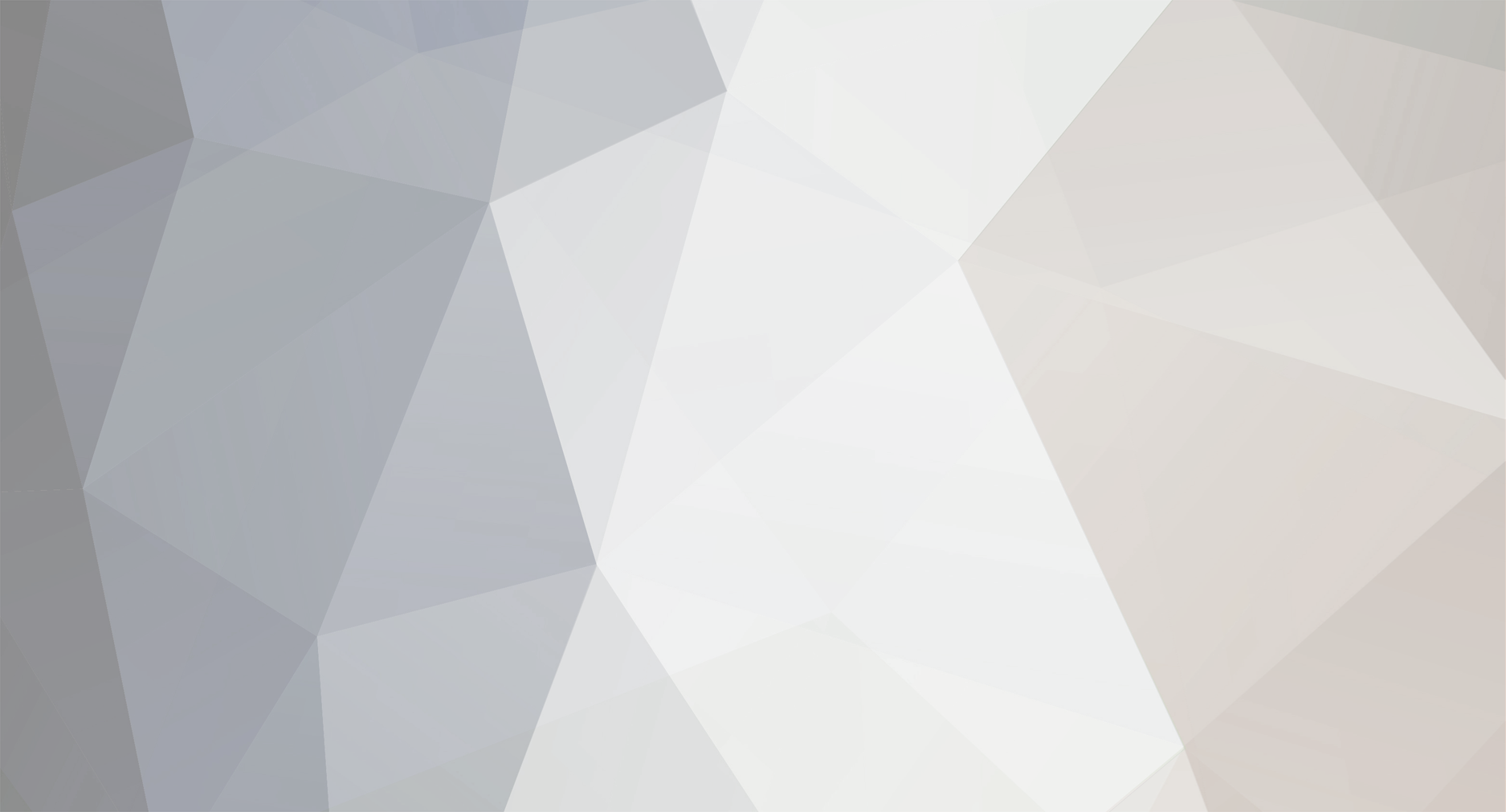
daveculp
Banned-
Posts
408 -
Joined
-
Last visited
Content Type
Profiles
Forums
Events
Everything posted by daveculp
-
This is a cross-post from my L-159 project. The question is a general one so I'm posting here to get more opinions. The issue began after I was studying photos and found one that surprised me: (original photo credit: Jan Kouba Czech republic 2013. All rights reserved.) I added the green lines and text. What surprised me is the pylons are perpendicular to the underside of the wing rather than being aligned with the vertical. In this case I figure it's about a 4 degree difference. The best explanation I've read for this comes from forum member Oldbaldguy who figures it's done to keep the pylons from being handed, so they are interchangeable left and right. That sounds like a fair explanation to me. I'm pretty sure I've seen pylons on other airplanes that are aligned with the vertical, and I'm currently pouring over my books looking for examples, but it's hard to find photos taken at just the right angle. I suppose it could vary from one airplane to the next. It might depend on the dihedral angle - too much dihedral and you have to go with handed pylons. It might have to do with weight limits on the pylon - above a certain weight the pylon needs to be vertical. Maybe it's an option for the buyer. Are there any general rules for this, or do you just have to study each airplane? I've learned that you can't trust 3-view drawings, which are really just artist's conceptions.
