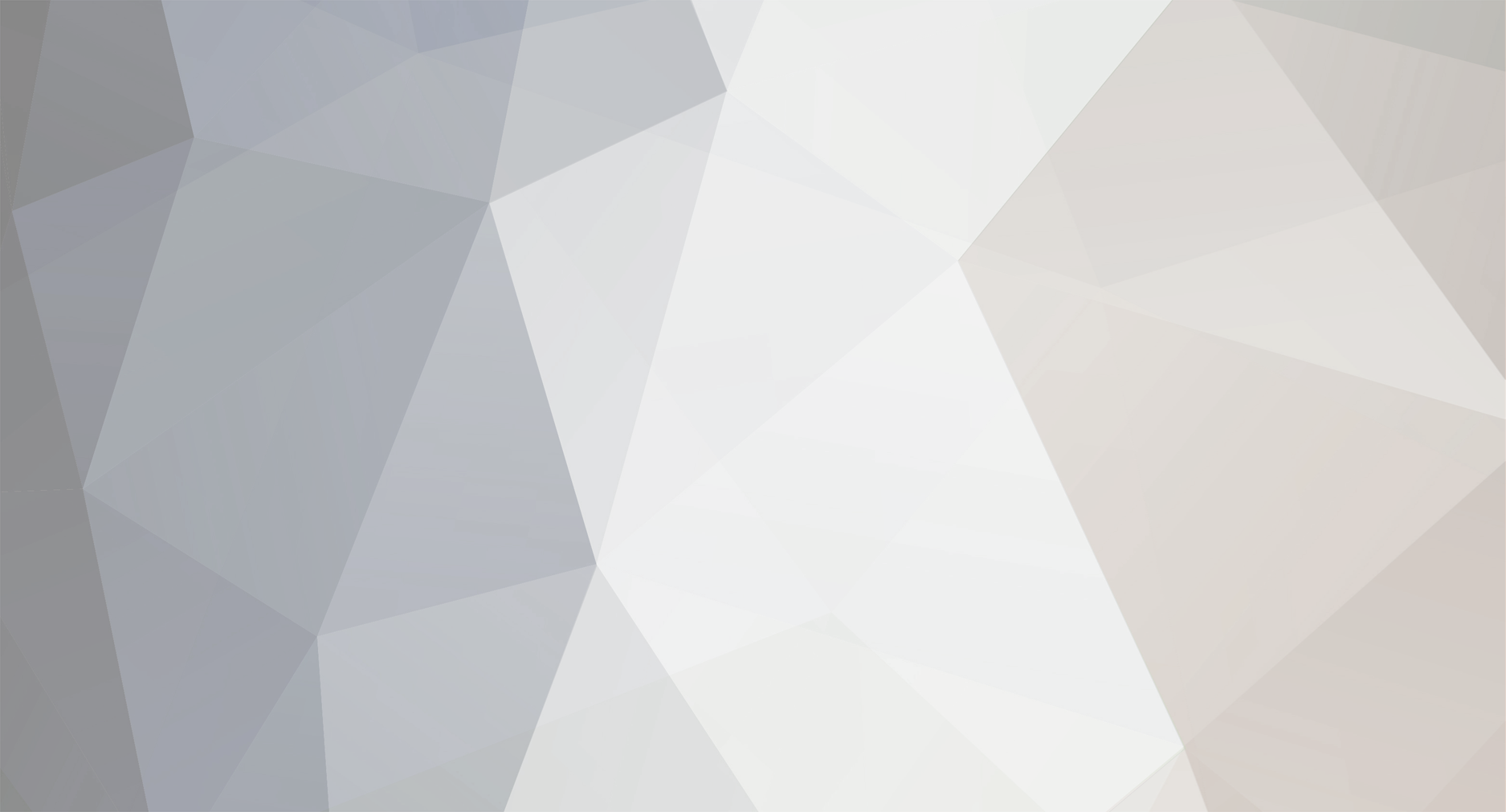
Daniel460
-
Posts
620 -
Joined
-
Last visited
Reputation Activity
-
Daniel460 reacted to Marine104 in Italeri CF-104 Starfighter "Kicked up a Notch": KLP Publishing eBook now Available!
Superb and equally informative modelling Chuck, that gloss black base is just unbelievable straight out of the AB with no polishing!
I've used the 'Hi-Shine' Alclads a few times now and by trail and error I found leaving some for a long cure, over a week or even two, made them much more bullet proof and resistant to masking, no marks whatsoever to which I was pleasantly surprised. Mind, this was with the most durable shades, Polished Aluminium and Polished Steel and over a softer gloss black Humbrol enamel base (the Alclad bonds with the slow curing enamel apparently) and not hard lacquer. I'm not sure this would help however with Chrome or Airframe Aluminium since they are even more fragile. The Airframe aluminium I've used seems to come off just looking at it.
Also, over an uncoated Hi-shine surface, even the relatively weak Microscale products when I used them, just left marks so I had to go on to clear coat before and after decals for protection. Really interested to see how you avoid this annoyance.
Finally, what do you thin X-22 with over the Hi-shine if needed? I like the surface quality that X-22 + levelling thinner gives, however I found the lacquer thinner slightly interacted with the Hi-shine (it is soo thin) and the undercoating lacquer gloss black (GX in my case) when spraying on a wet enough layer, maybe with X-20 it works better IDK. I assume you have tried Aqua Gloss which doesn't react with the paint at all given it is water based but it is very hard to spray without any orange peel, plus it gives this 'plastic' (best way I can describe it) type clear which is questionable for the NMF. Clear coating Hi-shine Alclad is still an unsolved riddle for me!
The rivets look very promising, I think the best solution for the goal. I've tried this briefly but directly over the Alclad (well with a clear coat to protect against decal solutions) and found it difficult to get the consistency as they didn't stick so well, doing it on the gloss black and spraying the Alclad over top is a much smarter and durable way of doing it! Eager to see how this turns out over the model and will try this out.
