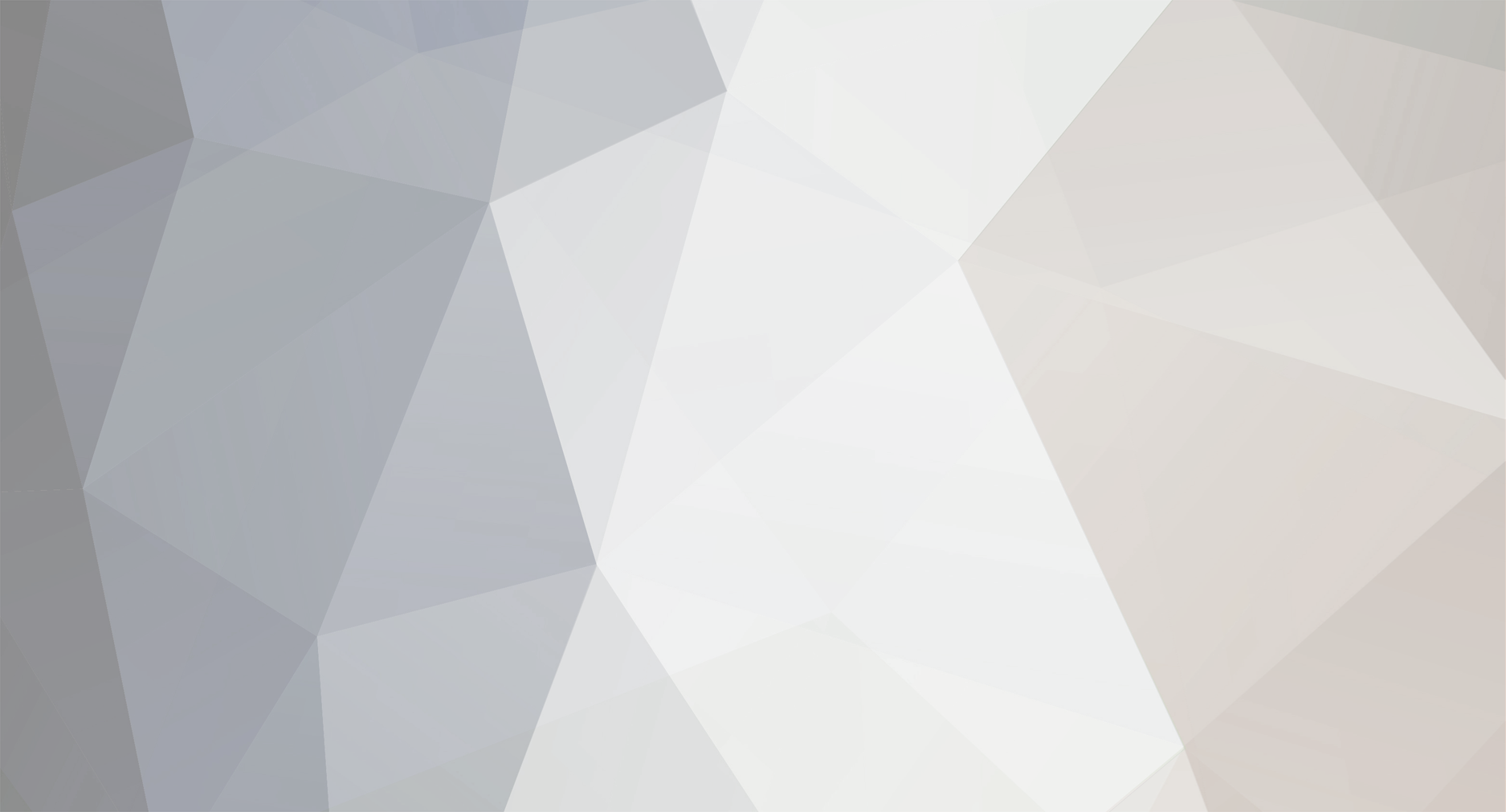
JayW
LSP_Members-
Posts
2,317 -
Joined
-
Last visited
-
Days Won
26
Content Type
Profiles
Forums
Events
Everything posted by JayW
-
I'd pay some serious coin for that.
