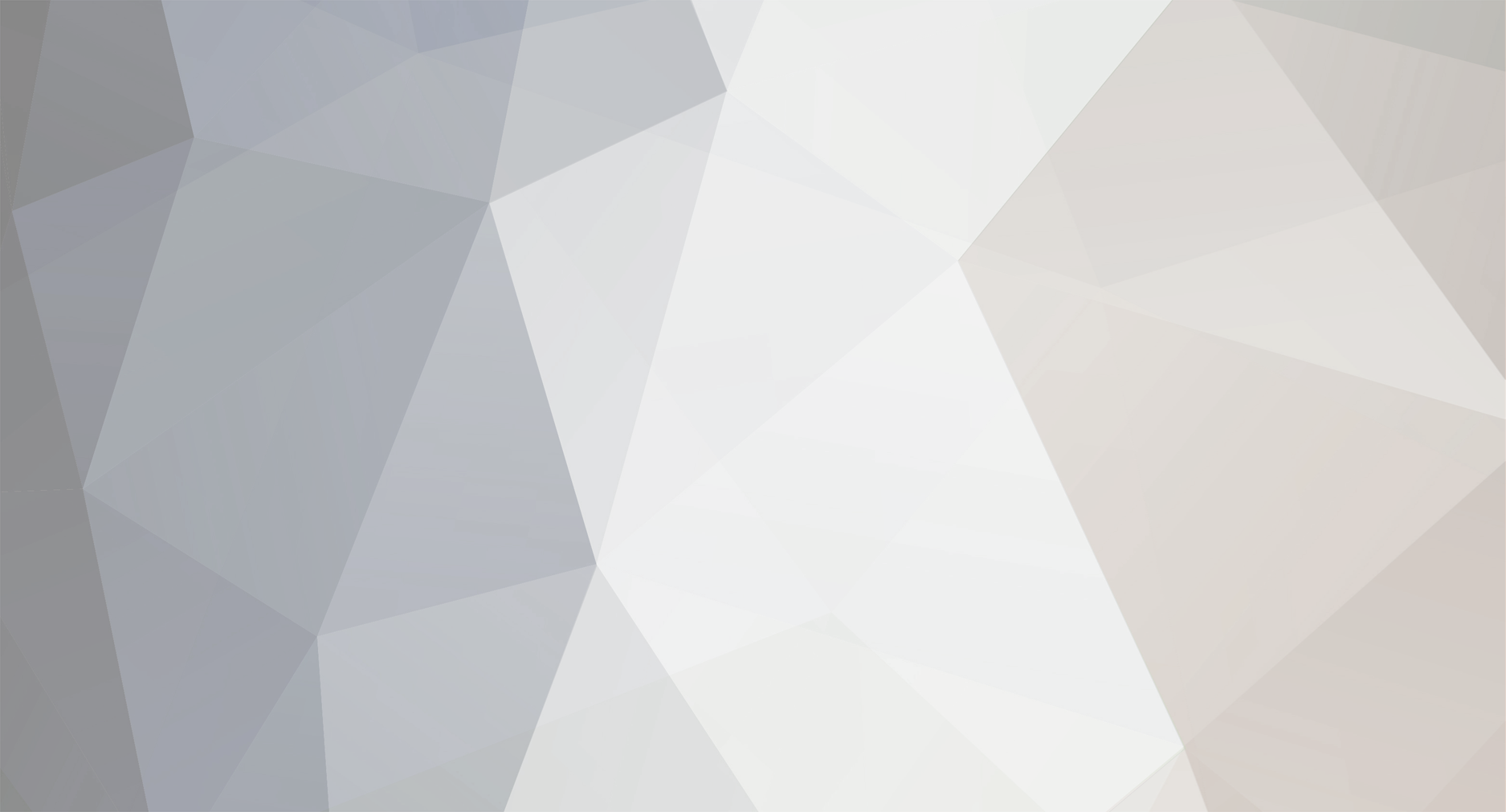
JayW
LSP_Members-
Posts
2,317 -
Joined
-
Last visited
-
Days Won
26
Content Type
Profiles
Forums
Events
Everything posted by JayW
-
1/16 scale scratch built AT-38B Talon-The Smurf jet is back!
