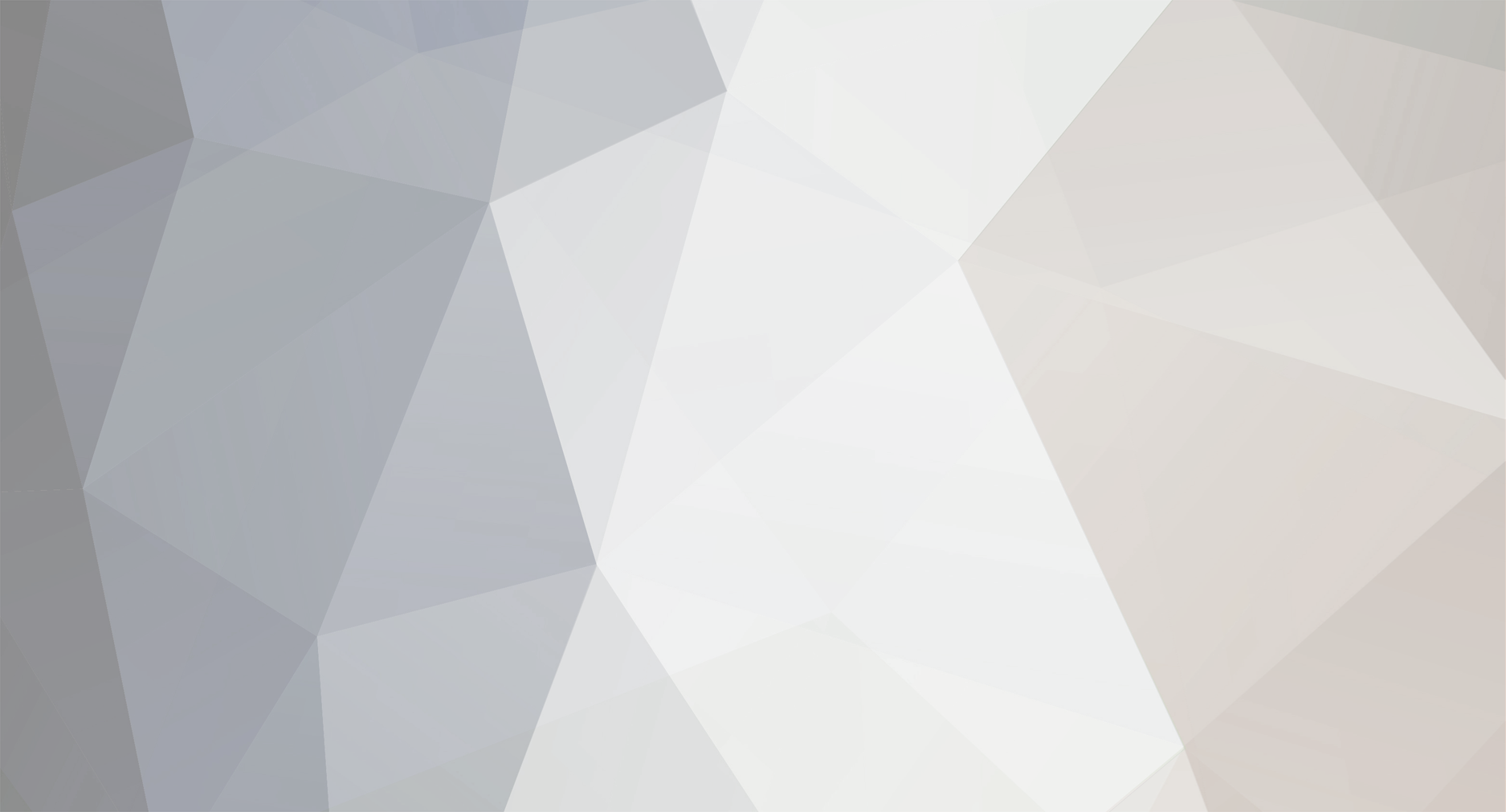
JayW
LSP_Members-
Posts
1,960 -
Joined
-
Last visited
-
Days Won
19
Content Type
Profiles
Forums
Events
Everything posted by JayW
-
Wohoo!!!
-
The panels are butt joined, so smooth. And yes most if not all panels would have to be stretch formed. It would be fun to see what the government paid for an F4U versus a F6F.
- 1,636 replies
-
- scratch building
- corsair
-
(and 4 more)
Tagged with:
-
Look and behold - from the fuselage lines drawing VS-10201: It shows a birdcage version, but the later blown canopy types share the same panels a few frames aft of the canopy. The belly is curved too. I am going to have some more issues with this mid-section fuselage skinning.