-
Wonderful engine nacelles Craig! And with a new material! The contrast looks good - wish I had done something like that on the Mustang engine cowl behind the exhausts, rather than painting it. You have to be very pleased that the steel worked for you - another worry addressed. I have so many worries on my own project I sometimes wonder why I am doing it!
- 1,592 replies
-
- scratchbuild
- rivets
-
(and 4 more)
Tagged with:
-
High praise indeed - have you all seen Pete's 1/16 Talon build-in-progress?
-
OK Troy: This is going to be a long journey.
-
True!! Every time I see a detonator box it reminds me of a face with bloodshot eyes. Peter - as you of anyone can attest, digital design and 3D printing opens up a new world to heavy lifting modelling where scratch building is used alot (in this case the whole model!). For this project, the Rhino program allows me to design tooling right along with the actual parts. I can fit and check clearances, and know that critical points or surfaces of the tool or fixture or jig are spot on relative to the parts or assemblies I want to use them for. It's so easy - building them is not a big deal. I used alot of jigs and tools on the Corsair too, as you might recall, and I could only have done it with Rhino or some other digital design program. Man - to do that R-2800 over again in Rhino and 3D print......maybe one day. Anyway - yes you have let your angst be known before about matching up complete skinned sub-assemblies. The concern of course is skin panel gaps at the interface. I share that concern, but for me I have to weigh that against skinning a much larger model later on, where there are more things to break. Skinning, after all, especially compound contoured stuff, is a heavy-handed undertaking. On the Corsair, I broke off landing gear doors umpteen times during that build - most of it due to skinning the wing after the doors were already installed. What were once beautifully done door hinges are now globs of CA. And, the landing gear were subjected to terrible risk and I am dam lucky they didn't break off. Those parts just didn't lend themselves to later installation, so I was left with decisions to make on sequencing of skinning operations. That's just one example. That said I will admit right here that skinning the engine cowl early on was less about that and more about being impatient to see what a blue-nose Mustang with "Cripes a Mighty" on the side looked like in the flesh. Now I live with the consequences. However, my point about the wonders of digital design and 3D printing - it all improves accuracy to the point where completing a sub-assembly and skinning it has a better chance of matching up well with another sub-assembly. Not an infinite amount of skill; just the advantages of latest tools. I added a strip of .01 x .03 plastic to the main jig front surface that is common to the aux nose jig. And that fixed the out-of-flat condition I described last post, after a fashion. That joint is just a bit flexy, and I hesitate to really torque down the two nuts that hold the two jigs together. They are plastic after all. I just have to make sure the two jigs are on a good flat surface as I monkey around with this skin joint. Anyway, that improved the gap between engine cowl and forward fuselage - take a look: I can sure live with that! Note I have finished off the skinning of the windshield surround panels. They now match up pretty darned well with the engine cowl. Skinning is so rewarding - here is one of the three panels just before bonding: Lousy picture.....sorry. So feast your eyes on the fully skinned gleaming natural metal windshield surround - next time you see it, it will be mostly blue: Now off to do electrical boxes and such. Then, that blue paint. Stay tuned.
-
1/16 scale scratch built AT-38B Talon-The Smurf jet is back!