JayW replied to Pete Fleischmann's topic in Works in Progress
Beautiful. So you are seeing the finish line. Looking forward to your RFI post. -
Hello y'all. Where am I on the P-51? Well, I decided to hold off on further wing-to-fuselage fillet fairing work. It just didn't sequence that well. Instead it was finally time to start the wing work. To do this I had to decide how I am going to design and build up the wing. Some of you (Airscale for sure) would advocate getting some brass sheet and make a full span set of spars, no splices. And build up from there. Or something along those lines. The wing span of a P-51 is 37 feet. In 1/18 scale that is 24.66 inches. Big. And unwieldy. I just dread working with something so large for so long. Instead, impressed as I was with the surprising robustness of my big Corsair wings which had wing splices at the folds, and having some confidence that a spliced wing for this 3D print project could be equally robust, I decided to not shy away from splices, and make full use of the 3D print precision, and design really strong and precise spar splices such that the parts can fit in my 3D printer. At least until it proves to be a bad idea. So I was off to the races. First though I thought I would Rhino-design the flap: Lots and lots of work. It is not quite ready to print off parts yet. But trust me - when it comes time to make the flaps, you are going to like them. 3D printed and skinned in aluminum. Then it was on to wing structural box components - front spar, rear spar, upper and lower inspar skin panelling, BL 0 inspar rib, and many other ribs. Here is what I have so far (skins hidden): And the spliced wing box build plan (skins hidden): All parts 3D printed. Note the quite large spar splice plates. The splice locations, as it stands now, are just inboard of the landing gear trunnions, such that the center section barely fits onto the build plate of my 3D printer. Also, the outboard wing box sections will be just small enough to fit on the printer as well, leaving only the wing tips to be separate. The actual airplane is that way, with separate wing tips. That's the plan. It then occurred to me that it is vital that the center section actually fits to the fuselage, as designed. Could there be surprises? I better find out now with a simplified part rather than a complicated part. So why not print off a simple test part! Recall there are four very important wing attach points on the fuselage lower longerons (circled in red): Also recall those holes were tooled up with my fuselage jig. My wing box test part must duplicate how I will build the attach points, and mate up exactly with those holes. So, I cut off most of the wing spars in Rhino, joined what remained of the spars with the center rib, and the LH and RH innermost wing ribs, and printed it off: Note the rear spar has integral fittings sticking up proud - two of the four attach points. That is not how it realy looks, but fear not - you cannot see the rear spar once finished up. But you can see the front spar inside the gear wells. So I am going to have to pay attention to configuration and model it right, including the wing-to-fuselage attach fittings - this circled in red: A Rhino-designed test part: And the finished test wing box: Those attach fittings have Rhino-designed location pegs, and matching holes in the spar web. So stoked. Would those four brass posts match up with the holes in the longerons? After a fashion, I can say yes!! Whew! Here: Victory. The fuselage jig paid off, again. So I don't know if it is evident in my description of this work, but this is huge for this build. The fit is good enough that I am not going to have to make a big wing jig. Instead I will take advantage of a big burly heavy gage wing box center section, with four precise attach points, and robust spar splices. And now I have confidence that my wing will fit onto the fuselage, in the same way a real P-51 wing fits onto a real P-51 fuselage. Not only that but the wing dihedral, its angle of incidence, and it's planform symmetry should be right on. It's been a good day. There will also be a stabilzing exterior stringer on either upper skin panel that will fit inside the lower longeron flanges, to further strengthen the wing/fuselage attachment. Also like the real thing. That comes a bit later. The wing/fuselage attach will be robust; I will not tolerate otherwise. Next post I plan on showing you the larger real wing center section with lots of parts, parts seen inside the wheel well. That's the plan. The wing is off and running. Take care, til next time.