- 1,636 replies
-
- scratch building
- corsair
-
(and 4 more)
Tagged with:
-
Yes, am familiar with the Willow Run miracle. Actually, industries around the USA mobilized during WW2 in ways few thought possible. Books have been written WRT how such a mobilization was managed by the armed forces. Another miracle. How the hell did Goodyear get a contract to make F4U's? Packard built RR Merlin's. So many unlikely examples (although the Packard Merlin wasn't so unlikely really). Amazing times.
-
Hah!! With an R-2800! What are you going to do about that? The P-40 flaps are really something. No lower surface....shakes head in amazement.
-
OMG!!!! Such variation!! Did the B-17's vary that much I wonder?
-
Like minds think alike. I thought that over too. So that middle seam is imperfect. If you think about it, on a humped crown, a single curvature panel wants to see-saw over the hump. That is why I could not get both ends of the original panel to conform to contour at the same time. When I cut the panel in half, the hump was greatly reduced. Halve the length of the panel, and the "hump factor" (height of the hump over length of the panel) reduces by much more than half, but not zero. Draw a circular shaped hump, take a length of the arc, measure the height of the hump, then half that length, remeasure, and you'll see what I mean. That's why I halved the panel. What the two panels do, essentially, is see-saw on their own only to a lesser extent. But still a "wrestling match". When pulled down to the crown (with CA glue!) the lower matching corners of the two panels want to jam together. So a good bit of trimming is required to eliminate that jam. My trims are not perfect, and the seam is not perfectly flat. I can sand it more but already there are a couple of small places where the .005 skin is completely gone. So I have little confidence that I can make that seam go away even if I putty it over. I suspect it just won't be as smooth as it needs to be. So, that being the case, leaving the seam there seems the better option. Let us all embrace the imperfections in my skinning.... Still thinking on it though. Thanks.
- 1,636 replies
-
- scratch building
- corsair
-
(and 4 more)
Tagged with:
-
For eagle. That is a very appropriate analogy!
-
This is effin' cool! I have not seen a large scale Sterling ever before. And your matter-of-fact descriptions of your scratch building are inspiring. Come on - there has to be some difficulty in this! I'm heavily involved in a 1/18 Corsair and it's been, and continues to be, one challenge after another!
-
Like he said - more to come. Fingers crossed John! So far, so good.
-
Last post I stated that in order to provide a smooth surface for the empennage fillet fairings, I need to putty over the area where those fairings will lay down. That is how Airscale does it, and he's right on. But in order to do that, all the skin panels that are in that area must be present. And there was one panel missing, which is a crown panel whose aft end is underneath the leading edge of the fin, just barely. Well don't you know that panel is the largest by area of any panel I have added to the model since I started skinning it! Here is a picture of it from the fuselage top drawing: Took more than one frame to show it all (red outline). Note the aft end is underneath the fin fillet fairing. So off I went laying it out on paper 2x size, and then on a sheet of litho with tape: What do we see there - The penetration on the left just off the centerline is for the antenna mast we discussed ad nauseum a while back. Just aft of that in the middle of the panel is another penetration for the "section" light. Why is it called a section light? And then the two holes furthest aft, one LH and one RH are for hoisting provisions. They will get cover plates later. Many aircraft have this feature. It began to occur to me that I had better do a test panel (good thing I did). This aft fuselage is not straight. It is a tad "humpbacked" which makes the panels compound curved if only a little. But this panel is so large, and it curves so severely over the crown, that fit-up problems might arise. I already had some of that with the forward fuselage on the larger panels. Not good. It was easy to do a test panel: Use masking tape and pencil to trace the outline from the model, place the tape on a piece of litho, cut it out and burnish some curvature into it. Using very stout packing tape, I attempted to get this panel to lay down on contour, and it just refused to do so: You cannot burnish that out. Tape down the forward end, and that is what you get at the aft end. Tape down the aft end, and you get something like that on the front end. Force both ends down, and the sides splay out and wrinkle. And this after having such an easy time with the tail cone, the part I feared the most. OK what to do. Switching to annealed material might help some, but I know from experience, it too has problems with that amount of compound curvature over a large panel. And annealed material just shows so much imperfections.... Didn't want to do that. So I decided to try cutting the panel in half. I just hate it, but that is what I did. First I cut the test part: And taped it down: Much better - I can work with that. Did same with the "production" part: I selected the split location at a bulkhead, where a skin joint could have been anyway if the Vought engineers had chose to do so. I just added an extra fastener row. Ready for forming and bonding: So pretty! And then the WWF wrestling match began. Several hours of high intensity burnishing and rubbing, burnishing and rubbing, trimming, sanding, applying CA at the edges that just would not cooperate, cursing, trimming some more, applying more CA. Finally I got this: The LH side came out better than the RH side, who knows why.... That dent? A mystery. No doubt something left over from the brawl. So this Corsair has a skin joint that isn't supposed to be there. OBG is going to chime in and remind us that the dent is just fine - that aircraft skins of the day just were not perfect. And I will agree! I have to! Or, I might apply a touch of P-38 to it - after all that is what it is - body putty. Not a real happy camper right now. Next post is going to be all about P-38 application and the first of the dreaded fillet fairings. Wish me luck!