I blame your build for luring me into just starting an early NMF Luftwaffe TF-104G!
Sorry for all the Qs but keep up the fantastic work!
David
-
Daniel460 reacted to chuck540z3 in Italeri CF-104 Starfighter "Kicked up a Notch": KLP Publishing eBook now Available!
Thank you, thank you, thank you! I have been using pics of the restored CF-104 here in Calgary, that clearly has bulged doors. According to the Military Museum website, this was its history:
"The CF-104 in the Cold War Hangars at The Military Museums made its first flight on the 2nd of October, 1962 at Cartierville, Quebec. It was the 146th CF-104 of the 200 single-seat aircraft ordered by the RCAF to fulfill its NATO commitment in Europe. After several test flights and troubleshooting it was Taken On Strength by the RCAF in July, 1963.
The aircraft was then partially disassembled by removing the wings and the aft section and on December 12, transported by C-130 Hercules to #2 Fighter Wing, Grostenquin, France where it was assigned to 430 Squadron. A few months later #2 Wing was closed and 846 was transferred to #1 Fighter Wing, Marville France where it was flown in a photo reconnaissance role by both 439 and 441 Squadrons.
In March 1967, 1Wing Marville was closed and all assets and personnel were relocated to the new 1Wing at Lahr in Southern Germany. In 1971, Canada sold the aircraft to the Royal Danish Air Force (RDAF) as part of a force reduction as Canada moved from the Photo Reconnaissance and Nuclear Strike roles to conventional operations.
Renumbered as R-846 the aircraft was modified to meet the RDAF air-to-air requirements. In 1984, 846 was retired and for the next 16 years spent its days on display in a museum in Billund, Denmark, then into storage when the museum closed."
It would appear that the RDAF likely modified it, hence the bulged doors. The restored CF-104 in Winnipeg- also with bulged doors- is from Denmark and no doubt had a similar modification.
The Italeri instructions show the bulged doors and the flat doors on Page 31, with no indication which doors are for which version, as they do on other pages. Mind you, some of these instructions are wrong, like which engine cover doors to use on Page 22, so you really need to check your references and apparently the history of the jet!
Cheers,
Chuck
-
Daniel460 reacted to chuck540z3 in Italeri CF-104 Starfighter "Kicked up a Notch": KLP Publishing eBook now Available!
Thanks Derek for the tip, but thinking about it, white spirits would eat the Alclad without a clear coat, which what I'm trying to avoid. BTW, your Thunderbolt is beautiful!
I have no fears of using decals on Alclad, but only if they are clear coated with something like X-22. What they will look like without a clear coat is my concern.
FYI, here are some close ups of the decals on the P-38 using X-22, both before and after decals. You would be hard pressed to see decal film unless you look really hard, like the top of "993" in the second pic:
Cheers,
Chuck
-
Daniel460 reacted to chuck540z3 in Italeri CF-104 Starfighter "Kicked up a Notch": KLP Publishing eBook now Available!
Thanks. The Alclad "lacquers" come in two types. The "Regular" ones are definitely solvent based and etch into the primer coat, which is why they are tougher, while the "High Shine" ones like Chrome appear to be alcohol based and are more fragile. I've used solvent on both of them in the past and they come off easily, so solvent on decals is not an option.
The key will be how good the decals are. If they are thick and/or won't settle down without a lot of Microsol, I will be needing a clear coat. If they are super thin like the ones I used on my P-38, I may be lucky.
Cheers,
Chuck
-
Daniel460 reacted to chuck540z3 in Italeri CF-104 Starfighter "Kicked up a Notch": KLP Publishing eBook now Available!
I have a theory on why clear coats mess with the shine, so the car clear coats may not help. Just a theory, with the caveat that I'm wrong at least 50% of the time. Just ask my wife!
Most of the clear coats I tried are actually quite good at what they are meant to do: Cover the paint with a clear, blemish free and shiny finish, just like the car clear coats. Most of the Alclad metallic paints look like they have tiny particles of metal floating in them, reflecting light like real metal does. I have no idea if it's micro-metal bits or pseudo metal bits, but it looks like metal to me floating around in the jar or airbrush. When I spray Chrome on the black lacquer primer, for instance, it looks a bit dull at first when it is loaded with thinner and other solvents, but as it dries, the shine starts to come through. The thinner is interfering with the reflectivity of the metallic bits in the paint, but as it evaporates, it no longer impedes this reflectivity. Clear coats do the very same thing. The reflective surface is no longer directly on the dried Alclad paint, but above it, so the metallic reflectivity has been diminished, causing a duller looking finish.
Getting back to cars, there are many metallic finishes out there and while they can look shiny and beautiful, none of them look like real polished aluminum or stainless steel, due to the clear coats protecting the paint.
And then again, maybe I'm full of $&#t!
Cheers,
Chuck
-
Daniel460 reacted to chuck540z3 in Italeri CF-104 Starfighter "Kicked up a Notch": KLP Publishing eBook now Available!
Feb 17/21
Just for fun I experimented with a few things, like the Alclad paint color and the HGW decal rivets. Although I have all of the Alclad Aluminum colors including Polished Aluminum, some of the panels on these Starfighters look almost like chrome to me.
So I sprayed the tip tanks with Alclad Chrome and I really like what I see.
