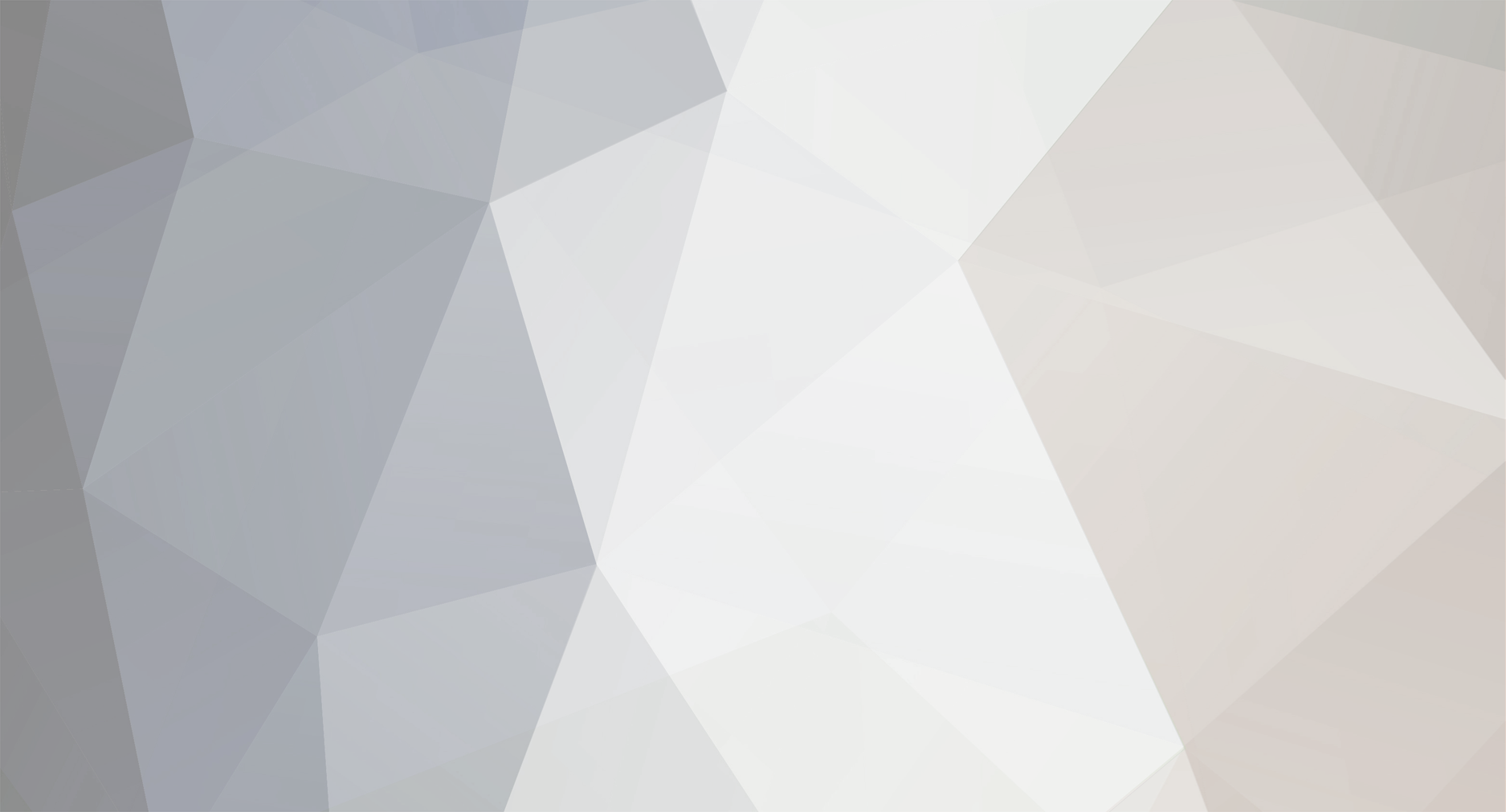
daveculp
Banned-
Posts
408 -
Joined
-
Last visited
Content Type
Profiles
Forums
Events
Everything posted by daveculp
-
1/32 Tamiya F4U-1 Birdcage Corsair
daveculp replied to curiouslysophie's topic in Ready for Inspection
It doesn't get any better than that. Looks real to me. -
The tip tanks have been installed. When I cut the original tip tanks off I got the angle wrong, so both wing tips angled inward a bit (i.e. toe-in, to use an automotive term). Since the 3D-printed trailing edges were already installed the only way to get the proper toe-in for the tip tanks was to shim the leading edge out a bit. The tanks are now aligned properly with the fuselage. It's not a big deal, but I could have saved myself some trouble by waiting until the wing assembly was glued together before cutting off the original tip tanks. One detail I discovered about the L-159 while looking at photos is that the tip tanks are not centered on the wing tips in the vertical direction. They are mounted slightly below the centerline of the wing.