-
Michael - fixing errors either by the builder or the manufacturer is part of the fun IMHO. Great job on this difficult build. You have to hand it to the Italians back in the -40's. Their aircraft were under rated. And I too know little about them and how they faired. What, if you know, did the most to defeat that air force? Were the Americans around at that time, in numbers? And if so was it those pesky Mustangs and Thunderbolts?
- 129 replies
-
Wow it is indeed very large! I am very familiar with large models. They require large work areas, which I do not have. Therefore, I break things often. And also I fashion my builds such that final assembly can take place as late as possible. My 1/18 P-38 comes to mind, which was an unbelievably large model. Ridiculous. I was constantly bumping it against anything and everything. Your Stirling is probably every bit as large. Let's see: P-38 wing span and length - 52 ft and 37 ft 10 in. At 1/18 scale that is 34.67 inches by 25.22 inches. Short Stirling wing span and length - 99 ft 1 inch and 87 ft 3 in. At 1/32 that is 37.16 inches by 32.72 inches. Your Stirling is bigger! Be careful!
-
Good Lord man!! This is really exciting.
-
Always exciting to see big stuff coming together. And yes it's looking very much like a 202. As for breaking pieces off, man I can relate!
- 129 replies
-
Oh man glad to see progress on this most excellent and singular build. The Stirling was a flying bomb bay.
-
1/18 Hawker Sea Fury - VX628 - 1831 Squadron RNVR
JayW replied to airscale's topic in Works in Progress
Yup that's my problem. Increasingly, my right wrist is becoming more intolerant of rivet punching. Am experimenting with different ways to hold the awl, but I think my all day rivet punch sessions are over. The Sea Fury is coming along very nicely! Great metal work. -
I'll be watching this. I feel the need for speed.
-
OK, I have spent the last few days on aluminum skinning, one of my favorite things to do (sort of). Awl punching hundreds of fastener marks does get old. But a good panel is very very satisfying. The big plank side panels that I showed last post (the LH one) are not that challenging, but they look great once glued on. The challenge came with the panels and cowls and fairings under the big side planks, in the radiator area. Months ago I worked very hard digitizing the complex shapes in this area, and it was fun to work with the real parts. Here is part number two (part number one, its opposite) is already glued on: It goes here: It took a couple of tries and lots of heavy duty burnishing. Those parts were probably the hardest of the dozen or so parts I did over the last few days. Here is the fruit of my labors: Lots of access doors, three fuel tank vent cups, the oil cooler outlet door, the coolant radiator outlet door. The coolant radiator outlet door is dry fitted for now. I want to be able to close it when it comes time to paint invasion stripes. Then after that, I will glue it in the open position. Note the blank exposed resin areas for the aft most wing-to-fuselage fillet fairing and four locating holes per side. That is my next task - to install these fillet fairing parts, putty them over, and prepare for skinning one day (not now). You will see that next post. I think that is about it with fuselage skinning for quite a while. I was tempted to do the flat planks under the cockpit and windshield, but the prudent modeler would wait until it is time to install the (already completed) nose of the airplane. After working with those fillet fairings, I will begin Rhino work on the wings!!!! I am stoked about that. It's been a good week of progress. Stay with me - adventures ahead.