JayW replied to Pete Fleischmann's topic in Works in Progress
Pete - this is just magical. Shrink ray modeling. I am humbled. -
Let's get up to date! There have been some issues, at least in my head, that needed to be resolved. One, the side windows. I don't like the ones I did myself. So I await the 3D printed transparencies from Shapeways - due in a week or so. It is my hope they turn out as nice as the Malcolm hood has. Two, blue paint that has been sitting for months - I feel I need to finish up the blue painting while the paint is still healthy. Because if it dries up, I will have great difficulty matching up a new batch. In the mean time, I have been working on the RH side of the cockpit wall where we find the radio gadgetry and some electrical equipment. Recall in previous posts that radio equipment for US ETO fighters was pretty simple especially for Mustangs with fuselage tanks, where the tank has used up alot of space where radio equipment went. Hence all they really had was the VHF SCR-522 equipment. Missing was IFF (identification friend or foe) equipment and low frequency radio equipment (the Detrola). The VHF SCR-522 consists of the following components: Transmitter-receiver - the big box behind the pilot's armor plate on the upper radio rack (to be done later) Dynamotor - a slightly smaller box also behind the pilot's armor plate on the upper radio rack (to be done later) Jack box - a version of this is included in the cockpit RH side stuff Radio control box - this item is included in the cockpit RH side Antenna mast - the familiar nasty looking spike antenna we see on all ETO fighters. Although this will be replaced by a whip antenna as part of the Malcolm hood modification. Here is the finished radio and electrical equipment on the cockpit RH sidewall: You see there in the forward-most bay the dominant black main switch box, below it the interior green radio junction box, and just aft of the radio junction box the fabric covered connector panel. The next bay aft has the SCR-522 radio control box with the red buttons, below it the jack box bracket, and below the jack box bracket the detonator box, and aft of the detonator box the silver mic adaptor box. I attempted to wire this equipment but the drawings are not very good - hope I got it close.... I may or may not include microphone cords. All this stuff except the fabric covered connector panel, and the red buttons, are 3D printed from my Rhino models, as usual for this build. You also see radio support brackets (3D printed), at least the one with a blank area where other radio equipment would go (IFF stuff), but is missing on this aircraft. Lastly another shout-out to Peter for the decals. They are marvelous. At this point, the sides of the cockpit area are pretty much complete. Here they are: Late additions are the flare gun stowage bag on the LH side (with the two brass buttons), and the map case on the RH side. The map case is just simple plastic sheet parts. I must mention - for those of you who followed the Corsair build, you may agree when I say the P-51 cockpit is much more simple than the Corsair cockpit. Mind you, I still have the floor to do, and some other stuff hanging off the IP panel, as well as the pilot's seat and armor plate. But there just is not nearly the amount of complexity. The Corsair cockpit was a nightmare! All right - I have been nervous about the blue paint. So what I have decided to do is to go ahead and paint the remainder of it on the windshield surround part - this: In order to do that, the rest of the skinning has to be done. And in order to do that, I have to fit this part to the already completed engine cowl, and tidy up the panel line between them. In order to do that, I feel I have to tool these parts up to one another. So I designed and built another jig: This new jig is part of a simpler plan than the one I laid out a couple posts ago. This way, I can still utilize the main jig (minus the firewall bulkhead). Construction and concept are similar to the main fuselage jig. That new bulkhead has a post on it that fits into the prop shaft hole in the nose of the engine cowl. Which will assure a proper orientation of the engine cowl to the forward fuselage both up/down, and sideways. The bulkhead can slide fore and aft in the center slot (the mounting holes are slotted), similar to the two end bulkheads on the main jig. This jig, or better an auxiliary jig, will bolt onto the existing fuselage jig that is working so well for me. Like so: Note that the firewall bulkhead has been removed. In its place is to be the actual firewall (actually a simplified version of it just for this exercise): Two parts - a top and a bottom - 3D printed. They fit onto or into the aft face of the engine cowl, which has just awakened from a months long winter hibernation. Note the firewall has the same four longeron posts that the jig bulkhead has. The beauty of digital design - the locations are identical to the zillionth of an inch. Much fiddling was required to get the firewall parts to fit perfectly into the big engine cowl part. Dimensional accuracy on 3D print parts is not quite perfect - parts grow just a bit, such that male and female parts when designed without any gaps often clash a bit with one another. That was the case here. Before using this new aux jig, I reloaded the fuselage side panels and windshield surround into the main jig, minus the firewall bulkhead, like so: The holes in the longerons are loud and proud in that picture - waiting to mate up with that new firewall. And here is the new aux jig in action with the engine cowl plus firewall loaded: f The jig is now about 13.5 inches long, and it is unwieldy to jockey around. Big model. The concept works great, but I got a bit of a surprise - tapering gaps at the firewall interface: Both sides. Not bad, but it makes me wonder if something is in error. I do notice that once the aux jig is clamped up and bolted to the main jig, despite my efforts to get it just right, its forward end has risen up a few hundredths of an inch above the flat desktop. That would cause that tapered gap, and maybe that's all there is to it. So I am going to shim between the jig surfaces to eliminate the condition, and hope that tapered gap disappears. Actually it matters little - when I skin the fuselage side panels, that gap will be hidden, and turn into a normal panel line. Still, I want that Mustang nose to be spot on relative to the rest of the model. Next steps - I believe I am going to adorn the windshield surround assembly with the electrical equipment that hangs off it - several boxes and a lamp. I don't want to do that work after I paint on the blue, because there will be alot of handling and that paint is a bit fragile. After that - then I will put the parts back into the jigs and skin the windshield surround, and then paint! You will see the results next up. Hope you like that aux jig - I sure do. Later folks.