While beautiful, there are a few problems with this lacquer paint and high shine as follows:
The “High Shine” colors like Chrome and Polished Aluminum do not respond to masking tape very well, sometimes with paint lift. They sometimes don’t respond to decal solutions very well either. Both of these cautions are from the Alclad website. Any clearcoat to protect the paint knocks down the shine a lot. I have experimented with this using at least 8 different clear coats, including two different Alclad clearcoats, and they all dull the shine. The best of the bunch was Tamiya Acrylic X-22, but even it dulls the shiny look enough that I’d rather not use it unless I have to. If you think a smooth gloss black coat of paint reveals 5 times more imperfections than a flat coat, a high shine metallic coat reveals even more. Slightly rough sanding sticks out like crazy. Removing crap from a metallic coat is hard to do without leaving scratches. While the crap will be gone, the effects of the removal often remain.
Let’s move on to my next experiment with the HGW decal rivets I recently received from UMM. To recap, the bare metal finishes on CF-104’s reveal many, many rivets that are both obvious and numerous like this.
To replicate something close to these flush fasteners, we have two choices: Depressions, like most rivet detail on models, or raised fasteners, which are often too high. Since I need a LOT of them, I experimented with a Rosie the Riveter wheel tool and some HGW decal rivets, albeit slightly raised, that I had in my stash. While wheeled rivet tools can do a great job, they can sometimes take on a life of their own and go off course, creating a mess that’s hard to fix, especially after paint. They also won't go into tight places, so you need to recreate more rivets by hand. Leaning towards the HGW rivets, I ordered these, which are 0.25 mm wide and 0.8 mm apart, or close to 1” apart at 1/32 scale, which is good enough to me. While HGW makes these rivets a bit tighter at 0.2 mm wide and 0.6 mm apart, they are a bit too tight and appear as straight lines, which is not the effect I’m looking for.
So I gave them a try, with initial disastrous results! All the little decal rivets fell off in the water and there was no film holding them. Checking a second pack of decal rivets, I figured out the problem. These decals are covered with a sort of tissue paper to protect them, but also a clear film that holds the decals in place. When I took off the tissue paper on the first pack, the film came with it for some reason, which has never happened to me before- and I’ve used HGW water slide decals many times. I replaced the clear film back onto the rivet decals, but the bond has been compromised and not all of the rivets stick to the film, so I will use this damaged pack for subsequent repairs. Lesson learned: Be careful how you remove the tissue paper!
Anyway with the bulged landing gear doors painted that I’m no longer going to use, I had a couple of good test mules for the rivets and the Alclad Chrome paint. The second pack of decals worked flawlessly as I arranged 6 strings of them in roughly the width I’ll be using on the sides of this model. After letting the decals dry overnight, I gently removed the decal film, then wiped the part with water on a rag to remove any residual glue left behind.
While it’s hard to see in this small photo, the decal rivets are almost completely flat and it’s hard to feel them as raised at all. A rivet wheel would also have a hard time on these curved surfaces. If you can imagine this CF-104 covered with these rivets from head to toe and then painted in Chrome, I think this will look awesome!
I have already applied masking tape to this part, burnished it down, and pulled it off to see if any paint or decals would come off. While a tiny bit of the Chrome paint did pull off, it isn’t really noticeable and the rivets stayed put. So far, so good.
So here’s the painting and decaling plan, subject to lots of changes if things don’t work out.
Apply many, many decal rivet chains to mostly the sides of the fuselage and other places they are prevalent in reference pics After masking off black areas, like the nose and intakes, I will paint the entire model in Chrome After this paint dries for a day and likely after a few paint repairs, I will de-tack some masking tape and isolate several panels and paint them different shades of Aluminum and even Stainless Steel to provide realism and contrast I have several shades of Metaliner water based metallic washes, that I will use to slightly weather and “scratch” the paint by dry brushing instead of actually scratching the paint (as suggested by a few of you earlier). Dry brushing is not only easy, it’s reversible and I’m dying to try a few more colors of these washes that I used on my Tempest build. Full decals, with my fingers crossed that the Chrome can take the Microsol needed to settle them down. I think it can. No clear coat of any kind, but if I have to for whatever reason, I’ll use X-22 as a last resort.
While these decals rivets will take a long time to apply, I am very optimistic that they will look killer on the finished model and really make it look, "Kicked Up a Notch".
Cheers,
Chuck
-
Daniel460 reacted to chuck540z3 in Italeri CF-104 Starfighter "Kicked up a Notch": KLP Publishing eBook now Available!
Feb 15/21
Step 2 of a Gloss Black Finish!
The first coat of gloss lacquer revealed quite a few tiny flaws that I couldn't see on the bare plastic, much more than with a duller finish. A metallic finish will magnify any flaws even more, so now's the time to fix as many as possible.
Back to the drawing board and while I was at it, I sanded the entire model one more time.
Better now....
Seam lines at the rear shown earlier are now gone
This Starfighter kind of looks like an SR-71 when painted black
So here’s how I did it.
Painting a Smooth Gloss Finish
1. Before you paint anything, make sure the plastic is as smooth as possible to begin with. Although I don’t use primers like Mr Surfacer, I’m sure they will help, but I prefer to try and retain as much fine detail as possible without the use of fillers before paint, which is a filler already.
2. Remove as much dust as possible with compressed air.
3. I use Tamiya Gloss Black TS-14 decanted from a rattle can, but the new line of Tamiya lacquers in a bottle like LP1 may be just as good, although I’ve never tried it. After the lacquer has degassed, I add about 1/3 Tamiya lacquer thinner to 2/3 paint.
4. I now use a wet towel underneath my model to reduce static electricity and trap lint.
5. I now also make sure that I only paint in my paint booth with air flow. I’ve tried to paint beside the booth on a table for ease of handling large models, but particles from the air are attracted to the paint as the airbrush creates airflow disturbance. In the paint booth, the airflow works with the airbrush, flushing most crap away from the model and not towards it. I say “most”, because you will always get the odd particle of crap on the paint.
