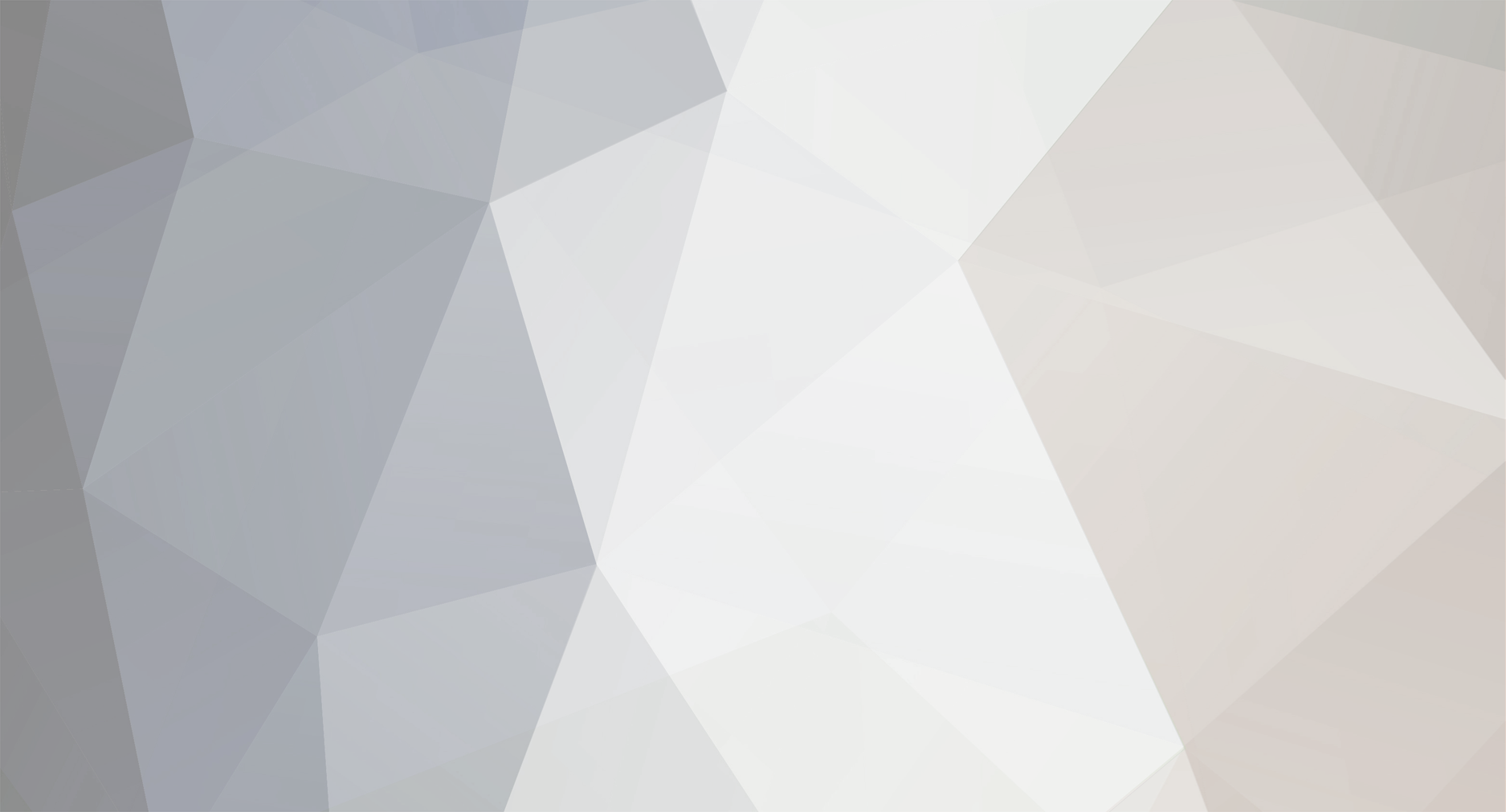
checksix
LSP_Members-
Posts
50 -
Joined
-
Last visited
-
Days Won
1
Content Type
Profiles
Forums
Events
Everything posted by checksix
-
Here's a kit I built last fall. I saved up a bunch of photos and finally had some time to edit them and post them up. Well, it looks like a B-1, but the devil is in the details. The kit is 20 years old. The parts fit is poor. Some of the panel lines are engraved (wings) but some are raised (fuselage). Many of the shapes (nose cone, tail cone, engine exhausts, external bombs) correspond to the B-1A prototype rather than the production B-1B. Nevertheless it's a good starting point and a good set of correction parts is available from the aftermarket. The box art: Quick dry fit out of the box, without the engines: I'll be using this drawing for panel line references: And this drawing for dimensional references:
-
It's difficult to tell without seeing the entire fuselage, but it looks like your nose profile is going to work! One thing I noticed is that the little cone shape at the front base of the canopy seems too exaggerated. It's actually fairly subtle, and the shape seems to carry through the canopy and matches the interior cockpit glare shield. Here's what I mean: You're going to have a great model. I'm really enjoying watching this unfold...