-
That makes perfect sense. I assume then that the sway braces in this case will also be angled 4 degrees from horizontal, and the store will hang 4 degrees off from the pylon centerline. In the photo it looks like the gun pod hangs this way.
- 89 replies
-
While I await a new kit to re-do the wings, here's the progress on the fuselage: For conversion to the L-159 type: 1. Make the exhaust area straight (parallel to red line shown) 2. Add a filet below the rudder that extends all the way back 3. Add a small fairing for a rear-facing light 4. Finish up the dorsal hump For general additional detail: 5. Cut out the NACA scoops 6. Cut out the elevators I won't print a new set of elevators until the horizontal stabs are installed. That way I'll have a final set of measurements to use. And I won't install the horizontal stabs until the aft fuselage is close to complete. While looking at photos of the L-159 on the internet I noticed something unexpected. The wing pylons seem to be perpendicular to the underside of the wing rather than parallel to the local vertical (gravity vector). It's only about 4 degrees of difference, but I wonder how common this is? Maybe it's like this on all airplanes and I just never noticed before? I've always assumed the pylons are vertical. (original photo credit: Jan Kouba Czech republic 2013. All rights reserved.)
- 89 replies
-
The lower surfaces are installed correctly, but the upper surfaces are on backwards. I then cut the upper surface ailerons and flaps off based on the location of the molded-in recess marking the aileron hinge line. Then I flipped it over and cut the bottom surface. End result is the upper surfaces are cut correctly but installed backwards. The lower surfaces are installed correctly but cut on the wrong edge.
- 89 replies
-
I installed the wings backwards. The fuselage is wider at the rear, so it can only go on one way. This is what i get for not marking the parts with an arrow pointing forward. I considered cutting the wings off, but there's enough CA glue there to hold a real L-159 together.
- 89 replies
-
The project is on hold because an unrecoverable problem appeared. While I await another vacuform kit from Tigger I'll continue to work on the fuselage. See if you can spot the problem: I need a drink.
- 89 replies
-
How did I miss the hump? It was staring right at me the whole time. Here's a shot of wing trailing edges installed and the new spine being built.
- 89 replies
-
Your're right, it does! Thanks for noticing that. I'll have to build in a hump.
- 89 replies
-
The 3D printed wing trailing edge came out just right. I've decided not to worry about weight any more. If I have to pose the airplane on a stick then so be it. Maybe I'll learn how to make brass gear. The resin parts can be scribed just like styrene. The right side is printing now. I spent much of the day carving out NACA scoops and drawing up the instrument panel decals.
- 89 replies
-
I have the cockpit roughed in and am printing up the small bits. I've made the front panel, pedestal and pedals all one piece. I've decided to make decals for the instruments, so they'll be 2-dimensional. The left console will have the throttle designed in, but the rest will be decals. I'll wait for installation until after the exterior is painted. I know one of the big chores when making a vacuform model is getting the wings and tail surfaces the right thickness, and giving the trailing edge a sharp edge. Judging by the amount of work this process has already required just for the rudder I don't think I'll have the patience to shape the wings. So, alternate plan is to cut off the trailing edge and either scratch build or print new ailerons and flaps. Either way will work. Printing them will be less work but will weigh more (and they're behind the CG). I'm inclined to print just because I like repeatable processes, but I've discovered that in the vacuform world the printed parts are all designed to fit the current model - and I don't think I could make the vac parts the same way twice. By the way, the more work I put into the rudder the more likely I'll just cut it off and make one as well. The drawing seems not quite accurate. From photos I've seen the aileron leading edges aren't swept - they go straight out just like Tigger molded them. EDIT: I later found out I had installed the upper halves of the wings on the wrong sides! Oops.