6. Like most painting, the lacquer should go down wet to get the smoothest finish. If the paint is not entirely wet, orange peel is created and if too wet, it will run. You want to be right in the middle of these too extremes and once you have achieved a wet surface, move on. Try to spray continuously as much as possible, so that the tip of the airbrush never gets dry allowing clogging and resultant sputtering. Always spray away from the model first to unclog the nozzle before directing the paint towards the model.
7. Spray close to you at in the beginning and finish at the opposite end away from you. If you spray in the opposite direction, fine paint dust will accumulate on areas that you painted only moments earlier, making it rough.
8. Use a relatively large needled airbrush of about 0.3mm or larger at a flowing pressure a bit higher than normal, of about 12-13 psi. This keeps the paint moving without sputters. While my 0.18mm airbrush works with ultra-thin MRP lacquer paints very well, it chokes and sputters with Tamiya lacquers, unless I really make them thin.
9. Flowing pressures are often misunderstood. When I mention 12-13 psi, this is what the pressure gauge indicates when I’m spraying, not the pressure of the compressor before I spray. For my particular compressor, a shut-in pressure of about 21 psi creates the above flowing pressure, whereas yours might be quite different, depending on size of tank and a host of other considerations.
10. Paint only one side at a time and let it dry for at least 4 hours before even considering painting other surfaces.
11. Large vertical surfaces, like the vertical stabilizer, should be painted on its side at 90 degrees to keep the surface flat.
12. Have a space heater nearby that isn’t too hot and never one with an open flame due to a fire hazard. Once you have finished painting a large surface, move the model close to the heat source to get the paint to flash, so that new dust particles won’t stick to it. This is one of the reasons I like using my simple painting box, which allows me to move the model around without touching the paint
13. While the paint will feel fairly dry after only 15 minutes or so, it really needs about 24 hours before you can handle it with your hands. If you’re in a rush to do some repairs, always wear rubber gloves when handling the model.
14. After the first coat of paint has dried for 24 hours, you can sand and do other repairs, always leaving smooth edges to the paint with no sharp edges. Re-spray the model as required.
15. After this second coat of paint, which may be the last, spray a flash coat of 100% Tamiya lacquer thinner over the entire model, allowing it to dry a bit before moving on to new areas. The thinner partially dissolves the paint underneath, allowing it to lie flatter and smoother. You want the surface just wet, then move on, trying to avoid any puddles.
16. When this coat has dried for 24 hours, you will still have the odd piece of crap in the paint that you can lightly sand off.
17. Assuming the above sanding did not go down to the bare plastic, spray the model with 100% Tamiya lacquer thinner again, which will smooth things out without the need for additional paint.
18. Let the model dry for about 48 hours before you handle it too much again. While you can handle it for shorter periods above since you are continuing to do repairs, you want this last coat to be hard enough that finger prints are not created with oily hands.
DONE!
Cheers,
Chuck
-
Daniel460 reacted to Derek B in Italeri CF-104 Starfighter "Kicked up a Notch": KLP Publishing eBook now Available!
Hi Chuck,
loving the tutorials (even in my 6th decade, I am learning new things, so thank you).
I discovered something (by accident) back in 2004 which may help you, but may require more experimentation on your part?
As an experiment of my own, I wanted to make a model OOB that could be used to try my first attempts at covering a model in normal kitchen grade metal foil. For this, I chose the Revell 1/72 P-47D Thunderbolt kit - the reasoning being that if I could successfully completely foil that kit, then logically, there should be nothing else in any scale that I could not foil!
Anyhow, it was successful, which was good:
The (accidental) discovery occurred whilst I was applying the kit decals to the foil. I used Micro-set and Micro-sol to apply the decals, which worked well, but the edges of some of the decal film picked up dirt or looked a bit scruffy. Not knowing any better, I used a cloth damped with white spirit to clean them and found (initially) to my horror that it dissolved and removed the decal film completely! The discovery bit was that it actually left the decal design and colours intact on the model - it only removed the decal varnish film.
This now left me with a model which had decals applied that looked like they had been painted on (I think that the Micro-set and Micro-sol helped here) the bare aluminium with no decal carrier film in sight! (I used a mix of acrylic matt and gloss varnish to provide a satin finish to protect the decals).
I don't know if this would work with other brands of decal or finish, but I would love to know?
Good luck
Derek
-
Daniel460 reacted to Christoffer Lindelav in Italeri CF-104 Starfighter "Kicked up a Notch": KLP Publishing eBook now Available!
Thanks for the great tutorial. I really should print it and put it on the wall of my mancave for easy access when doing some painting.
Cheers
Stoffe
-
Daniel460 reacted to chuck540z3 in Italeri CF-104 Starfighter "Kicked up a Notch": KLP Publishing eBook now Available!
Thanks Guys! If you have any questions, fire away.
Short answer is no. Like all airbrush painting, it's a lot of trial and error with viscosity of the paint, pressure of the air flow, humidity, temperature, etc. The only way I can describe it is to put down a bit more paint at slightly higher pressure than you normally would with thinner paints- maybe 10-20% more of both. If the air pressure is too high, the turbulence will cause dusting of paint particles some distance from where you are spraying, while too low will cause sputtering.
The other tip (just added above) is to spray continuously as much as possible, so that the tip of the airbrush never gets dry allowing clogging and resultant sputtering. Always spray away from the model first to unclog the nozzle before directing the paint towards the model.
A few more examples....
Cheers,
Chuck
-
Daniel460 reacted to chuck540z3 in Italeri CF-104 Starfighter "Kicked up a Notch": KLP Publishing eBook now Available!
I would be very interested in your results. Right now, the Tamiya Gloss Black from a rattle can works for me as shown below!
I had not noticed that before Don, but even if I did, there's no way I was going to move that complicated latch mechanism. It's not really too bad anyway, but thanks for pointing that out.
Feb 14/21
Before painting the fuselage, I noted that there should be a protective plate for the arrestor hook over the drag shoot door, so I installed one from my spare PE collection. According to the DACO book it is offset from center, just like the hook.
