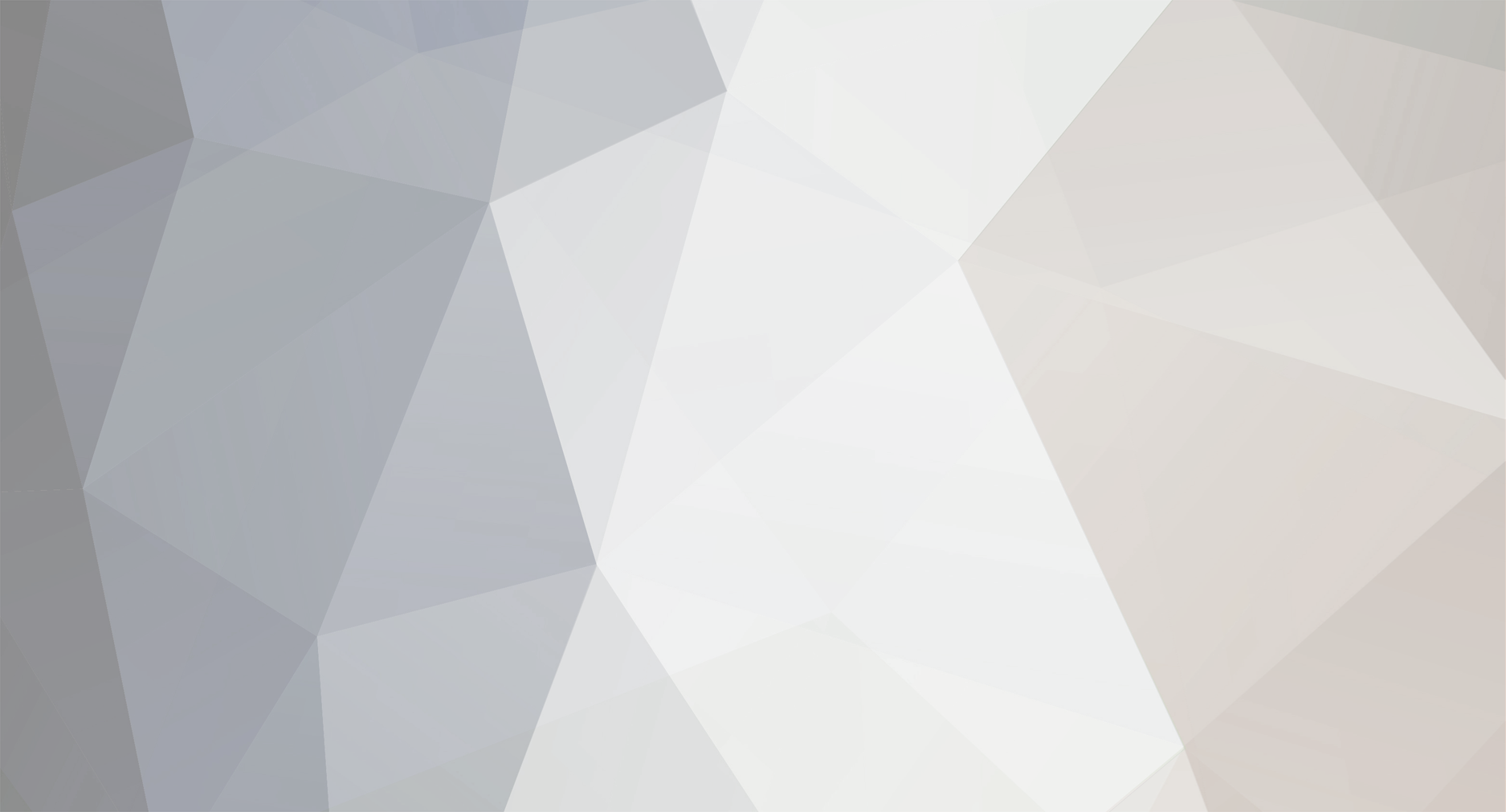
scjh
LSP_Members-
Posts
79 -
Joined
-
Last visited
-
Days Won
2
Content Type
Profiles
Forums
Events
Everything posted by scjh
-
Another challenge of this project was stencils in white for SEA schemes. I learned to use a Silhouette to cut paint masks for large markings, and bought some specialty decal papers to be able to "print in white". I made these for @Dandiego's "The Iron Eyeball". SC
-
My apologies for the long absence. I continued to apply stencil decals to the forward fuselage, but got bogged down with the rescue stencils, some of which needed white and other color shapes. The ejection seat triangles were borrowed from a commercial set. Times like this made me question the sanity of starting on a project that I couldn't easily buy off the shelf decals and parts. I also ran into issues with my 3d printer's reliability as I added more details to the rear tail part. Hopefully I can get back on track soon. SC
-
As an FYI the Collect-Aire T-38A canopy is also a bit short on the back end. SC
-
Good point about the flatness of the KH F-5F rear canopy in profile, @Sabrejet. For what it's worth, this the the Northrop drawing in white outline over KH's instruction (assuming the instruction uses the same CAD model as the kit itself), showing the flatness of the top. Looks like the rear canopy frame does not slope up high enough to have the nice smooth curvature. I had trouble getting resin ejection seats of other brands to sit inside the rear canopy, even with my own 3d printed cockpit floor that I think is at the correct depth. I believe KH's own seat is too short in order to fit in the shallow pit and the canopy that's too low. SC
-
Before KH announced their F-5 family, I was working on a F-5F conversion using Hasegawa F-5E fuselage, so I spent a few years staring at photos, drawings, and 3D models of the F-5 family, including the T-38. In the following composite of Northrop drawings, the yellow is the T-38A and the white is the F-5F. I believe this shows the canopies are the same shape and size. However, I believe the KH F-5F rear canopy is a bit too long. Each square is 5 inches in the following comparison of the Northrop F-5F drawing and the KH F-5F forward fuselage. I would estimate the gap to be about 5 scale inches or about 4mm in 1/32. A simple trimming would probably work. I was also planning on using Collect-Aires T-38A vac canopy at the time, but the shape seems off. Many of the Collect-Aire T-38 kit parts look like resin copies of the Hasegawa F-5E parts. Here's my Hasegawa F-5F. SC
-
Help for the Kittyhawk 32nd scale F-5E/F. Your input is needed!
scjh replied to f5guy's topic in LSP Discussion
There was a 71 page SIG thread: and the tweaklist compiled by @thierry laurent here: For those that have the Zimi F-5E/F RF-5E kits, take a look at the gravity fuel fillters on the spine behind the cockpit. They may have fixed the error, Kitty Hawk kits had them on the startboard side instead of port side. SC -
Hi JeffT, Great to hear anothe 1:32 Scale Eagle in the works! I believe the original pilots in the 44" Eagle came from the 1/24 Revell Gemini kit. Another possible source may be MPC Round 2's Moon Buggy, which is also in 1/24. You'll have to scale them down to 1/32. SC
-
Congratulations Dan, for taking home an award for this FB-23 from OrangeCon. It's a truly impressive sight to behold. SC
-