-
That from my last post. What a jinx. While doing a little assembly work around the radiator area, I shattered one of the radiator faces: My bad - I should have made them thicker, and I wasn't being careful enough, as usual. But one of the great things about 3D printing, I can make another one, and I did, and a bit thicker too. Here it is safely installed onto the 3D printed aft radiator fairing: See the little hinge fittings for the exit door? Soon. Some more assembly work: The Rhino designed and 3D printed air inlet - the oval shaped radiator face represents the oil cooler, as mentioned last post. And further back in the cave is the front face of the coolant radiator. Lest you think these faces are easily seen ultimately, not so: Nearly but not entirely invisible with the inlet scoop attached. Remember that inlet scoop? I struggled with that one months and months ago. So last post I said I was thinking about skinning this section of the fuselage. And I decided to. First task was the aforementioned 3D printed radiator air exit door: I chose not to skin the inside of it; it would mute the beads. This was not a difficult skinning task, only I had to be careful not to fracture the two upstanding walls of the door. Almost the entire fuselage aft of the side windows and onto the tail section is painted with full invasion stripes: That includes the radiator exhaust exit door. Right over that shiny aluminum. I will give it a bit of chipping when the time comes. MOF, all you will see in the remainder of this post will ultimately be painted over with invasion stripes. Then, it was on to the difficult crown skin, made from soft annealed aluminum sheet, to drape over the slightly compound contour: Back to the major manufacturing splice at Station 248. It required a bit of convincing to lie down onto the 3D printed and compound curved surface, but it did after vigorous burnishing work. I don't very much like how this material responds to the awl punch for fastener marks. It's just so soft, the marks are a bit too prominent, and they cannot be burnished down all that well. Had the same problem on the Corsair. Oh well - I think all of us who skin models with aluminum have the same issue to one extent or another with annealed material and fastener marks. The side panels however go over nearly single curvature, so I could use the harder litho that Peter sent me eons ago: Love that stuff, greatly prefer it over the annealed stuff, and fastener marks look very convincing. However it was here or just before where I discovered something rather serious. See that spot circled in blue magic marker? This area, and just under it down to the hole for the fuel filler cap, is depressed inside contour by a good bit. I cannot be sure why it is there. It is either from the printing process where for some reason the part is locally deformed, or I cracked it just from handling - maybe when I was burnishing the crown skin. Just don't know. It extends down underneath the just bonded stiffer side panel, where I was careful not to push it into the depression: The pictures don't do it justice - it looked awful. I had to do something. Knowing that this area is covered with the invasion stripes (thank goodness), I elected to fix it like a car dent - bondo: Peter Castle uses P-38 all the time. I see why - it's great stuff. Meanwhile - I was multi-tasking. I Rhino designed and 3D printed the fuel filler cap, from drawings, and from an item on Ebay with good pictures: Also, the LH side of the airplane has a large cover held on by four Dzus fasteners (or Camloks?), I believe to cover a couple of holes in the fuselage meant for cameras for the recon version of the P-51. An easy task using the aluminum litho: It is my understanding that P-51's, even the Allison powered ones, made terrific photo recon aircraft - fast, long range, and they could fight their way out if need be. And here is the offending area, with the bondo fix, the dry-fitted gas cap, and the cover: Surprisingly, I was able to restore the fastener marks in the P-38 without crunching it. Rather than pressing down hard on the awl, I just applied minimal pressure and spun it around and around for each mark. I'll take it! As if I was not busy enough, I took some time to see about those icky foggy side windows. I managed to sand off anything left of the Future and/or Tamiya spray gloss, down to the base resin material. Scary. Then, I pulled out my trusty Turtle Wax car headlight lens restorer kit, and got to work on the multi-step process. And now they look so much better. Here's the LH side window (the right is the same): After restoring the silver finish on the surround framing, I think they will be up to snuff. I could spray clear gloss over them again.....I will decide later. It's kind scary doing that. Over the next day or two I will tidy up the skinning work - some of the joints don't look that great. Next post you are going to see the entire section skinned, including the radiator fairings - which will be very difficult. I hope to show you something really special. Take care and stay tuned.