In most of my builds I show off my modeling box, which has served me well for many years and was used on just about every model I have ever built, from my small Harvard to my big F-15C Eagle. Besides being almost free, what I like about it the most is that the pipe wrap is gentle on the model and pressure points are more evenly distributed than some of the contraptions I see used by other modelers.
To make it even softer and help reduce dust, I cover it with microfibre towels and on my Tempest build I discovered that spraying the towel with a light mist of water reduces dust when painting, which is critical if you want a dust free and glossy finish of Tamiya Gloss Black lacquer (TS-14). I use this paint as a primer for Alclad, but also as a “check-coat” to look for flaws.
Small flaws like seam lines that were not filled properly are revealed, which I will fix before painting with several shades of Alclad. There are lots of other small flaws as well, that you might never see with a flat paint finish.
Overall, I’m pretty happy with this first coat of paint and thanks to the wet towel, dust and other crap is minimal. A bit of a walkaround….
I will knock down the shine on the top of the nose area later.
A few bits of crap here and there, but not many....
After lots of clean-up and sanding, I also painted many other parts that will also be aluminum in color.
After lots of trial and lots of error, I have finally figured out a method to apply this paint easily, so I will do a write up of how when I have a bit more time.
After this lacquer dries for another day, I’ll go over every square inch of it and repair flaws and sand off contaminants. After that, it will be the application of a few thousand HGW wet transfer rivets!
Cheers,
Chuck
-
Daniel460 reacted to chuck540z3 in Italeri CF-104 Starfighter "Kicked up a Notch": KLP Publishing eBook now Available!
February 11/21
Enough of cold temperatures! We Canadians are supposed to be tough in the winter, so I did a little painting after all. Not much, mind you, but enough to help speed things up when it warms up a bit.
Before I started painting, I need to decide on a subject that was limited by the decals I had on hand, what I liked and what looked a bit different. Almost all bare metal versions of CF-104 models have a red tail and other red markings which are cool, but I think a bit overdone if I want something different. I also found that most of the pics I have of CF-104’s serving in Germany had white tails, so I decided to go with that instead. I don’t like the kit decal scheme that much either, but thanks to Rockie Yarwood’s donation of Belcher Bits decals to me a few months ago, I can go for a “CAF” version for many serial numbers, as long as those numbers aren’t repeats, since I have only 2 of each number for both sides of the model. As a result of all of all the above, I’m going with 104743 that looks like this at the front. I am also going to add a MN-1A bomb dispenser to the center pylon as shown here, which is a shortened version of the SUU-21 dispenser I bought from VideoAviation.
I don’t have a pic of the whole jet, so I’ll use this pic of 104788 for the rest. Again, two “8’s” in the serial eliminated this subject. Note that it also has the bomb dispenser.
Since the surface areas were small and light colored, I painted the wings, horizontal stabilizer and nose cone first since they will need to be masked off, maybe for months, for the bare metal finish that will dominate this model. This paint can now dry for the next few days before the weather warms up and serious painting begins.
The top of the wings are supposed to be flat white so I used MRP-004 White, which sprays beautifully, but the coverage is terrible. After 5 coats I gave up and used Tamiya TS-26 Gloss White lacquer instead, which will eliminate the need for a gloss coat before decals at the same time. Like all the Tamiya lacquers, they are a bit tougher to spray than MRP paints, but the finish is second to none. This is what I will also be spraying in Gloss Black as a primer coat for the Alclad finish. Ailerons and front flaps were left off for ease of painting and fear of breakage during assembly and painting.
One thing I discovered when reviewing many pics of the real deal, is that the white paint does not go right up to the wing root, but back a bit, leaving a notch of bare metal, while the front flap is white right up to the fuselage. For example, check out the first pic of this build thread. FYI if this was always the case, this was missed on the restored Starfighter here in Calgary, while the one in Winnipeg is painted correctly.
Same thing on the bottom of the wings, which are FS 36473 Sky Grey, MRP-242, which is a greenish grey. It’s a bit hard to see in this pic since the paint is almost the same grey as the bare plastic. If I did this model again, I’d leave the main landing gear bay bare plastic and paint it with the rest of the bottom, since they are both metallic Aluminum. The open gap where Part 9C has been left off was filled with foam, to help avoid overspray getting into the cockpit area, just in case.
The horizontal Stabilizer is also flat white, but both top and bottom. Again, I used Tamiya gloss white, which I will knock down the shine on later after a few decals.
The sides and bottom of the nose cone are also FS 36473, but I didn’t mask off anything to avoid sharp paint edges later. Note all the effort to mask off the cockpit and avionics bay area, which took a long time to do cleanly and hopefully totally sealed.
In the background I’ve put the wingtip tanks together and cleaned up landing gear doors and other parts to save time later. As always, lots of cleanup required. Hopefully my next update will be a super glossy black jet in preparation for many shades of Alclad.
Cheers,
Chuck
-
Daniel460 reacted to Troy Molitor in Italeri CF-104 Starfighter "Kicked up a Notch": KLP Publishing eBook now Available!
Woke up here in Memphis and were under icing conditions. Great to look at but you can hear trees all moaning under the added stress. I went to the post office earlier and saw several tree limbs down and a few actually falling while driving close by. The magnolia and pine trees seem to be taking this added weight especially hard.
And Thank you Chuck for sending down that wicked polar vortex! Your comment made me smile. True!
-
Daniel460 reacted to chuck540z3 in Italeri CF-104 Starfighter "Kicked up a Notch": KLP Publishing eBook now Available!