Thank you Ray! It didn't win anything. There were so many awesome models on display. It was fun just to participate and meet other modelers. SC
-
Instead of sitting comfortably in the display case, the Eagle Transporter made quick a visit to the Nuclear Waste Area "OrangeCon 2024". This was a first time for me to put something on a contest table. The Eagle was disassembled during transport, to be assembled on the table. It was all going well until I realized the Command Module and Engine sections would not fit into the front and rear Cages. I was sure the Cages were facing the correct direction by checking on the oleo structs of the Landing Pads, but I managed to swap the front and rear Cages. Dooh! So had to take it apart to re-assemble. Thanks to @Dandiego who literally lent his helping hands for the re-assembly! SC
-
Thanks again to @Martinnfb for checking in on the Eagle. I decided to make some very simple markings based on MPC's kit decals to spruce up the Eagle a bit. They are not quite "screen-accurate", but should provide a much better representation. This wasn't attempted earlier also because I wasn't sure how waterslide decals will work over the unsmoothed and unpainted surfaces. So I tried tatoo decals instead, which might grip to the surfaces better. One plus is there is no clear coating needed after the ink-jet printing, but a minus is there is no moving the decal around for adjustment once the backing paper is wet. This made decaling a more exciting experience. SC
-
Thank you Alan, John, and Serkan! Your great builds have inspired me. Making slow progress, but Sun Run #4 bands are painted on the fuselage, and decaling has begun. The stencil placements will need some adjustments, and hopefully I can get rid of the slight white borders around the larger decals in the next iteration. SC
-
Hi Bill, I bought one of these for the purpose of making canopies. A single seater Voodoo canopy in 1/32 will fit into the area, but not a double seater canopy if you want a continuous pull. I also tried separating the windshield. The 3d printed buck I used will not withstand repeated use, so I plan to try printing a negative volume, then use something like Durham's Water Putty to make the buck next time. Might also try using 3d print for the framing and just use the vacu-form for the transparency. This was a quick test so I didn't spend any time post-processing the buck. Will probably try a resin 3d print buck evntually. SC
-
Practice masking on a spare fuselage of the yellow bands on Sun Run #4. I found that the walkways were important to establish with positioning of the stripes. The leading edge of the walkways will be modified appropriately to be more perpendicular as these were just scaled up version of the Tiger Wings decals. Most, if not all of the commerically available walkway decals I have found in 1/48 seem to be designed for the two-seater. And like many things I've discovered about the Voodoos, there are multiple versions of the walkways, in addition to the RF-101A and RF-101C having different length intakes. Even the red jet warning stripe towards the back of the fuselage had two possible positions. If one looks closely at the decal mock up in my previous post, one might fnd the US National Insignia is positioned for the A version, which is not correct for the C. In a way I am glad I'm building both at the same time, so I can possibly show off some of the variations.
