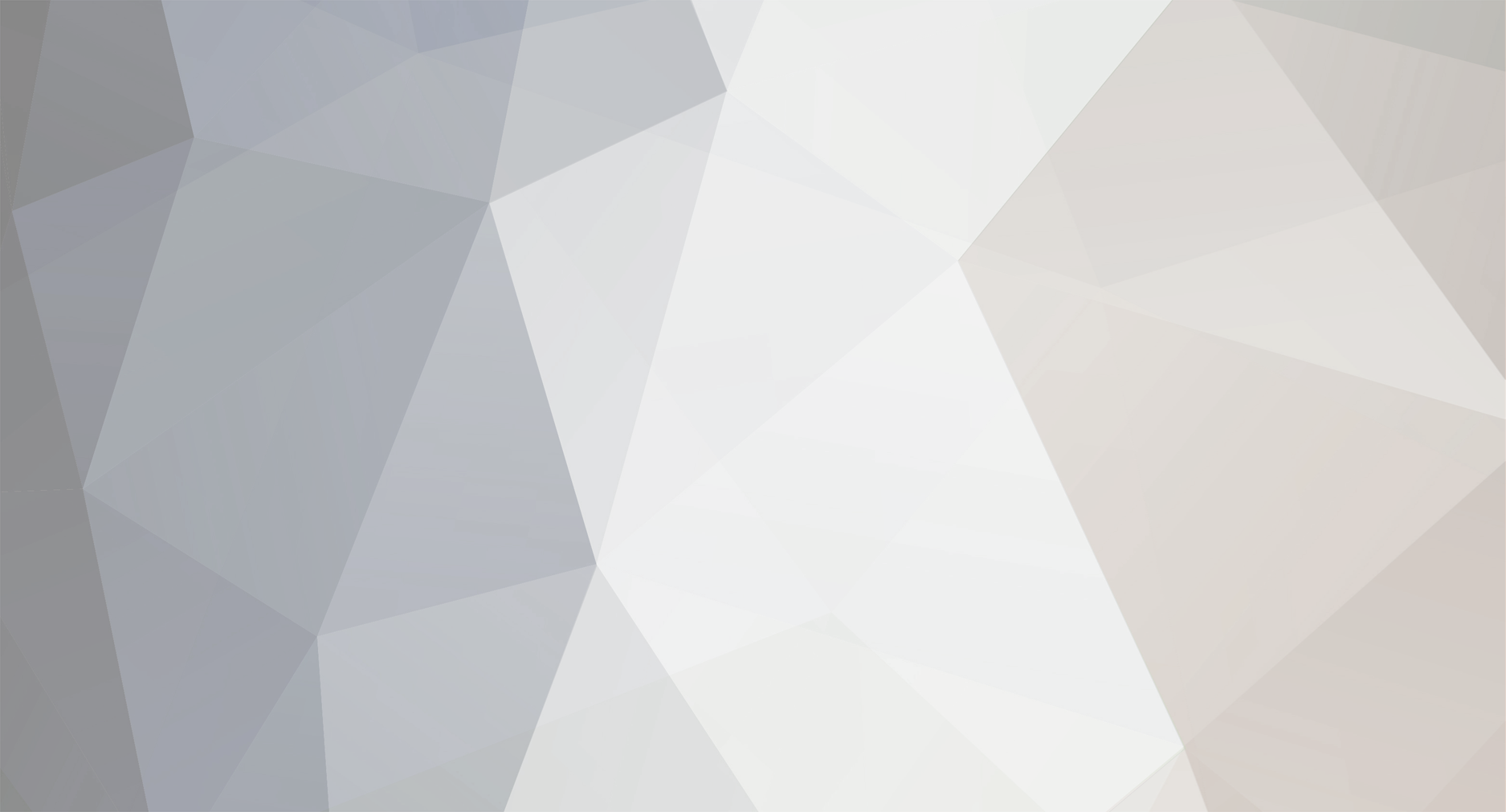
Battlebirds
LSP_Members-
Posts
21 -
Joined
-
Last visited
Recent Profile Visitors
The recent visitors block is disabled and is not being shown to other users.