-
Tamiya F-16 Aggressor, Kicked Up a Notch- KLP Shout Out
JayW replied to chuck540z3's topic in Works in Progress
The master of paint, at it again. You renew my spirits and make me want to do better with paint jobs, my weaker skill. And this build is F-16 101. I am no jet model maker, but man - you are making me wonder why not. I like your comment a couple of posts ago about why you detail something that will not be seen - because it's fun. Here, here. I agree. -
1/18 Hawker Sea Fury - VX628 - 1831 Squadron RNVR
JayW replied to airscale's topic in Works in Progress
Man - that's a whole lot of Rhino time! Beautiful! Can you share with us what you are using as reference for all that gadgetry? -
1/18 Hawker Sea Fury - VX628 - 1831 Squadron RNVR
JayW replied to airscale's topic in Works in Progress
Yup - it's cheating. -
Nice paint job Peter! I imagine it's pretty fragile. It is beautiful none the less.
-
Jim how is it that your bench is so free of clutter? Mine is just awful.
-
Remember this? That was posted on Nov 21 of last year - four months ago. The finished engine cowl section - painted and all. There is still some more blue that has to be applied to this model - around the windshield, and the uppermost panels between the windshield and the firewall, which is the aft end of this sub-assembly. You will recall that I, in my impatience, just had to apply a final topcoat to the forward end of this P-51. I couldn't wait to show off the blue-noser blue. Well now it occurs to me that the paint cocktail I ended up with is not going to wait forever for me to complete the forward fuselage of this uber-complex model. It has already been four months since I shot that paint, and it will probably be something like another four months to complete the forward fuselage such that I can skin it in aluminum to match the finished engine cowl section, and paint the rest. I am screwed if the paint decides to dry up; I have no confidence I can match up a new batch to the old batch. To review, this is the combination: Tamiya medium blue XF-18 (49% plus) Vallejo medium blue 70.965 (49% plus) Vallejo white 71.001 (quite a few drops, but quantity unknown) No way would a new batch be perfect. Were it all Tamiya, I would not be stressing as much about the shelf life. But it isn't. I just don't know how long its shelf life is. So far it seems fine after four months. Am accepting comments from the master painters here who are tuning in. So I think I am going to hit the pause on the assembly plan, and try to get the rest of the blue on sooner rather than later. To do that, I have to mate up (dry fit) the engine cowl section to the forward fuselage section in its current state, and skin the forward portion of the forward fuselage section to match the already skinned engine cowl section. I do not trust using the jig to trim the fuselage section aluminum skins. In theory it would work, but in practice, I don't think I will get a great match to the engine cowl. And it needs to be good. In order to do that, I must be able to assemble the two nearly complete sides of the forward fuselage section, and the fully complete windshield surround section, without the benefit of the fuselage jig. I think I know how to do that: 1. 3D print the firewall, with its four posts that match the holes in the forward ends of the four longerons. Just like the forward end of the jig does now. My firewall is already mostly designed in Rhino. It won't take much to finish it and print it. Fit the firewall to the engine cowl and then the forward fuselage can be fit to the firewall, and taped in place. 2. Rhino design and print a mock station 200 frame, just a plate with four posts to match the holes in the aft ends of the four longerons. Again, just like the aft end of the jig does now. This part can be taped to the side panels and will stabilize the aft end of the side panels and keep them in place. 3. Rhino design and print a simple square plate with four posts that match the four wing mounting points at stations 104 L&R, and 146 L&R, on the lower longerons. Again, just like the jig does now. Tape this to the side panels also. 4. Tape the windshield onto the side panels. This should give me an accurate forward fuselage assembly that holds shape acceptably and can be fit onto the engine cowl, complete enough to skin the forward end of it, to perfectly match. Maybe skin just the windshield surround, since the blue doesn't extend down to the side panels. Once the trim is final, mask up for the remainder of the blue, paint it, and problem solved. That is if there is a problem at all. If the shelf life of my paint is alot longer than a half year, then I don't need to do this out-of-sequence work. What do you think?