-
Spent some time working on a few of the many stencils. Thank you to a professional decal maker who gave me some tips on fonts and sizes. Perhaps this is already known by many, but the more I dive into references photos, the more variations I find. Little things like left and right text justifications for the same caution or warning stencil can be found. I don't know if I would be able to cover all of the stencils, perhaps I will concentrate on most importantly the areas around the photo nose.
-
Thank you Derek and Rafael! I am inching along, but hope to cross the finish line with your encouragements.
-
Thank you themongoose, Oldbaldguy and Serkan. All the credits to the look of the Voodoo goes to the original McAir designers. As mentioned before, it definitely has a very strong family resemblence to the Phantom II that came a few years later. I have a bottle of Model Master ADC Gray FS16473, and used that as a reference in a very non-scientific way. :-) After trying Tamiya's AS-26 Light Ghost Gray, which seemed too blue and saturated, I picked out a few other rattle cans in the AS line to try (AS-5, AS-16, and AS-18). If these didn't work, I was going to try Light Gull Gray next. I didn't get into mixing or scale color effects. AS-18 seemed close enough. It does seem to have a green tint.
-
Mock-up of decals.
-
Another round of painting. I thought Tamiya AS-18 was a close match to ADC Gray for the RF-101A in the back. What do you think?
-
Thank you Rob and Alan! Not sure when I'll get to them, but here are some inspirations for fans of the fighters and two seaters (especially for our Canadian friends).
-
I plan to paint these two schemes: RF-101C 60166 and RF-101A 41499/5654. Stencils, this is going to take a while. I would appreciate help on what stencils look like on the fuselage bottom and under the wings, especially Door 104 (viewfinder).
-
On July 3, 2019, I visited the Aviation Education Exhibition Hall in Taiwan. Part of the mission was to photograph RF-101A Block 25 54-1506/5658, one of the three remaining ROCAF RF-101As. I did a photogrammetry run on my laptop the night after the museum visit, and discovered visually the differences between RF-101A and RF-101C intakes (based on Akira Watanabe's photos of 56-0214 from Pima), at least for a geeky modeler. Most books and articles described the the RF-101A and RF-101C as externally similar, and some have called out the various intake types (Type II, IIa, IIb, etc.), but I have not come across one that described the actual difference in look and dimension between Type IIa (production RF-101A) and Type IIb (RF-101C). Ron Easley's book described the Type II Intake as 11 inches longer than Type I on the early F-101As with an extended wing fillet added. I believe Type IIa is similar in length as Type II without the extended wing fillet (and with the extended splitter plate below the intake lip and an inward camber just like the IIb), and Type IIb is a few inches longer than that. On the question of how perpendicular the top of the intake lip is to the airflow, there seems to be some debate on the various drawings. Is it completely perpendicular, or is there a slight angle. The answer is yes and yes. I believe the top lip of Type IIa (similar to Type II) is almost perpendicular to the airflow, while there is a more pronounced angle to the Type IIb. This may be obivious to Voodoo experts, but I was very excited to discover this for myself. The key is Door 70, more on that later... SC AEEH Photogrammetry of the Pima RF-101C 56-0214 with Akira Watanabe's photos Photogrammetry of RF-101A 54-1506/5658 RF-101C Type IIb intake on the left, RF-101A Type IIa intake on the right
-
Thank you Serkan for the kind words. Just doing my best to see what is possible without resin and CA glue. :-) This may get printed in resin eventually, in which case more surface details will be needed as I improve my CAD skills. Still a ways to go. SC
-
These are progress photos from the last week or so. After some sanding. After another coat of primer and sanding, here are my attempts at a NMF for the RF-101C and and ADC gray for the RF-101A. Down to my last can of Model Master Aluminum Plate Buffing Metalizer rattle can, which splattered badly. Will try to salvage. I read somewhere that Light Ghost Gray was close to ADC Gray, so I used Tamiya Light Ghost Gray (AS-26 can) that I had on hand, but it looks too blue/green. I wanted to see if the panel line details can hold up. The forward fuselage is 1/48 proof-of-concept test print with home made decals. SC