- 89 replies
-
I hadn't thought of that. My plan was to glue first, then shape. I suppose I could have done most of the shaping first, then glued it on for final shaping. This is my first time shaping clear acrylic and I was worried that mechanized shaping could melt the material. I don't know if this fear is warranted, but it caused me to do the shaping with a sanding stick using single direction strokes, as with a metal file. This is why it took so long. One other problem ( a real one) I ran into was knocking the piece off while sanding. The rod is glued on with a simple butt joint, so there is no mechanical help holding it in place. I also learned that the CA needs to cure for a full day to reach adequate strength.
- 89 replies
-
The acrylic rods arrived in the mail. I now have enough 3/16 inch rod to build several hundred Honey Badgers. After a couple hours of sanding I took a break and did some coloring instead: Draken also uses a similar scheme to this one except with white/gray/black colors. The pattern is the same. I was fortunate to find enough photos on the internet to map out the pattern. The flap/aileron piece needs to be scribed to mark out the edges of the flaps and ailerons. Then the small area between the flaps and ailerons, and the small area at the outboard end of the aileron, need to have the gaps filled. I also filled the gap at the leading edge of the ailerons with thin CA to keep any light from shining through.
- 89 replies
-
You should be more careful. Maybe you can block me. Is there a way to do that here? Dave
-
Well, it came time to attach the wings to the fuselage and that's when I discovered that the wings have different dihedral angles. The right wing has a little more dihedral then the left. I thought I had measured this enough times that it was foolproof, but it made a fool of me. All is not lost though. I attached the wings with the right side shimmed upwards a little. This will hide the error by moving the error to the bottom of the airplane where all the errors can accumulate unseen. I can fair it a bit, but I expect it will always be noticeable from underneath. I'd previously decided that I'm not going to worry about the fit of the control surfaces on the bottom, so the errors are already accumulating there. -- Dave
- 89 replies
-
I think we may have already beat the http vs. https horse to death, but maybe I need to write a how-to for the "Posting Images" subforum? One thing I won't be doing is buying an https certificate for the purpose of delivering the images securely.
-
After progressively beefing up the landing gear it looks like this version will hold. I printed them in April and have had them holding up the model since then. They're still intact! This is quite a relief since the next option would be switching to a different material. I've been using PLA, and although it is easy to work with it does have a reputation for weakening over time as it absorbs moisture from the air. For non-load bearing parts this isn't a problem. The gear test was done in an upstairs bedroom so I get my dining room table back.
-
The wings are progressing. Here I'm replacing the flap fairings with 3D printed versions. The wings are almost ready for attachment to the fuselage. Three different putties in use here. The pink is Bondo two-part resin. The red is Bondo Spot and Glazing putty. The silver is Tamiya Gray putty.
- 89 replies
-
I've been using Bondo Glazing and Spot Putty. The problem is you can't scribe over it. I'm still trying out different putties. Tamiya Gray Putty is working well, but I haven't tried scribing it yet. Dave
-
Great project! I always liked the look of the Viggi. What do you use for surface smoothing after printing?
-
Thanks! Clear acrylic it is.
-
I was planning on gluing some clear sprue (which I assume is made of styrene) onto the front ends of the tip-tanks for my L-159 project, then sanding it down to final shape, then polishing. I've never done this technique before, but I see some build threads here that illustrate it. My problem is I can't find any clear sprue with large enough diameter. I need 3/16 inch (5mm) and I can't quite get there with my spare sprues. Has anyone done this technique with other forms of plastic. I can buy acrylic rods with the right diameter, but I don't know if acrylic will sand down and polish to a sheen like styrene will. My guess is that it will, but might take more time because of its hardness.
-
After staring at the vac windscreen for a while I decided I'll have to print a windscreen frame and worry about how to get the clear part to fit later. Making 3D printed parts can be an iterative process, especially when fitting to a curved or irregular surface. Here are three photos showing three of the four print iterations I had to do in order to get a good fit. The first print is a basic "geometry checker". The other prints are progressive tweaks to the part to get to the final form. In the second photo I was checking that the instrument panel, cowling and HUD didn't collide with the frame. Now I'll just putty in the gaps and prepare for more painting.