- 89 replies
-
The Honey Badger has a single seat cockpit, the rear cockpit being full of electrical equipment with a sun shade built in. Here's a photo from wiki commons (credit Thomas Del Coro): One thing to note in this image is that the rear canopy is raised up a few inches. Also, note that the crease where the fuselage side meets the canopies extends aft and disappears behind the splitter plate. So, the kit's one-piece canopy part needs to be cut up so the aft canopy can be raised. Locating the wings so I know where to cut open the fuselage. I cut out the belly of the airplane so that the wings can be attached at the correct angles. It also make it easier to install a spar. I gave the bottom of the wing 4 degrees dihedral. That should give the top surface of the wing about 1.5 degrees diredral. The wings look pretty strong, so I only need to run the spar out to the main landing gear mount points.
- 89 replies
-
Well Pete, that makes the L-39/L-159 the perfect subject for a vacuform build One other thing I've noticed while looking at online photos of the L-159 is that the part of the main gear well that contains the strut has its own set of doors (in addition to the door that's attached to the strut). I've never seen this on any other airplane. It means the belly is a smooth as can be when the gear are down. I've been racking my brain trying to figure out why it has the extra pair of doors. Maybe it's to keep the tires from throwing mud/debris up into the wells? -- Dave
- 89 replies
-
Work on the fuselage is progressing. I've printed a new nose. Getting it to fair in nicely with the fuselage will take some putty and sanding. Part of the problem is that the kit fuselage has a flat belly, whereas the real airplane has a rounded belly. I'm not going to reshape the belly, so I'll just make it work with the putty and sanding. In this photo the nose is installed and the cockpit opening is roughed out. In the mean time I've been working on the other small bits. Shown here are the seat, drop tanks, pylons (right wing only for now), missile launcher rails, sidewinder, and tip tanks. The launcher rails (LAU-7, I believe) are taken from my KH OV-10 kit. The sidewinder is from Brassin. Funny thing about the Honey Badger is I've seen photos of it sitting on the ramp with all gear doors closed. I've also seen it with some or all doors open, so I'm still trying to decide how to pose the airplane. I've decided the nose gear door will be closed, but I haven't yet decided about the main gear doors. The drop tanks are each made of two halves, top and bottom, just as you'd expect from an injection kit. That keeps the weight down but adds the difficulty of getting the seam just right. For the tip tanks I decided to print them solid, accepting the added weight. I am a bit concerned about the weight because the landing gear will be 3D printed as well, and I'm not sure how much weight they'll be able to hold. All three gear have a trailing arm design which makes it even more concerning. On the plus side all three gear can be inserted into holes in the airplane without glue, so if they break it'll be easy to remove them and replace them with gear printed with a different resin.
- 89 replies
-
I think the word I was looking for is "malleable". The material would need to be malleable to behave like a soft metal. I've started designing rigid pieces for 3D printing, and I've asked a flexible resin producer whether malleable resins exist. I'll experiment with the rigid printed parts, assuming I can print them. supporting them during printing will be tricky. Another option is to print them in rigid form and use that part to make a silicone mold. Maybe there exists a malleable, pourable resin?
-
After making wire bundles for my 1/32 OV-10 project I thought there has to be a better way. Has anyone given consideration to mass-producing these? It would have to be made of a bendable material that would hold its shape, like a soft metal would. It could perhaps be extruded like pasta. If made this way the clips/ties positioned every 20cm (at 1:1 scale) or so would be hard to add. I can 3D print a straight piece fairly easily, and given a circuitous run I can print a piece to match the run. The problem here is the resulting part will be rigid, and I don't know of any resins that will behave like a soft metal so that one could bend it to fit any path. I can print a variety of straight pieces, elbows, offsets, etc. that could be joined to make any path. The problem here is that even at 1/32 scale the pieces will be very small and hard to handle. Any ideas?