I've been waiting for someone to mention the "Polar Vortex". The media in the last few years has claimed that global warming has caused the jet stream to wobble, allowing brutally cold air to drop to the south, creating this "new phenomenon", brainwashing the public. Poppycock! When I was a kid about a million years ago, we had 2-3 bouts of -25 C (and colder) events that would each last for weeks every winter. Global warming isn't causing what we have right now. Due to global warming, we have less of these events each year, despite the new media label for it.
Back to painting (before I get political!), I learned long ago that painting in my cold garage can actually work out very well for 3 reasons:
I can get a wet coat easier since the paint isn't warm enough to dry too quickly. I use lacquers and enamels exclusively, so acrylics may not work as well. I have a nearby space heater and when I'm finished a light coat, I hold the model near it, drying the paint when I want it to dry and not sooner. Our cold air is super dry, so when I use a space heater the paint dries almost immediately.
These painting sessions are usually quite short- maybe 5-10 minutes, after which I bring the model indoors to let it dry properly in warmer air. When dry, especially with MRP quick drying acrylic lacquer, I might go back out for subsequent coats and touch ups only 30 minutes later. Thanks to our long winters, every single model I have ever made has been painted in my cold garage this way.
Cheers,
Chuck
-
Daniel460 reacted to chuck540z3 in Italeri CF-104 Starfighter "Kicked up a Notch": KLP Publishing eBook now Available!
PM sent Gord and thank you so much! I was really looking forward to photographing that bird for this build, but as you know thanks to Covid, the Cold War hangers are closed. SO disappointing, but your pics might be just what I need. As above, what I am most interested in is the positioning of the thousands of rivets on the fuselage. I'm going with the HGW wet transfer decal rivets, which I think will look the part.
I got the nose cone on which was no easy task. The plastic is very rough and the sprue attachments damaged the edges. Thankfully the cone is a bit too big, which allowed my to sand it a LOT! All good now, with some fastener detail added according to references. For those who might be wondering, the radome goes all the way back to the base of the windscreen where you can see the two latches on the top.
With the nosecone on, this model has blown through the confines of my small photo booth that I use to take all my detail pics. I guess I'll just have to put up with it until I finish the model and get it into my bigger photo booth, which is a real pain to set up and take down.
Cheers,
Chuck
-
Daniel460 reacted to JayW in 1/18 Scale Blue Box F4U-1A Corsair Modification
A while back I stated I would be doing some limited cockpit work and then closing it up for a long period while I did the inboard wings. Well, I am finding there is a whole lot of cockpit work that can be done before I go to the wings. Here is another cockpit update:
The horizontal beam on the Sta 186 bulkhead (that I cut in half) is fragile and easily catches on things like my sleeve or a fumbling finger. So each side needed some reinforcement. The LH side was reinforced by the side console (sort of). The RH side needed something so I took a break from the LH side and did up the O2 bottle and its support stand:
You can see it somewhat reinforces the beam. Hard work - almost entirely because it snugs up to the side wall and the side wall on this model is grossly out of scale due to its thick gage. A layout helped, but I can only approximate the local contour so I have to resort to a bit of trial and error with the bracketry. The bottle itself is acrylic and turned on the mini-lathe, and is something like 0.2 inch shorter than it should be to clear the aforementioned sidewall. The hardest part was the straps just due to very small details. As you can see I chose yellow for the color; some of you would probably have chosen green. Pressurized bottle colors for WW2 aircraft is an interesting subject with many opinions.... When I get to the RH side, this bottle will be plumbed to the familiar O2 regulator and its long flex hose.
And then it was back to the LH side, where I will be for a good while longer. Gadgets galore! Next to the seat are two details that need to be there even if largely unseen. One is a pulley bracket support shelf, and the other is a truss/bracket structure that supports the CO2 bottles and also the hydraulic hand pump. It is a good example of a poorly designed afterthought of which the Corsair has many examples (IMO). I provide pictures from the parts catalogue to help describe.
First the pulley bracket support shelf (for aileron trim cables, tail wheel lock cable, and wing hinge pin lock cable):
And the CO2 bottle and hydraulic hand pump support bracket:
And my versions of these details:
Not perfect by any means. But once I get the bottles in there and tighten the cables (fishing wire), it should look the part. It will probably take a flashlight to see them once the cockpit is done and the seat is installed. That truss/bracket thing was a major PITA I can tell you! Lots of tweezer work on small parts, and trial & error trimming.
Next post you will see the CO2 bottles and their very interesting cradles, and the hydraulic pump. Take care!
-
Daniel460 reacted to JayW in 1/18 Scale Blue Box F4U-1A Corsair Modification
So where am I? To review, I am trying to get as much done in the cockpit as I can before the bottom must be joined to the sides. The bottom, as I have stated before, is the wing center section. Sooooo, if I am to join that to the fuselage in order to complete the cockpit, the center wing itself must be completed - a huge job (LG bays, and the wing fold if I choose to try it). A sequencing nightmare of sorts.
So I have been concentrating on the LH side of the upper cockpit for quite a while now, and I have some progress to show you. Last post I said that the Sta 186 bulkhead (seat and armor plate bulkhead) needed to be there in order to stabilize the side console. Here is the bulkhead, already fabricated and installed into the fuselage, including the horizontal beam that the seat and armor plate attach to:
You can see the fittings for the seat frame attach. Also note the chord flanges protruding aft in that first shot. That will aid in joining the aft fuselage when the time comes. So I glued the horizontal beam to both bulkhead halves after gluing each half to its respective fuselage half. This assured a good level orientation. Fabbing the bulkhead details to closely match the inner contour was no easy thing. As is usually the case, laying it out took more time than making it. All the parts you see are of course made from plastic sheet or rod or angle stock. But now, I had to disassemble the fuselage again. To do this I cruelly snipped the horizontal beam in two:
I will join the two beam halves back down the road. It won't be visible at all - it will be behind the armor plate. Now to get back to work on the LH side. It was time to get in some more bracketry, and then finally the aux panel and side console. Voila:
On top, you see the canopy rail structure, all finished up with its support fittings at each frame, and the detent plate lying on top. This allowed the canopy to be slid back to any of several partially open positions. Just below that is the engine control quadrant mounting bracket, with the horizontal bend in it. The quadrant itself is coming soon. And below that of course is the freshly installed LH side console and all its gadgets. Forward of the side console is the LH aux panel, also freshly installed.