- 89 replies
-
I'm probably the only person using AC3D for CAD work, and on occasion I use FreeCAD. I've tried Blender several times, but I always give up and return to the apps I already know. CAD is definitely the barrier to 3D printing for most people. As for the printing itself I use an Elegoo Mars 2 Pro and the standard grey resin. I've never had any luck with clear resin. I built a curing box and use it a lot, but in a pinch you can always just set the parts out in the sunshine. I've tried the water-washable resin, but I found no benefit to using it, so I only use the regular (wash with Isopropyl alcohol) now. For slicing I use Chitubox, free version. It tends to be buggy, but when it works it works great and is easy to use. I do all the supports manually. PM me if you have questions. -- Dave
-
Club meeting tonight, so I brought the project along and took a picture of some parts with their general layout. Tail feathers are installed, engine inlets installed. I'm taking this opportunity to try different colors for the Honey Badger's light tan color. The under-wing fuel tanks are painted with a previous color choice which I've since decided is a bit too yellow. The fuselage is now wearing my next (final?) choice of tan - Mission Models MMP-010 Gelbbraun, yellowed a bit with some Vallejo Beige and darkened with some Vallejo USAF Tan.
- 89 replies
-
My new wings arrived today in record time! This time there will be no mistakes NOTE: Once you cut off the L-39 style tip tanks the wing parts look very similar.
- 89 replies
-
The tail end is well enough along for a photo. Still some final shaping and smoothing needed. The only photo I have of the L-159 tailpipe is a still from a youtube video, but it's enough. It looks like a tailpipe within a tailpipe, so the first tailpipe I installed, made of 3/4 inch O.D. clear acrylic tube, is actually an inner wall of the fuselage. I 3D printed the actual tailpipe and associated parts as a single piece: This is one of the most fragile and complex pieces I've printed, and it didn't come out quite right. I'll thicken up some walls, support it better and re-print. When installed it looks like this: The two ducts are probably cooling ducts to carry away some of the tailpipe heat, fed by air coming from two large NACA inlets on top of the fuselage:
- 89 replies
-
Working on three areas now: The exhaust, the inlets, and the canopy frame. The exhaust area is a bit complex, and I'll post a photo later when it looks more presentable. Now it looks mostly like a clump of Milliput. The other bits look more presentable at this point, so here are pics of the inlets and canopy frame between front and rear cockpits. I've decided both canopies need to be open. This means I have to cook up some "electronicsey" looking stuff to put into the rear cockpit. I only have one distant photo of the electronics bay to work from. The sun shade over the equipment is actually attached to the rear canopy, so I can't hide anything under it. I pre-painted the inside of the inlets, including the bare metal anti-iced inlet lip. The canopy frame is 3D printed.
- 89 replies
-
Photos work OK here. Maybe retry in a few minutes? -- Dave
-
So I tried Kevin's trick of freezing parts to make the CA glue brittle, and it definitely helped. After a lot of cutting, sawing, prying, twisting and snipping I managed to extricate the original fuselage belly from the wing structure. This will save me a lot of time later. I had believed that the L-39 vertical tail was close enough to correct height for an L-159 that I could leave it alone. Upon further review it just looks too short, so I cut off the tip and am building a new one. This is the kind of thing I'm supposed to figure out earlier in the process. I'm going to print a small extension for the rudder since the geometry is already set in CAD.
- 89 replies
-
Thanks Kevin. I recovered quickly from the wing shock, and am taking it as a blessing. Now I have time to make progress on the fuselage while I await the new kit from Tigger. There are three areas which I still haven't decided on a solution for: 1) The tailpipe - I have an acrylic tube that's the right size but too heavy. I'm still searching for a thin-walled alternative. 2) The cockpit glass is going to be tough. I might have to build up the canopy frames to get a good look and fit. I plan on making the aft canopy closed and pilot's canopy open. 3) The gear will be 3D printed. The question is will they be strong enough? We'll see. -- Dave
- 89 replies
-
With the dorsal hump done I'm starting work on the intakes. The splitter plates need to be scratch built from styrene card. I added a thin spacer where the splitter plates attach in order to move them outboard just a bit. Here I've painted the fuselage and the inboard side of the splitter plates with a primer that closely matches the final color of this area. I also clearly marked the splitter plates to avoid stupid mistakes After the splitters are installed I'll sand the intakes down on the sanding board until they fit flush. I left some extra material at the intake opening for now to keep the part strong while I sand it down. After that more putty and sanding. The tail end is progressing slowly. This end is complicated and requires several interations of putty and sanding. I used Milliput to get the basic shape of the area above the exhaust opening. I'm using Tamiya gray putty for filler work, and I use Bondo glazing and spot putty for the final shaping. The Bondo is very easy to use but it doesn't handle scribing very well, so you have to use it only for small touch-ups. Eventually it'll all come together. The control surfaces are 3D printed, and I printed them with 0.4 mm thick trailing edges. I could go even sharper than that, but I don't want them to be too delicate.
- 89 replies
-
A couple photos from my airshow/museum folders. The F-84F and the F-86. Both appear to be handed.