- 111 replies
-
- belcher bits
- hasegawa
- (and 6 more)
-
Q1: What brand of putty / filler is that you're using? Looks like it sands and blends really nice. Q2: Great pilot figure. Did it come with one of your donor kits? Q3: At one point I thought you were vac forming your canopies (thought I saw this in another thread) , but the ones in your pictures here look like they are clear parts from a kit. Is that correct? Sorry for so many Q's :) Just trying to learn new stuff here...
- 111 replies
-
- belcher bits
- hasegawa
- (and 6 more)
-
The parachute is part of the seat and the pilot sits on it. Martin-Baker has good pictures here Edit: Whoops. Wait a minute. You're doing an A model, not the C model, right? I think the A model might be using the older ejection seats (pilot wears the chute). I don't know if the A's seats were included in any of the T-38 upgrade programs.
- 111 replies
-
- belcher bits
- hasegawa
- (and 6 more)
-
Here is a photo that might help.
- 111 replies
-
- belcher bits
- hasegawa
- (and 6 more)
-
Starting to look impressive. The Talon's distinctive upturned nose shape is hard to capture correctly. It will be interesting to see how your conversion effort handles it. Keep posting, this is good stuff!
- 111 replies
-
- belcher bits
- hasegawa
- (and 6 more)
-
I've used MDF (medium density fiberboard) many times and have found that it's a pretty good alternative to wood. It's dead flat, grainless, smooth, easily cut, and takes paint nicely. After cutting and beveling, I seal it with 3 or 4 coats of polyurethane (choose water based for easy cleanup), sanding between coats. Then apply primer followed by color coat.
- 403 replies
-
- Jeff Boerboon
- N73KG
-
(and 3 more)
Tagged with:
-
I happened to notice that photobucket has recently rescinded their image ransoming blockage and that all the pictures in this thread (and many other sites) are visible again! I just finished binge-reading from beginning to end in one sitting and enjoyed it so much. This project was so well documented I felt like I was looking over your (Pete's) shoulder the whole time. I'm amazed tyou could sustain the level of concentration required to work for so many years on this without permanently burning out. Understandably you need to put it away from time to time until enthusiasm returns. Hope that's the case here. Would love to see this epic play out to the final conclusion. Thanks for sharing all your work over the years!
-
@Kagemusha: thanks for those links. Ted Taylor's article was very interesting reading. At one point in my research/experimentation I did consider trying to convert an F-5 to a T-38 and bought an old Hasegawa F-5E kit off ebay for cheap. Unfortunately I found multiple problems with this approach. While the top rear sides of the F-5E fuselage match the "coke bottle" shape of T-38, the bottom sides do not. Belcher Bits makes an F-5 E to A conversion kit which addresses this, but a more serious shape issue involves the nose. The T-38 has that delicate upturned nose while the F-5 series has a straight conical nose. Also, the cross section of the F-5 nose is elliptical, while that of the T-38 is circular. I didn't really see a way to surmount these differences without remolding the whole front fuselage, so I finally gave up. After seeing Kitty Hawk's recent F-5 release I've been so hoping for them to do a T-38. I'd buy one (or two, or ... ) in a heartbeat. But I suspect this will never happen. With few exceptions, it seems that if a jet plane doesn't shoot bullets or drop bombs or hasn't flown in a war, no major manufacturer seems interesting in kitting it. Sigh.
-
Maybe orient the damaged area facing down, cover it with a piece of tape, and inject resin upward through a hole pierced through the tape. Then let gravity form a puddle on the interior of the cowl?