Time to see what this cockpit is starting to look like:
There is SO MUCH MORE TO BE DONE! Stick with me - it's going to be a long and interesting journey. So far so good.
-
Daniel460 reacted to JayW in 1/18 Scale Blue Box F4U-1A Corsair Modification
Well - a bit of a milestone. The very complicated side console (LH side) is done, as well as the LH side auxiliary instrument panel. Many many "doo-dads" had to be created. Nothing too fancy; just using rod and strip, measuring, trimming, filing, sanding, drilling, painting - all under heavy magnification. An example (two gun charging cylinders, a landing gear control quadrant, and a hydraulic valve that mounts underneath the side console:
Here is the LH side aux instrument panel which will soon be installed. I have identified the features:
And the LH side console:
My gosh I thought I'd NEVER finish these things. So much to it! There are three versions of the console - one for the birdcage Corsairs, one for the earlier -1A's, and one for the late 1A's and D's. My aircraft gets the middle one, and the assembly and installation drawing was too faint to be read. But the equivalent drawings for the early and the late versions were much better. So I had to do a heckuva lot of research with the part catalogue and photos to come up with the right stuff. For instance, that silver bomb release quadrant is a government issue unit used on the -1's and early -1A's, but was replaced by a Vought designed unit on the later models. Similar configuration difficulties with the aux panel.
Here is a shot of both components roughly positioned:
It's going to be just fine. Don't you worry! Oh BTW - I am very happy with my decal sheets from BareMetalFoil. They behave pretty darned well for inkjet decals.
I have decided that the best way to go forward from here is to make the Sta 186 bulkhead, which is the bulkhead the seat and armor plate is attached to, and which is the aft closeout for the cockpit. I will split it in half - a LH half and a RH half.
Take care; I'll post soon.
-
Daniel460 reacted to JayW in 1/18 Scale Blue Box F4U-1A Corsair Modification
Happy New Year LSP friends. I have managed to put in at least a little time on the Corsair project every day or nearly so. And it's time to post something so that y'all don't think I have just given up. Progress seems slow. But here's the thing. I am scratch building a cockpit in 1/18 scale - the most complicated cockpit I have ever attempted (second toughest was my P-38), mostly due to three things (sorry if I sound like a broken record). One, the Corsair doesn't have a floor, which exposes a ton of detail in the bottom of the fuselage that would otherwise be unseen (and unmodeled). Two, the cockpit walls of this model are on five different parts (left fuselage, right fuselage, lower fuselage, upper wing half LH, upper wing half RH), making attachment of components challenging. And three, the Corsair is chalk full of rube-goldberg gizmo's. And it is those gizmo's that take alot of time and effort. They also leave me wondering just how far I need to go. When I look at some of the cockpit efforts you guys have done (talking to you AirScale), I feel the need to shoot for the moon. Yet other smaller 1/32 efforts leave stuff out yet still look very convincing.
First - it is time I selected the aircraft I will model (the Bu number). Why? Because I am constantly having to decide what configuration part to make. Like all warbirds, and especially the Corsair given its teething issues early on, and all the other improvements it received over time, things changed. So here it is:
This is VF-17 (the Skull and Crossbones Squadron, or the Jolly Rogers) F4U-1A Bu No 55995, Vought line no 1636, #29. The pilot was Ira Kepford who was a rather famous and successful Navy pilot.
I like this aircraft because I can duplicate the paint scheme and make decals relatively easily, plus it represents a fairly famous (or notorious) unit. And it is indeed a -1A with the partially framed canopy which the model came with. Many have modeled this aircraft, so lots of info out there. When the time comes, I will be challenged with the triple colored paint (light gray bottom, light blue middle, darker blue top) that all Corsairs had at that time.
Ok, the cockpit. I have had a bit of a decal disaster. Many months ago I purchased yet another set of Model Master decal papers, only to use one sheet leaving several more sheets for the next project. Well - with time for some reason the decal one creates on this paper loses its ability to slide off the backing. Even if I increase the soaking time. Here are the decals I have made so far for the cockpit:
I mean, they are very representative of the actual placards in the airplane. But when I cut them out and attempted to apply, they would not free themselves from the backing, and self destructed. GAH!!!! So, I am fed up with the Model Master decal kits. And I am going with another brand "Expert Choice" by BareMetalFoil. Still waiting for them in the mail, and that is holding up some of my progress.
In the meant time work progresses on the LH side to include the forward LH auxiliary panel and the side console (shown with the failed decal sheet before failure):
Positioned on the LH sidewall:
For these parts, I spend hours and hours researching their details, deciding how to build them up and with what materials, and laying them out on paper usually about 4x size. The actual fabricating of the parts takes less time than all that research work!
Anyway - not too impressive I know. That side console you see there is going to get ALOT more complicated. I think you will like it. I really have a tiger by the tail with this cockpit.
Hope to post more progress soon. Take care, and stay healthy.
-
Daniel460 reacted to JayW in 1/18 Scale Blue Box F4U-1A Corsair Modification
A small update. Having some fun here with the surface control components. In these pictures you will see the pushrods that go from the elevator tube to the wings, and the control stick attach:
The control stick lacks the pistol grip, and is only temp installed. It's too long and fragile to leave there with all that is left in the cockpit (like 90% of it!). But I felt I had to at least install the yoke that it attaches to, while the joint is still accessible. The unoccupied lug you see on it will one day accept a pushrod going aft under the pilot seat, toward the tail of course.