-
Well I have a big 3D print parts dump for you all. Took two print batches, one for the big parts at .05 mm thickness, one for the smaller parts at .03 mm thickness: One, the forward radiator housing, and the most troublesome and complex one, has already been bonded to the fuselage. It was a tad narrow for some reason, and I had difficulty fitting it over the two lower longerons. The rest are better. There are 15 different parts that are new there (not counting some duplicates), and I do not think I need to redo any of them. That's a first! Yay! Note also that work has begun on those pesky side windows - they look awful and will get worse before they get better. I think I erred greatly on those transparencies. If memory serves, after sanding and burnishing and polishing were complete, I dipped them in future. It was not a great dip, so after allowing some time to cure, I sprayed clear gloss Tamiya over them. It appears to me that the combination isn't good. The resulting surfaces were (and are still, at least until sanding began) a bit tacky and picked up smudges very easily that cannot be buffed out. I dunno - but I am in the process of sanding off whatever is on them, and starting again. This time no future. Wish me luck - I am nervous about it, especially since these transparencies are the weak link of this whole build so far. Back to the subject - a couple of interesting details follow: Here is one of three fuel vents that are prominent little details of P-51 fuselages. One in real life: And in 1/18 scale 3D printed: Note it lacks the cap you see in the picture above it. That feature was added after my subject was manufactured. A tough little Rhino modeling exercise. Prior to the introduction of the fuselage fuel tank, P-51B/C models had two - one on either side of the lower fuselage under the aft-most wing/fuselage fillet fairing. They were for the two wing fuel tanks. When the fuselage tank was added (presumably either by field mod or on the production line), a third vent was added on the RH side just above the radiator air exit door. Here is the oil tank front face, which is visible if one peers into the intake scoop under the wing: I think that is pretty cool for a part that is unseen unless you look for it. Compare to the real thing: That part just had to be a bullet magnet. And the coolant radiator front and rear faces, also visible if one peers into either the inlet scoop or the outlet door (with flashlight): The radiator - also a bullet magnet and the root cause of most P-51 losses I believe. You will see these details in place painted and weathered next post. But a sneak preview of one of the fuel vents dry fitted: I show here all these parts (the big ones anyway) fitted onto the fuselage (almost entirely dry fitted): I am darned pleased that these parts fit together as well as they do. Not perfect, but more than adequate. Remember - I will skin these surfaces. And also it is here that 3D printing parts made from data off the actual drawings bears its fruit - with a correctly shaped lower fuselage where many other model manufacturers don't get quite right. Last post I mentioned that I needed to address the aft-most wing/fuselage fillet fairing - this beastly thing: So I set out trying to Rhino model this shape, just to get something that served as a surface in which to finish up with some putty or P-38 bondo, and then aluminum skinning. What a frustrating exercise in 3D surface modeling. Turned out it needed to be in two pieces, I felt, the lofts were so complicated: And dry fitted: They will serve, methinks. Finishing them off with some bondo and skinning them will be a big challenge. Not sure when I will attempt that - maybe soon. Those parts must be exactly located if they are to interface properly with the wing flaps with flaps up. So I modeled locating pins and holes. With the addition of all those fairing parts below the longeron, the fuselage will be too deep to fit onto the fuselage jig. So let us bid it farewell - here are all the parts that comprised it: I might use it one last time to final install the engine cowl, but to do that I must cut off the aft half of the jig to make room for those fairings! We'll see - it is going to be quite a while before the engine cowl is permanently installed. That jig was vital to this build - may it rest in peace. Lastly for this post, it has been right at a year since I began this project, by starting the surfaces model in Rhino, using the point data on various NAA ordinate drawings. I have added much to it since, and use it still. This picture then shows what I have to offer for a year's worth of effort: What an adventure it has been. Year 2 is going to involve the wing, and hopefully also the aft fuselage and tail. The wing is on my radar now, and I am thinking over build concepts. It will be every bit as adventurous as what has already been experienced. First though, I have more work to do with these new parts, and something tells me now might be the time to skin the rest of this fuselage.... Stick around!