- 403 replies
-
- Jeff Boerboon
- N73KG
-
(and 3 more)
Tagged with:
-
What next? Well, that's my story so far. Hope you've all enjoyed it. For most of you, this would be the starting point where you begin to apply your magic: a blank canvas ready for camo, panel lines, weathering, etc.. For me, this might be the stopping point. I can't decide whether /or/ how to proceed. I'm not really happy with the limitations imposed by a wood cockpit. The engine inlets don't look quite right. I should have vac formed a canopy frame rather than just painting it on. I'd really like to build a version with landing gear extended, canopies open, detailed cockpit, etc. etc. I'm pretty sure I'd rather not invest any more work in this particular model, and, instead, start anew with the intent of a full vac formed version. Of course, then I take look at Pete Fleichman's thread: http://forum.largescaleplanes.com/index.php?showtopic=28715&page=1 and shake my head in disbelief. For the moment then, the airframe sits in primer on my desk: Thanks for reading, and thanks for all the nice comments. --Derek
-
Cockpit Interior Now it was time to figure out how I was going to finish out the cockpit interior and attach the canopy. The first canopy came out great and fit perfectly. Then I managed to put a nasty scratch in it. So I got out the second (and last) canopy. This one I just couldn't get to fit as well as the first. The fit was good, but not perfect, and was going to require a bit of persuasion to make it conform to the fuse. My original idea was to CA the canopy in place, but given the less that perfect fit, I needed some way to attach it that provided some working time to align and finesse the placement. Epoxy seemed like the best alternative, but I was worried about a messy joint that would likely be visible behind the seam line. So I decided to create styrene "lips", carefully CA those to the bottom edges of the canopy, and then use epoxy to mount them to the edges of the fuselage.. Here the lips have been attached to the canopy, the cockpit has been boxed in with styrene, a gIare shield has been fabricated from sheet aluminum / styrene laminate, and pins have been installed where the pilots will be attached to the floor: At this point I was a little bummed, because the thickness of the cockpit walls and floor was way out of scale due to the thickness of the wood. I couldn't really thin out the wood any more without danger of piercing or warping it, so I was kind of stuck. This would definitely not be a scale cockpit . Nevertheless, I decided to proceed and see what could be done. Some simple instrument panels were fabricated: The cockpit was sprayed light gray. Pilots, joysticks, and (non-scale) seatbacks were installed, and the canopy was epoxied in place. A combination of tape and wood strips was used to coerce the canopy fitment. Slow cure epoxy allowed time to get everything aligned: After an overnight cure, the canopy was masked off and blended in to the fuselage: After more filling, sanding, and priming the airframe was finally complete: More to come...
-
Pilots This model will be posed in flight, so pilots are a must. I did a fair amount of searching for modern 1/32 USAF jet pilots and was surprised how few are available. There are all manner of WW-I, WW-II, and Korean war figures of all nationalities, but not many modern post-war US jet figures. I finally found one that was close to what I wanted, an F-15 "Desert War" pilot produced by Master Details, and ordered a pair. I found them to be very nice resin figures with amazing detail, right down to the zippers and zipper clasps on the g-suits. They come with a variety of heads having different combinations of visor and mask, as well as different arms with sleeves down or rolled up. There's even an O2 hose that can be flexed into whatever shape is needed. My only complaint would be that the heads are cast from some kind of pot metal (presumably to act as ballast to prevent plastic models from sitting on their tails). The resulting detail is not quite as crisp as that in the resin components and the helmet/mask areas had a slightly gritty texture that was hard to remove without further reducing the molded details. The arms come posed for a "hands on lap" position rather than "hands on throttle and stick" so a fair amount of surgery at shoulders, elbows, and fingers was required to get the pose I wanted. Thick CA was used for initial assembly. Then I filled the joints with baking soda using a small brush, gently blew off residual soda dust, and applied a single drop of super thin CA using a micro pipet applicator. The joints were finished off with some Tamiya putty that was thinned with lacquer thinner and applied with a brush. The figures were lightly sanded and primed, then colors were applied. To bring out some shadow detail, I followed up with a wash comprised of Future mixed with a few drops of flat black. Then a dusting of flat clear was sprayed on and a bit of Future was brushed on the visors to make them glossy: Instructor pilot: More to come...
-
No, not really. Sorry if I mislead anybody. As I mentioned in my initial post, this "work in progress" thread is actually a recap of work I did last winter. I had a pile of pictures and decided it would be fun to do a writeup here.
-
Wings, stabs, and tail All of the flying surfaces on the T-38 are simple trapezoids with symmetrical airfoil profiles, tapered in thickness from root to tip. I cut these from basswood sheet, sanded them to shape using thickness measurements taken from my 1/48 plastic model (scaled by a factor of 48/32 = 1.5), and epoxied them into slots cut into the fuse. Wings: After sanding with 80 grit paper on a flat plate: Tail fin: After blending and smoothing: The wings have zero degrees of dihedral and the stabs have 4 degrees of anhedral. I used a flat aluminum plate and gauge blocks to line everything up, squared to the tail fin: The T-38 uses flying stabilators - the stabilizer and elevator surfaces are combined into a single tailplane that pivots on a shaft. However, as this was going to be a desktop display model, for durability reasons I mounted the stabilators in slots rather than using shafts that might get bend or damaged during handling: More to come...