-
Derek B reacted to a post in a topic: 1/32 Mirage F.1C
-
ivanmoe reacted to a post in a topic: Let's get to know each other a little better. Show a photo of your
-
GROWLER 96 reacted to a post in a topic: 1/32 HS Buccaneer
-
Kagemusha reacted to a post in a topic: 1/32 Mirage F.1C
-
Hey there! It's been a while, since I have any updates for you guys, regarding my 32 scaler Bucc Kit. I haven't done much, since things got bmvery busy for me, making scratch built models for customers. I have 4 on my workbench at the moment. Here in South Africa, we are also on a 3 week lockdown, and I hope to get these projects nearer to completion soon, so that I can get back into the Bucc. I will deffs keep you updated, however, there is a TONNE of stuff to do! See ya real soon Jon
-
thierry laurent reacted to a post in a topic: 1/32 HS Buccaneer
-
Landrotten Highlander reacted to a post in a topic: 1/32 HS Buccaneer
-
Landrotten Highlander reacted to a post in a topic: 1/32 HS Buccaneer
-
Landrotten Highlander reacted to a post in a topic: 1/32 HS Buccaneer
-
Landrotten Highlander reacted to a post in a topic: 1/32 HS Buccaneer
-
Landrotten Highlander reacted to a post in a topic: 1/32 HS Buccaneer
-
Thanks guys Hope some can see this clip...
-
Thank you sooo much folks!! This encouragement is seriously needed sometimes. Once I have completed the cockpit tub, ready for molding, I will post a photo of the Aerodynamix part, just for comparison. There is an awful lot going on in that area and I am trying to work out how to break it up for molding. I was thinking of the following seperate parts: instrument panel, instrument panel shroud, HUD, rudder pedals, cockpit floor with the side consoles, then the side panels, including that beautiful quilted soundproof layer and various instruments/boxes. Then the rear wall. Oh, and two nice bang seats.
-
Could be, if there is interest in a 1/32 Buccaneer Good times indeed Some progress made on the cockpit.
-
Hi Marc! Thanks so much for the kind words! I remember the club meetings in the "old days", at the SAAF museum. You guys taught me so much! Alec, Louis and you.
-
Hey, Renegade! I love your work, man! I think you might be my biggest inspiration. I would love to post that video of the airbrake on the model, but I don't know how to. Looking forward to more of your work!!!!
-
Progress.... the horrible Bucc tub has begun. Starting with the instrument panel. The top layer has the holes and the rear plate has the instrument markings on it. This detail should mold nicely and cast in resin beautifully.
-
Troy, it's elbow grease. Lots of it. Seriously though, I sand the stuff with gradually finer sandpaper, going down to 1000 grit. Then apply floor polish. That Cobra wax in a flat tin. Lavender is ok. Let it sit in a warm environment so that wax seeps in a little and then use old T shirt to polish the heck out of it. Speed helps. I have made the airbrake section and it actually works like the real thing, with the clamshells, drag links and centre guide unit. I can't stop playing with it. Next section I want to tackle is the cockpit tub. Not the most well thought out, nor ergonomic jem. It's a total mess in there. That should be a huge "super fun time" LOL!!!!!
-
As promised, some pictures
-
Hey, Troy, thanks man! I really don't like 3D printing for various reasons. Sure, they're revolutionizing things, but old school is STILL the best IMHO. I have seen many 3D models online and they just aren't accurate. Probably rendered by someone who hasn't researched the airplane correctly or someone who knows nothing about the subject. The files are also very expensive, plus, the actual printing filament is pricey too. The final printed part also needs a lot of work to remove those horrible striations from the layering. Give me some MDF and I'm a happy camper!! I am currently working on the Bucc's airbrake section and it's taking all my grey matter to get it looking right. There are a lot of sepperate parts that need to go together in a relatively tight space back there. Pics soon.
-
Thanks so much fellas! Mark, I used MDF/ Supawood for that canopy form. In fact, as I mentioned before, I use it a lot for various reasons. It's cheap, can be shaped relatively easily and handles vacc forming heat rather well. It's also used, as you saw, on the nose sections for the masters for resin casting. In a "pinch", one could also use hardboard. The airbrake area is a ******* to copy! I am aiming for it to be operational on the model. (Manually, not hydraulically)LOL!!!! I just wanna get it right.
-
Thanks guys. I've made some more progress.
-
Okay, here you go The Dakota. Anyway, back to the Buccaneer. Some more progress has been made The 1/48 Airfix kit helps to see if I'm on par with the general shape. Nose fold detail.
-
Thanks guys! That metal buccaneer was a sister model for Mike Beachyhead of Thunder City. I made a few models for him out of printers lithoplate. There were two lightnings, a few Hunters and two Buccaneers. It was a while back, and looking back on that model, and the fact that I have a real Bucc to work from, it is hopelessly inaccurate! This current buccaneer model is going to be super accurate - as far as I can copy it! I really thought that I could have used the Aerodynamix kit, but there are so many issues with it, that I decided to just start from scratch. It's actually easier to make from scratch than to repair an existing part. For instance, the airbrakes are NOT round in cross section all the way to the tip but starts off round and gradually tapers to a flat oval. Call me crazy, but if one is going to do something mad, then do it correctly!! I have also built two all metal Lockheed Lodestars in 32 scale. All polished natural aluminium. Those were fun to do.