-
Tamiya 1/32 Spitfire XIVe Conversion (Laminar Flow Design)
JayW replied to Thunnus's topic in Works in Progress
I think I know what your favorite part of modeling is. And you are really good at it. A master class. -
Great discussion on the seat assembly! Morrow Aircraft Corporation - I am the smarter for it. Thanks Ralph! Nice to know. But this bird gets the WM seat. So I am in this world right now where one thing leads to another which leads to another. I am in the midst of developing the Rhino models for the radiator intake and exhaust areas below the lower longeron, as reported last update: In order to fully integrate this area so that I can commence with 3D print part making, I have to consider the wing/fuselage fillet fairings, which up until now I have not created surfaces for. So I have been busy doing just that. But, in order to create those surfaces, especially the underside of the aft-most fairing - this one... ..... I must do at least some deveopment of the inboard end of the flap. And to do that, I must try to decipher a flap assembly drawing 73-18001 which is a most hard to read drawing: I am certain that the planners and tooling and fab folks in the NAA factory had to collar the engineers on multiple occasions to help them read that awful drawing. So that they could fab up that first set of flaps back in '42 or whenever. Anyway the inboard end of the flap is kind of complicated, and the underside of the wing/fuselage fairing has to match it. Airscale - if you are reading this, you know this well. At least I have the basic wing surfaces, created back when i started this project a year ago or so. So one things leads to another and another. And it is taking time. Wing/fuselage fairing lines and surfaces are in progress: The aft end is tough. Very tough. Further forward, easy. And the various fairing assemblies in the radiator area are in progress as well: Four fairings, and two hinged exhaust doors. The Mustang enthusiast will recognise the parts instantly. The most difficult development is this one: The real part looks like this (thanks again for the photos Peter C): It isn't finished yet, but close. It includes a large portion of the the coolant radiator intake duct, the oil cooler intake duct, a couple of fuel vents on the skin, a mounting interface for the wing/fuselage fairing. Also I mean to give it two thin flat plates with perforation designs meant to simulate the oil cooler radiator and the coolant radiator, which can be seen if one peers into the sexy intake scoop under the wing. All right then. The struggles continue. Next post I hope to show you some parts. Take care all.
-
Tamiya 1/32 Spitfire XIVe Conversion (Laminar Flow Design)
JayW replied to Thunnus's topic in Works in Progress
What an understatement. I know how pleased you are (and we are) with that. Just beautiful. Especially with the paint lift issues. You are in the finish line sprint. -
Tamiya 1/32 Spitfire XIVe Conversion (Laminar Flow Design)
JayW replied to Thunnus's topic in Works in Progress
I knew this already. Personally I choose subjects that are a bit "war weary" shall we say. That way my less than superb repair skills are just part of the model. This though is perfection. So is the repair. -
So Tony - this got me going some, trying to figure out what is what. Seat assembly drawing 102-53009, which is the appropriate drawing for my subject (a P-51B-10NA) is effective for all P-51B and C aircraft. This drawing specifies a non-NAA item (a purchased item) Schick-Johnson seat up until about about midway through the B-5's and midway through the C-1's. Beyond that, the non-NAA purchased item "SK2016" seat is specified, and this is the Warren McArthur seat. But if you look at the revision block of that drawing, you see interesting things: The date of the C revision is not shown, but the B revision is May of 1943 and the D revision is October 1943. So between those times. The C-revision states that "Schick-Johnson Co" replaces a "Morrow Aircraft Corp". Whaaaaaa?? And it also alludes to a drawing "91-53074". Drawing 91-53074 is an in-house (NAA) drawing fully defining a plywood seat. There are two seats defined on that drawing. One is a re-inforced version of the other, but both are plywood. It appears that NAA at some point quit building this seat (if they ever did - maybe "Morrow" did), and sub-contracted it out to Schick-Johnson, who appears to have not had their own design, but merely built the NAA design, which is plywood. This seat, whoever made it, dates all the way back to the AT-6 (SNJ) Texan, the original P-51, P-51A, and AT-6. I certainly hear of metal Schick Johnson seats. But I see no record of such a thing within the NAA drawings. What do you know that I don't? At any rate - my subject gets the SK2016 (WM) seat.