-
[ Personal side note: as I was writing the previous post, we just received word from our son, a student pilot at Columbus AFB, that he completed his first jet solo flight this afternoon. Yes, in a T-38. We're so happy for him and proud of all the hard work he's done to achieve this. ]
-
Inlets and exhausts Engine inlets and splitters were carved from basswood stock using sanding blocks, dremel tools, and files, followed by the usual priming, filling, and sanding: After gluing and bolting to the fuselage, the inlets were blended in with filler: After more sanding, priming, and filling: Exhaust cans were next: Each can was formed by mounting a basswood cube on a bolt and spinning the assembly in a drill press while shaping wiith a dremel grinder and sanding block. For now, the cans are just placeholders. Eventually they'll probably be replaced with something from a spare plastic kit (F5, maybe). The curved shrouds and corner outlets were formed from thin aluminum sheet laminated with .010" styrene. More to come...
-
Cockpit Now, another design decision: should I go the vacuum forming route and split my nice fuselage into halves for use as patterns, or should I keep the fuselage intact and continue as-is with a solid wood model? The scale skin thickness provided by vac formed styrene would allow much more detailing in the cockpit, wheel wells, and engine inlets, as well as scribed panel lines etc. But I was not confident in my ability to successfully vac form large parts with deep draws and significant undercuts. A solid wood fuse would be easier and quicker to finish. But it would be difficult to build out a nice cockpit and other details in solid wood. I finally decided to go with a solid fuse, treating this build as a "practice" run, and seeing how far I could take it without detouring off into a side project of building a vac forming machine and learning how to use it. I took a big gulp, cut off the canopy, and started hogging out the cockpit with a drill press and various dremel tools: After much grinding: More to come...
-
Canopy I'd never vacuum formed anything before, so this was new territory for me. A little research seemed to indicate that PETG is the preferred material for thermoforming clear plastic canopies so I ordered some 6"x12"x.020" sheets from ebay. Now I had to decide how to proceed: I could either form the canopy directly on the fuselage, or I could cut out the canopy portion of the fuselage and use that. I elected to form the canopy directly on the fuselage so that the canopy edges would (hopefully) blend out smoothly to match the contours of the fuse. Building a vacuum jig was simple: a rectangle of MDF with a hole cut in the center connected to my shop vac provides the base. A few layers of window screening provide a vacuum distribution system and some 1"x1" rubber window insulation provides a seat on which to lay the carrier frame for the PETG sheet, which is held in place with some metal clips. The carrier was placed on metal blocks over a cookie sheet in our kitchen oven at 320F for about 2-3/4 minutes, at which point the PETG sheet started to sag. The vacuum cleaner was switched on and, using gloves, the carrier was quickly removed from the oven and placed on the jig: The first attempt was a bust because I misaligned the carrier, but two more "pulls" were successful. I stopped after the third pull because the MDF carrier board was starting to deform from the heat. The final step was to mark the plastic for trimming. I used frisket paper to trace out the canopy outlines from the photo and transfer them to the fuselage, then put the canopy in place and applied tape over the lines: More to come...