- 1,636 replies
-
- scratch building
- corsair
-
(and 4 more)
Tagged with:
-
Well John - I have seen your repairs before and they turn out perfect. I suppose this will too. But as many builds as you have done what do you think happened here? What's different?
-
Yikes - you are a courageous modeler.
-
Thinner! 0.005 inch.
- 1,636 replies
-
- scratch building
- corsair
-
(and 4 more)
Tagged with:
-
Great work on the tail feathers. Timely too - as you know just did same on the Corsair! I'm really surprised and heartened that the decal strips stayed put. You are fearless.
-
Hey Craig - a bit of a sore subject. Well, not really. I know perfectly well that this build deserves to have a good convincing skin surface so I had to do something. It has however lengthened significantly the duration of the build, getting on 4 years now. And it has introduced the dreaded paint lifting. Very concerning! Metallic skins however can be very very convincing. You should know - you have done some pretty impressive acreage yourself. I have very difficult skinning yet to do. Stay tuned for continuing adventures.
- 1,636 replies
-
- scratch building
- corsair
-
(and 4 more)
Tagged with:
-
My word!!!! What a gigantic project! I love Sterlings. Following.
-
Continuing on with the build..... For quite a while I have been anticipating (maybe better - dreading) aluminum skinning of the aft fuselage and tail. It is now time. First among my concerns was the tail cone. Second the h/stab and fin fillet fairings. Other concerns but those are on the top of the list. The guy who performs magic in this arena is Airscale (Peter Castle). Others too, but Peter is the best of the best I think we all agree. So he has provided some guidance to me, which is really just some further explanation of what he has done on his P-40 and P-51 builds, and a couple of videos he has done over the years. Thanks Peter! So I am starting at the aft tip, and moving forward for the most part. Here I provide views of the engineering drawings of three panels I have made: Upper tip VS-19500: Lower tail cone VS-17619: And aft fillet fairing (H/stab) VS-15224 (LH and RH): Here is the aft end prior to skinning, for comparison: Here we go - lots of trimming, burnishing, and tapping with a ball peen hammer to get a shape that annealed aluminum sheet doesn't want to take: Glued on: The fillet fairing was easier (the ones further forward will be much harder): Glued on: Those four panels were not as hard as I thought they would be. Some of you might wonder why the fastener marks are so small and numerous on the fillet fairing (should it not be fastened with Cam-locs or Dzus fasteners?). No, it is fastened with flush head 3/32 rivets. As are the rest of the fillet fairings. I was surprised but the drawings don't lie. OK, so far so good. Next I must apply some P-38 filler to the areas where the larger and harder fillet fairings go. But before I can do that, and because the fin leading edge fillet fairing spills onto a large fuselage crown panel, I must first make and install that panel. That's next. Thanks for looking in; you are watching alot of fun taking place.
- 1,636 replies
-
- scratch building
- corsair
-
(and 4 more)
Tagged with:
-
Thanks for your interest. When I first introduced 3D print parts to this model a couple years ago, I had the very same concern. I felt I could not make a decent main landing gear lower strut by any other means than some sort of mold, or 3D print. I chose 3D print, but first ordered a test part. This part: I knew this part would bear the weight and the shock from any mishandling of a pretty heavy model. Others on this site had similar concerns. So I put it to the test: That test rig has 4 pounds of weight on top of the strut, that after starting with one pound. The part ultimately supported 5 pounds of dead weight on its own and did not fracture, although it flexed for sure. I ended the test there rather than go until failure. It showed its stuff, with capability waaay beyond what it has to do. I was amazed, as well as my audience. So, the lesson is this stuff is stronger than you might think. I will say the resin used by my supplier is a high strength mix, supposedly. Carefully designed and applied, 3D print parts are just fine. For the tail gear, the carriage, fork, and tire are 3D printed: Those are stout parts I can tell you. Also the upper compression link and scissors link are 3D printed, shown in this picture of the Rhino model: The upper link is nice and stout; the scissors link is so spindly and thin that it will break if you look at it sideways! However, as I explain in my short treatise on the mechanism, it is basically unloaded. As long as I can get it in there without breaking it, it's going to be fine. And I did that successfully. The shock strut, BTW, has 3D printed ends but the rest is made of aluminum tube. I am constantly amazed when I accurately scale real structural parts at 1/18 scale, 3D printed, just how efficient and strong these parts are. The best example I can show, other than the lower strut I already showed you, is this (drag struts on the main landing gear): That is a fragile part if you try to bend it. But in pure compression, it is very strong. I can tell you, the main landing gear on this model are plenty stout. So will be the tail gear. Worry not my friend!