-
As of my last post, there were two major items left in the cockpit - the rudder pedals and the pilot's seat. So I set to work on them. Model Monkey has a few 3D printed items in 1/18 scale for the P-51, and I took advantage of that and ordered some stuff. This is what I got: Rudder pedals with the NAA emblems, the Warren-McArthur (WM) seat which comes with armor plate, and P-51A/B/C bomb shackles. The bomb shackles will gather dust for an eternity but glad I got them. The rudder pedals - stay tuned. The WM seat - well it's really nice but it is set up for the P-51D model, which has quite different support tubes and its attachment to the armor plate. So, I am going to save it for the time when I do a -D model - a real possibility with so much commonality with the -B. The rudder pedals surprisingly fit into my fuselage with nearly no modification at all. That center post had to be trimmed back to clear the control lock push rod, but that's all. I added some simple details so that I could attach control cables, painted it, and installed it into the fuselage. Voila: From the front: It was no surprise to me at all that with the windshield in place along with the instrument panel and center console, the rudder pedals literally cannot be seen unless with a flashlight and even then only a little. What can be seen are the cables, nearly all the RH cable, and just a bit of the LH cable. Oh well. I know they are there and they are beautiful. The seat. P-51's had two different seats to choose from, and they were interchangeable even though they look quite different from one another. A Warren-McArthur (WM) seat which is a sheet metal ugly looking bucket, and a Schick-Johnson (SJ) seat, I believe made mostly from plywood, and to my eye a more elegant looking item. Sometime in the P-51B run, the WM seat began to replace the SJ on the production line, until by the time the -D model was being produced, it appears that the WM seat only was being supplied. I have some reason to believe my subject had the WM seat. So I was going to have trouble with the Model Monkey seat due to its different support tubes and top mounting brackets. But not to fear - Peter Castle (Airscale) quite a while back gave me a huge data dump from his Lope's Hope P-51C build, and in it he provided a Rhino model of a WM seat that he developed. He did alot of work on it, I can tell. So I took it and messed around with it some and made my own version based on his. A picture of it in Rhino, integrated with my floor panels, the control stick, and the armor plate: It's about 50% Airscale and 50% JayW. Thanks again Peter. You're the greatest. And here is the 3D printed kit: Hairspray method chipping, and springs made from .01 inch diameter silver solder. I am very happy with these parts. Assembled and ready for a back pad and seat belts and shoulder harness: You can see it is a different support arrangement than the Model Monkey parts. Dry fitted into the cockpit: Those pretty springs are hidden. Sad. Shoot - look at the sag in my chain. Gotta fix that. Well I cannot iinstall the seat until I get the seat belts, shoulder harness, and back pad in there. Gonna take a while. God I am ready to be done with this cockpit! So in the meantime, I am modeling up the radiator fairings: Started with the surfaces I created quite a while ago, and began building with help from the drawings. The inner duct contours are challenging, but they are coming along. The exit door too. The hardest one remains - the "twilight zone" fairings where the coolant radiator and oil cooler radiator reside, along with the elaborate ducting that leads into and out of those radiators. In the next few days I hope to have that taken care of. This zone also interfaces with the complicated aft most wing-to-fuselage fillet fairing, adding to the fun. Take care, stay cool all of you in the Northern hemisphere. It's HOT where I am right now!