-
So the canopy frame sits on top of a vac form. How thick is the canopy frame?
-
1/18 Hawker Sea Fury - VX628 - 1831 Squadron RNVR
JayW replied to airscale's topic in Works in Progress
And he's off! Speedy you are. Right now I am slow as a tortoise. That Sea Fury 5-blade prop and spinner look awesome. Raw power. It looks as if the engine will not be seen very much. Will you be detailing it? -
Status update - I just ordered a set of aft cockpit windows from Shapeways. The transparencies I made myself just do not cut the mustard. Good lord this model is getting expensive. The price of those two windows is as much as a pretty nice 1/48 kit! So was the Malcolm hood. Radio equipment - what goes in there and what does not? I got the story from the P-51B/C Erection and Maintenance manual, and the Operating manual. So WW2 fighters essentially have two kinds of radio equipment - communications and identification. For the P-51B/C, its communications radios were the familiar SCR-522 VHF equipment, and the long wave Detrola equipment. But the ETO never used the Detrola, and that equipment was removed including the long cable extending from the forward fuselage crown to the tail. Too many modelers go through the unnecessary trouble of making that wire and modeling the associated equipment in the cockpit if they are modeling an ETO aircraft. Not me. As for identification equipment, there were several versions of IFF (Identification Friend or Foe) equipment provided. Most of it resided behind the pilot armor on the lower radio shelf, and some of it on the RH side of the cockpit. BTW - it is this equipment that required the detonation switches you see in WW2 aircraft cockpits. The IFF stuff was top secret, and in the event of a survivable crash in enemy territory, it had to be destroyed. But once the fuselage tank was introduced, its volume wiped out that space for the IFF radio equipment. So, the equipment was simply removed, and everything else that was in that compartment (like the battery) was moved to the upper radio rack behind the pilot's head. Period. No IFF capability for those fighters. So just the SCR-522 stuff and nothing more. You will see some of that equipment (what resides on the RH side of the cockpit) next update.
-
Awesome!!! Stunned. So, I guess I could ask Peter myself, but I am so curious what plans were used to make that 3D printed canopy part? Just pictures?
-
Could be the best looking spit model I have ever seen Guy. There is something about most spit models where they look like....models. Don't know why. Not so this one. So I guess congratulations to Airfix too? Well done!
- 37 replies
-
- spitfire
- 1/24th scale
-
(and 2 more)
Tagged with:
-
Airfix 1/24th scale Mk.IX Spitfire........March 2024. All done
JayW replied to geedubelyer's topic in Works in Progress
Oh Guy - you've been busy while was "down unda". What a beautiful Spitfire. Your black and whites gave me a double take - thought I was looking at a real spit. Congratulations! -
So Peter's exposure time for .03 mm layers is 2.5 sec. Mine is 3.5 sec for .05 layers. I guess my question would be are the prints with .05 layers and 2.5 sec exposure underexposed..... I think Peter and I are using the same gray resin...... I might just experiment with .03 layers on the next batch of small parts, coming soon - with 2.5 sec exposure.
-
Hi OBG. Agree 100%. Wouldn't it be fun to get our hands on the kit instructions and/or drawings? I had a ball incorporating the dead cowl flap mod on the Corsair - I actually had the drawing if you will recall. It would not be difficult for the field mod to cover the holes for the light and the insulator using an interior rough contoured doubler with a rivetted patch same thickness as the skin buildup, shaped like the holes. And using the existing fastener holes with flush rivets or bolts to attach the doubler to the airplane. Same for the antenna mast hole, except it has no skin fasteners, so drill new ones. I will probably assume that to be so, and just duplicate that when I skin this beast. Will be easy. And thinking about it, that would be the Cadillac fix. The Chevy fix would be simple exterior patches, as long a there was enough clearance to the lip of the hood as it slides aft. Also correct with resto's. Pristine metal work as if the hood is an in-production feature. Here is one: No patches. BTW - the wooden antenna mast is getting replaced with a whip style antenna further aft. I will have to do that one day. Something like this: And I don't see any patched holes on that aircraft either. But its also a resto.