- 1,636 replies
-
- scratch building
- corsair
-
(and 4 more)
Tagged with:
-
I have now, complements of E-bay. Now that would be a project! For my subjects however, I want to have access to alot of real definition (if not drawings, then lost of other publications where I can determine what needs to get fixed). Don't think I could find alot on the Stuka correct me if I am wrong.
- 1,636 replies
-
- scratch building
- corsair
-
(and 4 more)
Tagged with:
-
Is there a specific part you are concerned with? Or just the whole tail gear mechanism?
- 1,636 replies
-
- scratch building
- corsair
-
(and 4 more)
Tagged with:
-
This post will not be for all of you, but for those who are interested in how an aircraft landing gear works - namely the F4U tail gear - I offer my observations. For the longest time, I was a bit bewildered by the F4U tail gear. Couldn't quite figure out how it worked. Turns out it's quite simple, when you take away the arresting hook mechanism, which is right on top of it but is really independent from it. I have observations on that mechanism too, but for another time. Here is a picture of the tail gear mechanism, all by its lonesome (in Rhino 7): It is basically two links supported by a heavy bulkhead (the upper link and the "scissors link"), one of the links being collapsible in one direction (the "scissors link), so actually it is two. And these links are driven by a linear hydraulic actuator. The parts are labelled above. The carriage and shock strut are simply attached to this linkage. Note the labelled "hard points". These are fixed (non-moving) attach fittings on the fuselage. All the red circles are merely paths that joints follow as the mechanism operates. Collapsible I say? This is the key to the mechanism. Look at a close-up of the scissors link with the mechanism in an intermediate position: Note it is partly folded up around a central pivot joint, showing stop surfaces on both link halves. Those stop surfaces contact one another when the link is fully extended, preventing the link from folding in the wrong direction. Here, I show four different positions for the mechanism, with only the two links and actuator shown. Gear fully extended, 1/3 retracted, 2/3 retracted, and fully retracted: Look how the actuator changes length from fully extended to fully retracted. Look how the upper link swings back and forth. And look how the "scissors" link goes from fully extended to folded to fully extended again. These four mechanism positions overlain on top of one another: This mechanism, of course, is designed to function in two positions only - fully retracted or fully extended. All other positions are transitory. In those two positions, there is no load on the actuator. None. The weight of the aircraft, or the shock of a landing or a bump is taken purely by the carriage, the shock strut, the upper link, and to a small extent the fully extended scissors link. It's beautiful. The only way the actuator sees load is in transitional positions, where the scissors link is in a folded orientation. This means the actuator doesn't have to be very strong and heavy. Just like it's supposed to be. Also, the geometry is such that the scissors link is lightly loaded at all times. When the gear is extended, where it sees its most severe loading, the upper link and shock strut are almost in a straight line - the scissors link only makes sure the two don't collapse. When the gear is retracted, or in a transitional position, the scissors link(s) only see a factor of the dead weight of the gear carriage, the fork and the wheel/tire. That is why my scissors link is so thin and spindly looking. I have stated before that IMO the Corsair is chalk full of unnecessarily complicated contraptions ("Rube Goldberg"). But the main and tail gear - they are engineering marvels. Vought had some crack engineers in the landing gear group. Next post - fuselage skinning!
- 1,636 replies
-
- scratch building
- corsair
-
(and 4 more)
Tagged with:
-
I have been asleep at the wheel. Great updates Pete, and a great reminder on just how complex large bomb group operations were. Also, think how complicated fighter escort group operations were. Lots to go wrong; lots went wrong.
-
Your wheelhouse John. Trumpy better stock up on P-47's - this build should get alot of folks (re)interested in them. They should pay you a commission.