Here are the aileron pushrods. Difficult to make because the joints are so small. The main part is 2 mm brass tubing, truncated of course where they are not seen. They are situated right behind the "zig-zag" bulkhead like so:
Having fun. Take care!
-
Daniel460 reacted to JayW in 1/18 Scale Blue Box F4U-1A Corsair Modification
After the engine, I breathed a big sigh of relief, and then just couldn't figure out what to do next. I know what needs to be done next - the cockpit. And I guess that is what I will do. But one thing leads to another. The side walls need to be done first, especially important for the Corsair which has no floor, exposing the fuselage frames on the sides and bottom. Right now it all looks awful and unrealistic. So while doodling around wondering how to attack it, I started on the wing center section front spar. Just....because.
OK the center section wing front spar, or main beam in Vought language. It is very visible in the engine compartment with cowl panels open:
And of course there is an engineering drawing VS-10072 - here is one frame of it:
Two tubes (one left, one right) of the engine mount truss attach to the front spar common to its lower chord. Due to the heavy gage of the gull wings on the model (.08 inch scales to 1.44 inches!), the spar is narrower than it should be, which affects the location of those two tubes, which will cause interferences. So I had to modify the shape of my spar, flattening the bottom. This 4x scale layout (that is to say 4 x 1/18) shows what I am talking about:
That layout looks simple, but it is not! I did alot of hours of layout work trying to get a spar that was the right shape, and located fore/aft in teh right place. Here she is - just alot of plastic sheet, strip, and angle section:
Making it was alot easier than laying it out! The two little pads with holes are where the motor mount truss attaches.
These pictures show what it will look like when installed (the trained eye will notice I got the dihedral wrong - but fear not. It's gonna be OK):
That last shot is from the bottom. Note I have created "shoulders" for the big lower hinged door to nest up against (it's aft edge).
I am going to have to rely on this spar section to maintain wing dihedral as I continue to dremmel away material from the part, making it more limber and flexible. So I will install it permanently here real soon.
Take care - next post I'll show you some progress in the cockpit area.
-
Daniel460 reacted to JayW in 1/18 Scale Blue Box F4U-1A Corsair Modification
All right. A large milestone - the R-2800-8 is finished and on static display (my apologies for the crude mounting fixture). A nearly year long adventure:
Some lines were installed after the rear crankcase was installed - a large fuel hose from the fuel pump to the carburetor, and some tubing associated with the separator (the ZC yellow cannister on the side of the aft blower case):
With exhaust manifolds and the diaphragm:
When this piece of work gets installed into the aircraft, it will be a huge challenge to connect the myriad tubes, hoses, push rods, cables, and wire bundles to it. Oh, and the complex shaped air ducts. Wow. But that is going to be a while.
Tell you the truth - I am not sure what I am going to tackle next. The cockpit looms large, as does cowl flaps and nose cowl attachments, as does the engine mount truss. and firewall bulkhead. I guess next post you will see. Take care.
-
Daniel460 reacted to JayW in 1/18 Scale Blue Box F4U-1A Corsair Modification
OK, so last post I showed this basic lathe-turned, and milled chunk of acrylic which was the start of the rear crankcase of the engine:
This section of the engine is basically the accessory drive gearbox, and boy is it full of "accessories". It is also the place where the starter motor is mounted, and the input area for fuel and oil. It is supposed to look like this:
Gulp. Well you just have to attack it one step at a time. And, this picture shows only the basic engine and none of the componentry that is mounted to all those mounting points! Thank goodness AirCorps Library has an illustrated part catalogue of the R-2800-8, 8W, 10, 10W engines (which are the specific types for the Corsair and Hellcat). What a vital part of my research. That plus other specs of components and standards that can be found at AirCorps, plus some poking around the internet, and was able to fabricate some representation of each part of the rear section including accessories, with a minimum amount of guesswork.
Here you see the laborious work part way through (actually most of the way):
Accessories are sprouting like buds on a bush. In the foreground are the starter motor (left) and the clutch selector valve (right). The starter motor is a brass lathe turning with plastic add-ons. The rear crankcase in the back has many components on it already, all made of plastic shapes, and many many Meng nuts (I am going to have to order some more).
And eventually - voila! The finished rear crankcase with everything on it that I could make and mount, at least with it separate from the rest of the engine:
There is so much here that I have attempted to label it all, for those of you who are interested:
Next post is coming soon. It will be for a very large milestone, the complete R-2800-8 engine from stem to stern, something I have been working on for nearly an entire year now. Stay tuned please! Thanks for your patience.
-
Daniel460 reacted to JayW in 1/18 Scale Blue Box F4U-1A Corsair Modification
Ok the "intermediate rear crankcase":
Similar to the intermediate stage supercharger section already described, this piece started out as a lathe turning, and then a bunch of plastic add-ons. I don't have any early-on pictures as they are so similar to what I already described. But here are some pics of the basically finished part:
The large white flat area is where the "rear crankcase" will be mounted. The round white flats are for mounting of the aux stage air exit ducts. Wahoo!
And attached to the intermediate blower stage:
See that weird looking circuitous rectangular section pipe running horizontally on the near side of the assembly? That is an oil passage pipe:
Here is what the engine looks like so far:
Coming right along. The last remaining section of the engine is the rear crankcase:
This is also a lathe turning that starts out round:
...and then gets alot milled off:
Until it looks like this:
So much has to happen with this part! You will see that next post, so stay tuned!
-
Daniel460 reacted to chuck540z3 in 1/18 Scale Blue Box F4U-1A Corsair Modification
I am often bewildered how you and Peter Castle create such great parts, while the rest of us mortals are just gluing together the parts we find in the kit box. Like Peter, your research, problem solving and execution is so much fun to watch. Your engine looks fantastic!
Cheers,
Chuck