-
Tamiya 1/32 Spitfire XIVe Conversion (Laminar Flow Design)
JayW replied to Thunnus's topic in Works in Progress
John - your technique with black preshading and primer, etc is not new. Is it? Have I not seen a similar treatement on your recent efforts (the P-47 for example). ??? I absolutely dread the day when I have to paint the invasion stripes and stars and bars on my natural metal P-51. -
Tamiya 1/32 Spitfire XIVe Conversion (Laminar Flow Design)
JayW replied to Thunnus's topic in Works in Progress
Methinks changing that panel line might be tricky? Well, we have the man for the job. What a bada_s Spitfire. -
Tamiya 1/32 Spitfire XIVe Conversion (Laminar Flow Design)
JayW replied to Thunnus's topic in Works in Progress
Yeah John - your paint work is second to none. And as I hae said before - your repair work makes it as if the gaffe never happened. A wonderful Spit you have here. -
Tamiya 1/32 Spitfire XIVe Conversion (Laminar Flow Design)
JayW replied to Thunnus's topic in Works in Progress
Bad to the bone John. And it's getting very close! -
Well Alfonso, occasionally the backward step. But "ever stalwart", from the movie True Grit. Visible progress to show. First, for the control stick boot I ended up using some aluminum foil tape where I spray painted over the sticky side. It had approximately the right stiffness so that it could wrinkle yet hold some shape. The fabric I used previously was a little too stout for this application, and plain kitchen heavy aluminum foil was too thin. Couldn't get my hands on any lead foil, which was suggested. My backup plan was to use Milliput, but I was satisfied enough wtih this. Here it is warts and all: Then, it was time for that floor to be extracted from the tool and installed into the fuselage! One piece at a time, all the while making sure the fuselage still fits onto the fuselage jig with its important interface features (four wing attach points, four engine cowl attach points). The floor controls width to a certain extent, so had to be cautious. It is always hard for me to photograph cockpit floors, but here you are: With the floor now bonded in there, this fuselage assembly is truly stout, and really doesn't need the jig anymore. It holds shape wonderfully. The astute observer will also see the pilot armor plate - a better couple of shots: Never mind the glass - it's gonna get better down the road....as has been discussed. The armor plate is just dry fitted for now. When I get the WM seat, it and the seat will go in at the same time, methinks. The top part is 3D printed, the lower part is just a piece of .020 plastic sheet, with some hairpray chipping going on. Also, have I showed y'all the firewall all painted up? Just in case, here: 3D printed as well. And it and that forward floor panel form the very beginnings of the wheel well (the ugly dimpled bottom of the next aft floor panel will be hidden I think). Gonna be a while before that work happens. That interior green 3D printed fitting serves as the mount for the gear door hydraulic actuators - a feature of the early P-51's, but completely changed for the -D model. And still more progress - here is the newly 3D printed fuselage plug sta 200 - sta 248: A pretty simple part; it will be attached soon. Along with the stuff hanging underneath it - the beautifully contoured and far more complicated radiator exit fairings. Rhino modeling in progress on those parts now. It is not easy at all. Take a look at how long this thing is getting: Tempting fate there... It'll get longer. Next post might be work on the pilot seat, but maybe not. I await seat belt and shoulder harness hardware from Airscale, which might be a while. Also due in the mail are rudder pedals along with the seat from ModelMonkey - hopefully next Monday. Maybe they go in next, with their tricky cables. And I also want to show y'all how the Rhino modeling is coming along with the radiator fairings. Take care, until next time.
-
Tamiya F-16 Aggressor, Kicked Up a Notch- KLP Shout Out
JayW replied to chuck540z3's topic in Works in Progress
And those missiles! This reminds me vividly of a time around 20 years ago (or more??) when I was in Tulsa OK on business with an engineering firm there, located in a building on the local airport property. There was an air national guard unit there with F-16's. Many days there we were treated to the deafening roar of F-16's taking off one after another, loaded to the nines with all manner of stuff hanging off those wings. So much that it was hard to recognise what was aircraft and what was not. Just a big collection of evil looking pointy nose cones accelerating down runway. Made me wonder how they got airborne, and once airborne, where they were going to use all that ordinance and fuel. Nevada? Caused a work stoppage every time. F-16's are awesome, and have been for quite some time now. -
Tamiya F-16 Aggressor, Kicked Up a Notch- KLP Shout Out
JayW replied to chuck540z3's topic in Works in Progress
Good lord Chuck - your finishing skills are just through the roof. All the models I have watched you build. This one seems to have really put them to the test. I cannotwait to see the RFI. Get that arm well soon.