-
Hi Peter! No doubt a response to my "took all day to print" comment. My settings for standard gray resin: I actually have not been using the .03 mm thickness for anything. Always .05 mm. Perhaps I should for the tiny parts. However I would have to guess at the exposure times. What is yours? The crown skin, when turned vertical, was about 3.5 inches tall, or about 90 mm. Doing some arithmetic, I get these times (in seconds) for the steps in a single print cycle: Exposure time - 3.5 s Rest time after retract - 1 s Lift time - 4.9 s Retract time - 3.2 s That gives total time per layer = 3.5 + 1 + 4.9 + 3.2 = 12.6 seconds Total layers = 90/.05 = 1800 Total time = 1800 x 12.6 sec = 22,680 sec, or 378 minutes, or 6.3 hours. But the several bottom layers are 35 sec exposure time plus the same lift and retract times - so total time is more by about a half hour. So it was just short of 7 hours.
-
Back from Straya as of a few days ago. What a place! And man am I jet lagged. I want to sleep during the day, and I wake up about 3 AM ready to go! Getting better though. So I got the itch to make some more skin panels and see how they look and fit. This would also make the existing panel assemblies a bit more robust and lessen the chance for breakage. Here they are fresh out of the machine, and post cured: Not sure why that side skin on the left looks so ratty, but it sanded out just fine. The side planks printed up well, not so much for the crown skin panel. It suffered a similar deformation I got on my first try with the prop spinner last year: Hard to tell in that picture, but those slanted water lines are where the deformation is. Wiggly contour. That will not do so the part is scrap. I re-oriented the part to print vertically instead of at an angle, and it turned out beautiful: I wish I understood more what goes wrong with some of my prints. Those parts took all day to print up. It was then time to install the aft side planks, and the Sta 168 and 184 full frames. I did this on the jig; here are the side panels after CA bonding, freed from the jig: Yahoo!! The crown skin panel is going to gather dust for quite a while as I further populate the insides of the cockpit, and fabricate the lower radio floor (with the fuselage tank), the upper radio rack, and the cockpit floor. These items along with the side panels will make a good robust forward fuselage assembly one day not to too long from now. Can't wait! But I just had to check out the crown panel in the jig, along with the side panels: Fit is OK not great - gonna require some massage. Starting to look alot like a P-51B. And with the hood: I also dry fit the aft glass into the crown panel and got this: That is a poor fit. Both sides. I checked a couple of dimensions on the clear parts and sure enough they are about .04 inch too short. Reminds me of my Malcolm hood adventures. Well, I was not that impressed by those parts anyway, so I think I am going to pull out my wallet again and have Shapeways make them. That way I will get a better fit, and a better transparency. Next post you will see alot of radio equipment and bracketry for the RH side of cockpit. The Rhino modeling is coming right along. And BTW - here are two questions for those who purport to be P-51 experts: 1. Did the 8th AF in Europe use the IFF (identification friend or foe) radio equipment in fighters? I have a source that says no, and if that is true there are a couple of items I will not have to make. Already I am leaving out the Detrola radio (and the long aerial cable antenna), which I know the 8th AF didn't use in their fighters. But IFF? 2. P-51B/C aircraft had a busy little area right behind the canopy on the crown - a VHF antenna mast, an insulator, and a navigation light: And the crown skin had penetration holes for all three: All three of these items had to be removed for the Malcolm hood modification, to allow the hood to slide aft. My question is does anyone have any pictures of how these holes were covered up? I would like to include that once I skin the crown (if I live long enough!). Later alligators. Thank you for looking in.
-
Tamiya F-16 Aggressor, Kicked Up a Notch- KLP Shout Out
JayW replied to chuck540z3's topic in Works in Progress
!!!! Heavy lifting indeed Chuck. I don't know where to start - let's just say I am impressed. And, I love how you are trying to keep track of config on an aircraft that has seen so much change. -
Oh man - the etching primer..... So you used an etching primer on Lope's Hope did you not? Not the same stuff? On the Corsair, and also on the engine cowl of Cripes-a-Mighty, I used Tamiya x-22 clear from a bottle, thinned 50%, this upon the recommendation of Chuck I seem to recall. Sprayed from the airbrush straight onto the aluminum. And it worked at least as well as any of the etching primers, for reasons I cannot explain. And the Corsair is 100% painted. However, neither had a mirror finish. Just polished with wire wool. On Cripes, I used post-it notes for the blue-noser blue because they have a weak adhesion. Hope the next application works. Really hope.