-
Tom, your browser is blocking them. Some browsers have recently shipped with a setting that blocks "mixed content", which just means it won't load http content with https content. Supposedly this is being done for security, but I believe its really being done for tracking content sources. [insert Big Tech rant here]. One solution is to find that setting and turn it off. Another solution is to use a browser which is not set up for tracking, like this one: https://dissenter.com/download
- 89 replies
-
Dooooood!!! If you can build this, you can make yer own dang seatbelts! Hahha! Yes, you're right, but I'd rather outsource that part. I really don't like making seat belts. I already ordered an aftermarket AIM-9M, and I'd like to use an aftermarket TCTS pod and the rails for both because there are some nice ones out there and it'll save me a lot of time. Unfortunately the guy who makes the TCTS pods and rails only sells on Facebook, so i'm having trouble getting in touch with him.
- 89 replies
-
A couple years ago I spotted this airplane at the Nellis AFB airshow. Obviously someone has to build one! It's an L-159 operated by Draken International. Draken calls it the Honey Badger. Tigger has a vacuform model of an L-39 in 1/32 scale, and that's close enough to a Honey Badger to be the basis for a conversion. This is my first vacuform build, so it's going to be a wild ride. The Tigger L-39 parts: Not shown here are the two copies of the canopy. The barrel looking bit at bottom right is both left and right engine inlets. The fuselage almost ready to glue together: I applied some bondo to the rudder to thicken that part up. When I sand the rudder down to give it a sharp trailing edge I want to have some material there to keep from making a hole. I'm not going to build inlet ducting, but I did add a thin inner wall that will simulate the ducting. I also (later) painted the inside of the fuselage black from there back to keep inquisitive eyes from seeing what's not there. I added a cradle to hold up the front end of the tailpipe which will be made from 3/4 inch thin plastic tube. Also added are tabs on both halves of the fuselage for gluing. I've already cut the nose off in preparation for measuring the section shape so I can 3D print a new nose. Fuselage halves joined today. I've printed up two fuel tanks, two pylons for the right wing, and an ejection seat. I plan on loading the airplane with two fuel tanks, an AIM-9M and a TCTS pod, so the outermost pylons won't be needed. I don't plan on making a centerline pylon either. There is still a lot of designing and printing to do: landing gear, nose, tip tanks, and cockpit bits. Fortunately the printed parts sit ahead of the CG, so the heavy resin parts will help keep the nose down. I already made one mistake today. I painted the seat beige as was shown in the one photo I've found of the whole seat. I think the Draken airplanes have grey seats. And speaking of the seat, does anyone know who makes the seat and whether there are any aftermarket seat belts that would fit it? Shown are the colors I'm planning to use, Vallejo 71.074 Beige, 71.125 USAF Brown, 71.056 Panzer Dk. Grey. The decals are going to be a challenge
- 89 replies
-
As far as I know they never did such a thing. I was being sarcastic. My fault.
-
Example award. They had a little problem with the glue at the bottom of the acrylic part. Is there a modeler in the house?
-
Here's a photo from last night's awards event. They only physical awards given out here were for the special categories. Most of the contest winners were announced here, but the physical awards were placed next to the models at this time. When the awards event was over the contest room was re-opened and we all went there to pack up and collect our models/awards. -- Dave
-
For those having trouble viewing photos, I recommend this browser: https://dissenter.com/download It's free and runs on the 3 popular operating systems. One problem is that it is blocked by YouTube (they'll show you endless advertisements as retribution) . The solution is to use different browsers for different things, which you really ought to do anyway for security reasons.
-
Thanks guys, it was fun, even with the masks on. The vendor area was very busy and looked like a success. The banquet was cancelled and replaced with a "cocktail hour".
-
Show's over now. The CH-54 won three(?) awards, including judges best-in-show. The egg-plane-with-bacon won first in humor. The Thunderbird F- 84 won the best Thunderbird-themed model. Some models I photographed that placed: the Flight of the Phoenix diorama, the PT-109, the Peashooter, the OV-10D, the It's a Mad, Mad, Mad World scene, the B-1.