "RH" letters written on it) has a keyed hole that fits to keyed protrusions on the back of the gear strut trunnion, and another hole for the down lock pin. You see the LH side one too, with a little clevis lug arrangement for the actuator push rod. In real life that plate is fixed to the strut using a large castellated nut, which I also show. Assembled: So that temporary chunk of .093 tube is slid into the down lock hole, and if I designed it all correctly, properly fixes the landing gear in its down position. Not only that, but with that tube removed, the strut is free to rotate about its trunnion centerline and retract into the wheel well exactly where it is supposed to. I intend to make use of that while building up the leading edge and remainder of the wing, to keep it out of harm's way. Sequencing dictates the upper strut and its sta 75 support go in there early in the process. Temp installed onto the wing box: Ah yes - the wheel well looms. A parting shot of all the MLG components to date (sorry the torque links are not in there - later). One of the big nuts is broken - matters not. It cannot be seen ultimately. OK, next post should be wing skinning, soon followed by the pilot's seat stuff. Take care, and stick with me!
-
1/18 Hawker Sea Fury - VX628 - 1831 Squadron RNVR
JayW replied to airscale's topic in Works in Progress
Wow, how did I miss that Aug 31 post? The skinning is magnificent. If you wouldn't mind, can you give an executive summary how you got those louvers done? What really impresses me is that one looks like the other. Also, glad to see your weak MLG problem appear to be solved. -
I feel your pain John. You know I do. But you are the master fixer.
-
Hi Mike - totally captured the absolute badassery of the Thunderbolt. Makes me want to 3D print one in 1/18......well, not really.... Well done.
-
Nice work! I was about to say, solder comes in very many diameters up to .125 inch, and down to less than .01 inch I think.
-
Yes. Easier that way. Back when I was creating point data for surface definition, I was inputting x, y, z coordinates directly into Rhino as points in space, from big tables of points on NAA surface definition drawings. A gazillion of them, and I am not finished - I have not created the tail surfaces yet. That was tedious enough - to divide by 18 each time would have been intolerable! So yes, I have a full size Rhino surface, dozens of full size layouts, and now hundreds of full size printable Rhino details. When my details are created, I perform a copy/paste in Rhino of the digital solid within the model, and scale the copy by 1/18. It is that scaled copy that I then save as an STL file, which is readable by the slicing software (for me, Chitubox). That software allows me to orient the part the way I want for printing, and it creates the array of supports automatically. Although that array is modifiable.
-
Thanks you guys. Here is the magic. First, I have access to 1940's engineering drawings for a few aircraft. Not very many aircraft have their drawings available, but some do. The P-51 variants are defined by drawings which are available. A subscription to Aircorp Library gives you access. Second, 3D printing has come into its own. Now that's magical. To use it, you have to learn a CAD design software of some kind (mine is Rhino), but once learned, one can convert 2D engineering drawing data into a 3D model, which in turn can be scaled (in my case to 1/18) and then sent to a 3D printer. None of the rest you see here is magic - it's just modelling.
-
Well Michael - yes this is an issue. 3DP resin is pretty stiff and brittle once cured. Obviously, the key is to somehow make sure any kind of stress or load that results from clipping not be seen by the part. Usually when clipping a part off, there is a bit of a shock load when the part separates (it is a small local fracture, after all). That alone can break a particularly thin part. And this is sometimes exascerbated by the thickness of the clipping element (a blade) forcing a further separation between the part and its support. If there are other adjacent supports still intact, then you have just imposed a stress on the part in addition to the shock load. Sometimes, removing a part while leaving a larger portion of the support (or sprue if you wish) still attached works. Then the challenge is sanding off or otherwise removing the remaining portion without damaging the actual part. Also, if your clipper or knife, or whatever you use to separate the part from its supports has dulled, that invites breakage as well. My experience with 3D printed parts, both large and small is extensive by now, and getting more extensive each week. I have not completely solved it, although as long as I am uber-careful and not rushing it, and my tools are nice and sharp, I break parts much less often.
- 129 replies
-
Hah-ha!! Really.