-
Fuselage Next it was time to print out all the paper cutting templates: http://revenanteagle.org/checksix/lsp_1/cross_sections_page_0.pdf http://revenanteagle.org/checksix/lsp_1/cross_sections_page_1.pdf http://revenanteagle.org/checksix/lsp_1/cross_sections_page_2.pdf http://revenanteagle.org/checksix/lsp_1/cross_sections_page_3.pdf http://revenanteagle.org/checksix/lsp_1/cross_sections_page_4.pdf http://revenanteagle.org/checksix/lsp_1/cross_sections_page_5.pdf I sprayed the paper and wood surfaces with 3M 77 contact adhesive (rubber cement), allowed them to tack dry, and applied the paper to the wood sheets. This makes a secure bond, but the paper can easily be peeled off later after applying heat with a hair dryer or hot air gun. A jig saw was used to cut out each slab: Then the pieces were sanded to the line with a table top belt sander: The sander was a cheapo $80 unit but worked great. It's quick, accurate, produces clean square edges, and turns an otherwise tedious hand operation into a fun job. The moment of truth arrived. After all this image processing, scaling, cutting, and sanding, would the wood cross sections match the plans? Yup: After this successful test fit, the slabs were glued together using slow cure laminating epoxy (1 hour pot life, overnight cure) to ensure plenty of time was available for careful positioning. Then a surface coat of epoxy was applied to stabilize and waterproof the wood grain. Milliput was used to fill in the "staircase" and provide the initial base for subsequent smoothing. I found the best (albeit messy) way to apply Milliput is to push it around in small dabs using wet fingers: Next, the fuselage halves were faced internally with .010" styrene sheet to give a clean separation plane and then mated together without glue, using internal metal dowel pins to maintain alignment and a single screw to apply pressure: The plan was to fully shape and smooth the fuselage as a single piece, but allow the possibility to later cleanly pop it back apart into half-sections for use as vacuum form patterns. Multiple rounds of priming, filling, and sanding ensued: The only tool used was sandpaper strip backed with a 6" x 1/2" flexible steel ruler. 100 grit (dry) was used sparingly to knock off the initial roughness, followed by wet sanding with 320, 400, and 600 grits as the shape was refined with successive layers of primer and filler. Perhaps 10 or 12 layers were required.. A simple hot box (cardboard box with small space heater on one end) was used to speed things up, but even so, each layer required 2-3 hours to cure before the next round of sanding could begin. Eventually, something resembling a Talon emerged: More to follow...
-
Cross sections, cont'd After a session with the razor saw I've sliced the model into 62 slabs: The slabs were then arranged on the bed of my wife's HP printer/scanner and scanned into individual images. I wrote some c++ software to apply edge detection outlines and to mirror the half-sections into full sections. Here's a sample. You can see the cavity for the speed brakes and the stubs for the wing roots: Some more c++ software was written to tweak the centerings and rotations to bring all the images into alignment: Lastly, all the images were rescaled to 1/32 and printed out on paper, ready to be glued to the wood stock as cutting templates: More to follow...
-
Cross sections I decided to generate cross section images by taking a 1/48 scale plastic model, slicing it up, scanning the resulting slices, and reprinting them after upscaling. This actually turned out to be a small project all by itself. After assembling the basic parts of a Wolfpack T-38 plastic model, I carefully cut it in half and filled it with plaster of paris: I built a slicing jig consisting of a sliding tray and guides for cutting with fine tooth saw: The wings and stabs were cut down to stubs, the fuselage was placed in the wood tray, and the tray was filled with plaster: After the plaster cured, the tray was placed in the guides and carefully sliced into slabs: Each slab is .171" thick. When rescaled from 1/48 to 1/32 this will yield a slab thickness of .256" which is the thickness of the basswood stock that I'll be using for the final pattern. More to follow...
-
Plan A I was originally going to just build from a kit. A number of 1/72 and 1/48 T-38 kits are available, but these scales are just too small for my taste. I wanted something larger, easier to work on, and with more "presence". Unfortunately it seems that no manufacturer has ever produced a 1/32 kit for this subject. Well, actually a company called Collect Aire produced a resin model, but these are long out of production and, aside from an occasional (very expensive) ebay appearance, unobtainable. Plan B So I decided to build from scratch. I've built many wood and composite R/C flying models but never a static scale model. The plan was to build a wood pattern and then maybe vacuum form the fuselage from styrene sheet. More on this later. The first hurdle was to find a decent set of three view and cross section drawings. An internet search yielded little in the way of usable information, mostly variations of this: There's really not enough information here to generate the complex flowing curves of the Talon. More searching yielded this drawing from Wolfpack Design, makers of the well regarded 1/48 scale kit. I found it on their Facebook page: This is a remarkable drawing, with dimensions and station positions in decimal inches. I'm not sure if it came from Northrop or if it was produced by one of Wolfpack Design's engineers. To check the drawing for accuracy, I found a good side view photograph: And overlaid the Wolfpack drawing on the photo: The agreement was very good. So now I have a good two-view to work from, but what about cross sections? More to follow...
-
Hi all. I've lurked here on LSP for quite a while but this is my first thread in the WIP section of the forum. Last winter I built a 1/32 scale model of the US Air Force T-38C Talon jet trainer. Although the result has nowhere near the level of detail seen in the amazing models built by some of the members here, I thought I'd share my story and construction notes anyway. I'll be making several successive posts, but first, here are some pictures of the full scale subject that motivated me: More to follow...
-
Could you elaborate on your introductory post and list exactly which kit(s) you're combining to make this model? I'm new here and trying to figure out what bits and pieces you're using to do this project. Following with great interest. Thanks!